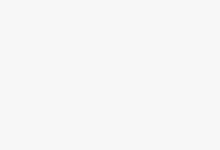
Boeing prepares to apply Intelleflex chip and Fujitsu label
[ad_1]
Quoting Ken Porad, Boeing’s project manager for the Automatic Identification Program, although there is a delay, Boeing’s plan to implement passive RFID tags to track the maintenance and repair records of its 787 aircraft parts will start in mid-2008.
In October 2007, Porad said that Boeing tested the last IC sample, which was manufactured by Intelleflex Semiconductor in Santa Clara, California. Test results show that the chip meets the storage and performance requirements established by the agreement between Boeing and the manufacturer in April 2006. According to the agreement, Intelleflex agreed to produce passive RFID tag chips with 64 kilobit memory that comply with the EPC Gen 2 standard. The chip prototype used for testing is the fourth product Intelleflex provided to Boeing. The first three products caused problems that caused the entire project to be delayed for more than a year.
Porad said that although the chip design has been completed, there are still other obstacles that need to be eliminated before suppliers can use labels on aircraft components. First, he must explain to Boeing management that passive ultra-high frequency (UHF) RFID technology is already at an “acceptable level of maturity.” He will then carry out a test to show that Boeing’s production system can accommodate RFID-tagged components without errors.
The test will select a component to be labeled, and then send the labeled component into the production process, starting from the Boeing manufacturing plant receiving the component, passing the quality assurance testing and assembly cycle, and then this component will be integrated into the aircraft body. Porad hopes that label integrators will use Intelleflex chips in component-specific RFID sample labels and can carry out this test in the second quarter of this year. Since the latest Boeing 787 was not in production at that time, it is inclined to implement it in advance on the Boeing 777.
If the test shows that the label does not have a negative impact on the production process, Boeing’s next task is to give specific instructions to its suppliers. Porad said: “The explanation will include the parts that need to be labeled and the time required, as well as the amount of storage required for each tag.” In October 2005, when Boeing first planned to use RFID tags for life cycle tracking of aircraft components At that time, it was clear that suppliers were required to apply 64-kilobyte passive UHF tags, but such tags did not exist at that time. A few months later, due to the inability to meet the time requirement for the completion of the 64-kilobyte chip tag before the fall of 20006, Boeing reduced its demand for tag memory from 64 kilobytes to 64 kilobits, which is also possible for Intelleflex. fulfilled. He said that 64 kilobits or less of memory is enough to meet the needs of parts and equipment that do not produce long and detailed maintenance records, so there is no need for large memory tags to store data. Porad believes: “There is no need to use Intelleflex64 kilobit chips on fire extinguishers.” For such items, Boeing considers using 512 bits of user memory, which is more than the traditional Gen2 tag used in the supply chain, but less than 64 kilobits.
The other is the issue of frequency spectrum. Aircraft components have a long service life, so Porad still prefers to use tags with 64 kilobytes of memory. This can now become a reality. This week, Fujitsu announced that it has developed a 64-kilobyte passive UHF tag that complies with the EPC Gen2 standard, which will be available later this year. Porad said Boeing was aware that Fujitsu was developing the label, and that it was close to completion when Fujitsu notified Boeing of the process. Fujitsu reported that it also discussed labeling matters with other companies in the aviation industry, but did not disclose the company name.
Unlike Intelleflex, Fujitsu manufactures chips as well as inlays and packaging. According to Porad, Intelleflex has contacted label manufacturers Confidex and Brady in an effort to convert their chips into entire RFID inlays, and to encapsulate these inlays to make them comply with the FAA approved by the Society of Mechanical Engineers (SAE) last year. Aviation standard AS5678. The Fujitsu chip uses FRAM technology, which has a faster data collection rate than the EEPROM used by the Intelleflex 64-kilobit chip. Porad said that in addition to high storage capacity, Fujitsu tags are more attractive to Boeing, but due to the factors of quantity and weight sensitivity, its price (not announced but will be higher than 64 kilobit tags) and weight (13.6 grams) are not conducive to Applied to some parts.
[ad_2]