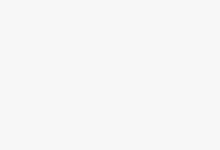
Lufthansa applies RFID technology to quickly switch cabin seats
[ad_1]
Lufthansa Technik Group used RFID technology to speed up the process of changing seats on flights from airports on all continents to Frankfurt Airport.
RFID applications help airlines to better coordinate seats between passengers. When the passengers reserve seats, the airline finds that there are no corresponding seats for the passengers. At this time, coordination can be carried out to avoid compensation for the passengers. For example, if the demand for first-class seats on a certain flight is high, Lufthansa can remove the seats from economy class in a short period of time and replace them with first-class seats. If economy class seats are sold better than first class, airlines can place more economy class seats at the last minute.
Before the implementation of this application, Lufthansa used paper and pen to record the number of rows and replacements for each seat and the seats installed on an aircraft. This process is time-consuming and troublesome, because the personnel must personally check the bottom of the seat or the row number to find the printed serial number, and then manually enter these numbers into the computer system.
Now, seats with RFID tags can solve this problem, and it is solved when workers transport them from the warehouse to the plane using vehicles. When these seats are removed from the plane and transported back to the warehouse, the tags on the seats will be read again by one of the three readers installed at the entrance of the warehouse. The focus of this application is to speed up the process of implementing seat switching. Since the tags on the seats will be read when returning to the warehouse, Lufthansa can track the application and exchange of these seats.
If they miss the departure time of the plane, the airline will be affected by the cost, so the basic work of each plane must be fast. RFID applications speed up the process of seat switching, allowing flight managers to confirm flight seats when they leave the warehouse. This confirmation is critical to ensure that all important tasks are completed before the plane takes off. If a job is not completed on time, the airline must register all affected passengers. Since February 2006, RFID applications have been implemented.
“Lufthansa has made statistics on the amount of paper used, and the cost of this application can only offset it,” said Peter Kern, a project manager of TBN. Lufthansa Technology has already implemented the application. Lufthansa spent less than US$66,770 on this application. TBN, which specializes in antenna design, provided all the hardware for this application, and a free software designer that provided software for other Lufthansa airlines provided the necessary software for the application.
Lufthansa cooperated with TBN for the first time in its seat tracking solution from June to July 2005. Lufthansa views seat tracking and modification as a significantly labor-intensive process. TBN designed the RFID application system and started to implement it at the end of 2005. Passive 13.56MHz tags conforming to the ISO15693 standard are affixed to 1,500 seats and some number of seats. These tags are provided by the Schreiner Group. The data of each tag only contains a unique ID number.
In the 3 hours before the plane lands (or 3 hours before the plane departs from Frankfurt), the airline can know whether the sales of first-class seats are less or more than expected. If the demand for first-class seats is greater than the actual availability, Lufthansa’s passenger booking system will send an electronic notification to the seat warehouse center at Frankfurt Airport.
Workers in the center of the warehouse will begin loading the seats on the trucks and then sending them to the specific aircraft for installation. These workers are also responsible for the maintenance of the seats. Transporting seats or rows of seats (these are stored underground) from the warehouse is done through a forklift, which is specially made for transporting and lifting seats and its metal wheels (about 10-15cm high). When workers drive the elevator through the entrance and exit, the reader installed on the ceiling will read the RFID tags attached to the bottom of each seat or in the plastic film on the seat row. Among them, the reader is composed of 3 custom-designed antennas. A plastic cable is clamped between the plastic film of the label, and the cable can act as a buffer between the plastic film and the bottom metal supporting the seat.
When the lift moves them, the seats and their wheels will be safely off the ground. Therefore, TDN specifically designed an RFID reader antenna that can read tags within a range of 60 cm. Before implementing the system at the airport, TDN first tested the system in its own workshop. Kern said that during the test, the deployed system achieved a 100% reading rate.
According to Kern, Lufthansa chose RFID technology because it requires a solution with little human involvement. For the same reason, the company no longer uses handheld readers in warehouses. One reason is that it is easily misplaced or left on the plane. The reader used now is the reader installed at the entrance.
According to Kern’s estimation, before the implementation of RFID technology, it would take 30 minutes to load 10 seats and collect relevant information, while it only takes 5 minutes to use RFID technology. Lufthansa plans to expand the application, in the next 2 to 3 years, select 80,000 seats to use this technology, using RFID tags to track their repair status.
[ad_2]