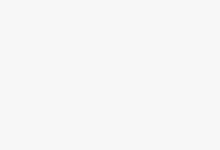
Whole-process quality tracking to ensure long-term high satisfaction of Siemens automotive customers
[ad_1]
When Siemens provides products to its automotive customers, there must be no uncertainties. In the automotive industry, safety and quality control are of paramount importance. This means that Siemens must provide full quality tracking for each part. At its fuel pump production plant in Asnières, France, Siemens uses Technifor’s Direct Part Marking (DPM) process to mark the surface of each fuel pump to ensure full quality tracking. . Siemens is also currently using Cognex’s In-Sight vision system to directly read and detect marking codes at each production point of the assembly line.
Siemens VDO (Siemens VDO) is the world’s leading supplier of automotive electronics and mechatronics. As a development partner of the automotive industry, Siemens VDO produces various types of products, including engine control electronics and fuel injection systems. When producing two different types of fuel pumps, Siemens needs to ensure that each product is marked with two different codes. The location of the code must be verified, and the code must be able to be read correctly, so that when each part passes the inspection point on the assembly line, the database will add the record that the product has been correctly marked and passed the inspection.
“100% readability”
There are two assembly lines in this Siemens fuel pump production plant. One line produces alloy fuel pumps and the other produces stainless steel fuel pumps. Both products must be marked with alphanumeric code and Datamatrix code. In order to pass the verification and record the results, the two codes on the product must also be fully readable.
Each part needs to be marked with alphanumeric code and Datamatrix code, so that each part can be identified by a special code. Once marked, the parts will go through a series of inspections and controls on the assembly line. At each stage, the code needs to be verified and read. First, the system verifies the codes to ensure that their positions are correct. Second, the system must read the code to ensure that it is clear and easy to read, which is very important. The code must also be correctly placed on the surface of the problematic part (ie, defective or difficult-to-operate part). In addition, this part must be correctly read and identified to prevent any interference to the assembly line. The customer requested a standard system of “zero unread rate”, that is, parts that failed to pass the reading must not pass through the assembly line. Even if there is only one “unread” part, it will cause manual intervention of the system, which will not only affect the environment of the “white room”, but also reduce the production speed.
Technical limitations
Technifor is responsible for marking and reading codes during the production process of fuel pumps. They decided to use the “dot peening” marking process, which is a process of marking directly on hard and metal surfaces. The surface of the fuel pump is stainless steel or aluminum, so these different surface materials increase the difficulty of marking. In addition, environmental factors must be considered, because the production process must be carried out in a “white room” environment. Reading and verifying codes under these conditions requires Technifor to have a powerful and efficient solution.
Long-term quality tracking
The last requirement of the customer is to record every production inspection, so that the problematic fuel pump can be accurately tracked at every control point. These details are recorded in a database integrated in the customer’s production operations. For example, at a checkpoint to ensure that the fuel pump does not leak, the camera will verify and read the code, and then record the products that pass the inspection at this precise point and include it in the database.
solution
Due to technical limitations and difficult operating environments, the use of machine vision systems is the only solution that the company can adopt. Cognex’s In-Sight camera is the only reliable tool used to verify and read codes, and can be used to assist in data collection. The In-Sight vision system can operate efficiently even in difficult environments. Strict restrictions in the production process make Technifor require a powerful vision system, including the marking process that must be efficient and durable. The nature of point marking also determines that they need a set of efficient visual solutions. This solution must not only be able to read the code 100%, but also be able to adapt to the environment with low contrast and low surface reflectance.
Advantage
? Efficient deployment and production process, saving time and cost
? Ensure 100% code reading rate
? Ensure integration and accurate quality tracking in Siemens’ entire auto parts production process
100% quality tracking: an effective and highly automated production process
Thanks to the powerful functions of the Cognex vision system, Siemens is able to meet the strict requirements of customers. Under the guarantee of Technifor’s “marking and reading” system based on the Cognex vision system, every part produced by Siemens can achieve full quality tracking. Siemens can assure customers that the entire production process has been strictly controlled, tested and recorded. Siemens can also guarantee that each part has achieved full quality tracking and passed the inspection. Siemens ensures that it has always been in an advantageous position in the competition by using the most high-end technology, and uses this advantage to help customers benefit.
For more information, please visit the Cognex website: www.cognex-china.com
About Cognex
Cognex Corporation specializes in the design, development, manufacturing and sales of machine vision and industrial systems or visual equipment. Cognex’s vision and ID systems are widely used in various inspection, identification and guidance applications throughout the manufacturing and distribution processes throughout the world. Cognex is a global leader in the machine vision and industrial ID industries. Since its establishment in 1981, it has installed more than 800,000 systems around the world and has earned more than $3 billion in cumulative revenue. Cognex is headquartered in Natick County, Massachusetts, with regional offices and distributors in North America, Europe, Asia, Japan and Latin America. For more information, please visit Cognex Corporation online at http://www.cognex.cn.
[ad_2]