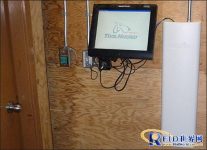
Canadian diamond mine deploys RFID system to improve tool efficiency
[ad_1]
Recently, a global diamond mining company deployed an RFID solution in a Canadian mine to better manage the use of maintenance tools. This tool and equipment traceability system is provided by ToolHound, an equipment tracking solution provider headquartered in Edmonton.The company installed a UHF at the entrance of the tool lending roomRFIDThe reader is used to record the person and time of lending the tool. ToolHound president Dean Perry said that the software allows mine managers to know the real-time status of the tool more clearly.
The mine occupies an area of two square kilometers and is located in a lake in the northwestern region. It uses wells for mining. Mining machinery is not only used for drilling, but also for collecting and transporting diamond material. In addition, the company also needs a maintenance team to be on call 24 hours a day.
The company encountered some difficulties in tool management. Workers need to use professional tools for repair and maintenance. Tool search is a major issue in the repair process of enterprises. The mine is only allowed to visit if the weather permits. Therefore, the company spends a lot of money on these tools, not only the price of the equipment itself, but also the time it takes to find the equipment.
Every mechanic carries a toolbox with basic tools, but some tasks require special tools such as wrenches, drills, or saws of a specific size. Before the RFID system was installed, the company used manual traceability tools. The mechanic needs to manually record the tool lending time and personnel information on paper. Perry said that occasionally, employees will forget to record data, and this manual system cannot provide effective management.
Perry added that no one in the mine can steal tools, so theft is not a problem. However, workers like to stock specific tools for use, which can cause companies to purchase more equipment than needed.
In July of this year, the company began to install ToolHound’s RFID solution at the entrance of the tool library. This tool magazine has two doors. An RFID reader is installed on the outermost door. Employees need to use RFID badges to enter and exit two doors. Each employee is equipped with a low-frequency RFID badge to access certain controlled areas of the mine. This badge with a unique ID number is bound to the employee identification information on the ToolHound software. Each door has an integrated badge reader.
When entering the gate, all employees need to pass through an Impinj xPortal reader with two built-in antennas. When the employee returns the tool, the reader will read the RFID tag attached to the tool and transmit it to the ToolHound software via a cable. At the same time, a list of tools lent by employees will be displayed on the touch screen based on the badge ID.
Then, the employee can operate the return item on the touch screen. In this way, the system will prompt where the tool should be stored.
At this time, employees can also borrow other items. Before leaving the tool magazine, employees need to verify again on the badge reader at the door. Then, the door lock is automatically unlocked, and the reader will automatically read the RFID tag information and display it on the touch screen.
Using this program, managers can have a clearer understanding of the use of tools, and use this to change the procurement plan. In addition, the management can also judge the length of the tool loan based on this system and set a reasonable loan period.
Perry said that most of the tools use passive EPC Gen 2 RFID tags. These labels are attached using adhesives. He also said that for those smaller tools, the company uses bar code labels. Employees can scan the barcode to determine the status of the tool.
ToolHound also provides a handheld reader for field tool positioning. Perry said that the mine currently does not use handheld readers, but the tool magazine staff will check regularly to ensure that the system is normal.
The company hopes that this system can eliminate tool hoarding and make tool use more efficient. At the same time, the company also hopes to reduce the number of tools used. Currently, the company has deployed 1,000 RFID tags and entered relevant descriptions on ToolHound.
(Exclusive manuscript of rfid world network, please indicate the source author for reprinting!)
[ad_2]