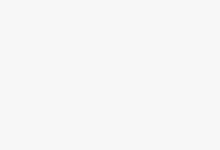
Aluminum Corporation of India uses RFID to track truck shipments
[ad_1]
Vedanta Aluminium Ltd. (VAL), a subsidiary of metals and mining company Vedanta Resources PLC, is now adopting an EPC Gen 2 ultra-high frequency (UHF) RFID system to improve work efficiency and prevent thefts at power plants and aluminum smelters in eastern India .
This system helps Vedanta prevent the theft of coal or ore. The company reports that it improves the efficiency of hundreds of contract workers and employees who enter and exit the factory every day. This EPC Gen 2 system replaces the previous RFID ID card system. The ID card of the old system must be extremely close to the reader to be read, forcing the driver to stop and hand the card to security personnel for reading.
Vedanta produces 500,000 tons of aluminum per year and also has a 1,215 MW power plant. When a contractor delivers coal to a power plant, the identity of the driver and his truck must be confirmed before the truck is authorized to enter the plant. During coal delivery, the truck must be weighed twice-the first time when the truck has just entered the factory and the other before the truck leaves-to determine how many tons of coal the truck has delivered.
The new application solution not only allows trucks and employees to quickly pass through the gate without queuing, but also provides real-time data, such as the identity of the staff and drivers at the gate at any time, and the amount of coal.
The old RFID system is difficult to read the tags embedded in the ID card. According to RK Shantosh, assistant manager of Vedanta’s IT department, all data-such as driver and company information-is stored in the card tag, not in the back-end system. In this way, Shantosh explained that the system cannot provide company management with vehicle arrival and departure data. Therefore, in March of this year, he stated that the company decided to adopt the new RFID solution and started the installation in April.
An average of 3,000 trucks enter the factory every day to transport coal and bauxite. Employees also enter and leave the factory every day. In the first phase of the application of the new system, RFID tags were installed on the windshields of cars and trucks to track the routes of employees and coal trucks at the power plant.
Due to the high metal environment-including the metal content of the windshield itself, it is difficult for the reader installed on the gate to read the label on the windshield. Therefore, the company uses a specific reader with an embedded antenna, and the antenna and the reader implement digital signal transmission (instead of the traditional analog signal through the cable). When the car is driving at 21 miles per hour, the reading distance can be as long as 50 feet.
The reader powered by the Ethernet power architecture obtains the tag ID code of each vehicle and forwards the information to a software system integrated with the SQL database at the back end of the power plant. This system includes an Apache Tomcat open-source Web server so that Vedanta can remotely control the reader. If necessary, turn off the power, reset it, and restart it.
The RFID software corresponds the ID code of each windshield tag with the name of the contractor, the description of the vehicle, and the driver. When the vehicle arrives at the gate, the security personnel only need to check the screen, compare the displayed data, including comparing the photo of the authorized person with the actual driver, etc., to determine whether to release the driver and the vehicle.
The second phase is currently still being implemented. This phase will integrate a cargo weighing system to ensure the accuracy of payment. When the truck arrives at the factory, the gross weight is first weighed, and then the tare weight of the truck is weighed when it leaves. The system corresponds these weight data to the windshield label of the vehicle. In this way, Vedanta said, the company can determine the net weight of the coal.
The last stage will integrate the picture of each license plate and match it with the ID code of the RFID tag, which will add another layer of security to ensure the correctness of the vehicle.
Vedanta reports that this system reduces the time it takes for trucks to enter the factory from 5-10 minutes to 20-25 seconds, thereby reducing vehicle fuel consumption.
“This system has been in use for three months and it has been very smooth,” Shantosh said. “We can obtain real-time data on the number of trucks, and in the future we can plan truck transportation accordingly.”
[ad_2]