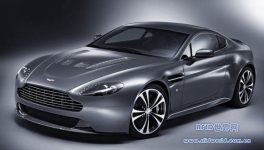
Aston Martin uses RFID to speed up the offline inspection process of racing cars
[ad_1]
Aston Martin, a high-performance automobile manufacturer, now uses RFID to track the flow of customized vehicles through the finishing line to ensure that the production of vehicles meets customer requirements.
According to Nick Lines, general manager of the company’s production engineering, the system provided by Ubisense, a real-time positioning technology company, can inform Aston Martin of the position of the vehicle in the “off the production line” (finishing) process, the time spent in each process and the location of the bottleneck. . The car manufacturer installed this real-time positioning system at the Gaydon plant in early 2009.
Aston Martin
Aston Martin only assembles 7,000 cars for the high-end market each year, and each car undergoes a rigorous test of approximately 200 working hours before being sent to customers. Each vehicle is tested on the road to evaluate the braking performance, remove the silicone from the tires, and evaluate the overall performance of the vehicle. The car will also go through the “rainy season test” in which 4,200 liters of water is poured onto the car to test the water resistance of the car. Finally, the car is sent to the “customer review line”, where the worker visually evaluates the car.
“Until all processes are completed, we can be completely assured that the car meets the high standards we set and install a signature wing badge as a proof of vehicle passing,” Lines said. During the test, however, if a vehicle is found to have a problem, the worker removes it from the test process and either sends it to a temporary parking place outdoors for refurbishment, or temporarily stores it in the factory until the problem is resolved.
Without manual inspection, it would be almost impossible to obtain visibility of the vehicle under the test line in the factory, said Richard Green, president of Ubisense. Aston Martin hopes to know the location of all vehicles in real time, the time spent in each process, and which position spent more or less time. “We are looking for a smart solution that can help us monitor the offline process of vehicles,” he said.
Now, when the vehicle is assembled and sent to the offline process, Aston Martin staff sticks a Ubisense power-powered 6-8 GHz ultra-wideband RFID tag on the inside of the vehicle’s windshield. The company installed 44 6-8 GHz Ubisense readers-Ubisensors in the finishing area and outdoor vehicle storage area of the factory.
Each tag sends its unique ID code to the reader by transmitting a series of short signals (up to one billion parts per second). Depending on whether the tag is moving or stationary, the tag sends signals at different rates. The reader then sends the ID code to the back-end WEB server. The server software analyzes the strength of the RF signal and the position of the reader, and calculates that the position of the tag is within 6 inches.
The software also corresponds the ID code of each tag to the data of the car attached, such as the vehicle identification number (VIN) and description. Every time the vehicle moves from one location to another, Green said, the new location is sent via the reader. The reader can receive tag signals up to 150 meters away outdoors, and within 60-80 meters indoors.
Aston Martin employees can then go online to check the location of the vehicle. The factory map provided by the Ubisense server identifies the location of each vehicle. The user can view the process records and time passed by a specific vehicle, and which processes have not passed. If the car deviates from the scheduled procedures-leaving the finishing line if the procedures are not completed-the system sends an alert to Aston Martin employees. Once the vehicle completes the finishing process, the tag is removed and reused in another vehicle.
“This system works very well,” Lines said, “especially locating vehicles and tracking the offline processes of vehicles, which greatly saves time and improves efficiency.”
[ad_2]