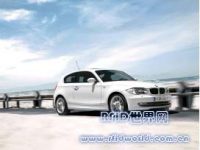
RFID enables BMW to achieve just-in-sequence supply (Just-in-Sequence)
[ad_1]
Just-in-Sequence is the key word of today’s automobile production-let the right components arrive at the right place at the right time, so that they can be installed on the right car body. Therefore, in the production process, logistics The ring is becoming more and more important. Internally, this goal can be achieved with a control system of an appropriate scale, but if the materials, modules, or the entire assembly unit are provided by external suppliers, a solution that is not affected by the plant is required. At this time, the system must be able to accurately identify various components in order to meet the expectations of the end customer, and establish a traceable quality control data file.
BMW’s Munich Plant 1.1 produces 3 brand new series of RVs and SUVs. Because BMW is fully ordering production and many of its equipment uses sophisticated electronic instruments, the assembly line has not only become the lifeline of the car, but also the correct assembly of the assembly line. The key element that determines the economic efficiency of production. As long as an error occurs during assembly, it is almost impossible to repeat it, and if the assembly line is completely wrong, the car must be scrapped.
Carsten Ranker, the control engineer in charge, emphasized: “Therefore, what we value is that each assembly line can be clearly and correctly identified when it is delivered and stored, and when it is taken out from the storage location and dispatched to the assembly process.”
Figure 1. The main model BMW series 3 produced by the Munich plant 1.1
4 plants, 1 goal: continuous control
The assembly line in the BMW factory will be individually bagged and placed in a shipping box for transportation. These bags are sewn into the mobile data storage device MDS D100. The 112-byte EEPROM of the MDS D100 will receive the necessary information so that the supplier can correctly identify the assembly line. This data storage device is the size of a credit card and is placed in a strong bag to protect the device from damage in the daily harsh industrial environment.
After delivery, these shipping boxes will be unloaded to the trough feeder in the storage location of the assembly line. During this process, the shipping boxes will pass through the read/write device SLG D10 with D5 antenna, which is installed under the conveyor. The antenna generates an inductive alternating magnetic field, which supplies power to the passive components of the data storage device, and initiates the data transmission process. As far as BMW’s assembly line is concerned, the information transmitted is a specific order number, and each ordered car will have a unique and clear number.
Based on this information, the system can store the shipping box to a designated location. If the corresponding car body is transported from the overhead storage facility to the start of the assembly line, the central computer will also dispatch the related assembly production line based on the order number, and the system will remove the assembly production line from the storage location, identify it again by the transmission platform, and then dispatch it To the assembly process. Before loading into the car body, the third station will reconfirm the data, and then clear the stored data to actively avoid future confusion.
Figure 2. The Moby system installed on the conveyor in the BMW factory
Caption: The loop antenna D5 of the Moby system installed on the conveyor is not affected by the high copper content in the wire when receiving the stored identification data.
Figure 3. The information of the assembly line will be clearly displayed on the operation panel
Caption: During storage and transportation, the information of the assembly line will be clearly displayed on the Simatic HMI operation panel.
On the Simatic HMI operation panel, the currently read order number will be clearly displayed. This operation panel can display the information of the main and auxiliary storage/transport stations. At the auxiliary station, if the assembly line has not been clearly identified before, the portable reader/writer STG D can be used for manual inspection and dispatch.
Figure 4. Manual inspection of the portable read/write device STG D
Caption: Using the handheld terminal STG D, you can also read the order number manually.
Smooth parallel operation
Moby D is not the first RFID system installed by BWM at the storage location of the Munni Black assembly line. Before launching the new three series, BMW has adopted the previous version of the system Moby L to identify the assembly line. During the transition period of 6 months, Moby L will be used in conjunction with the new system. In this way, the existing antenna can be integrated into the higher With a large loop antenna, the two systems will not interfere with each other.
During the transition period, the construction of the new system, the bus Profibus and the power supply are completely independent, so as not to affect the production operation when the Moby L system is disassembled in the future. On the control side, the already-built Simatic S7 400 can be expanded only through the bus Profibus plug-in module, which is very convenient.
For the planners of BMW control system, the use of new RFID as automation technology has obvious benefits: “BMW has a high degree of integration and standardization. If the operator of each workstation uses the same control screen, it can be Reduce the training required and reduce the error rate, thereby increasing the efficiency of the spare inventory.”
In the beginning, the RFID solution was not the first choice for copper-containing assembly lines because metal would weaken the strength of the alternating magnetic field generated by the antenna and shorten the readable distance of the data storage device. However, after many field trials, BMW has found that the reading distance is quite satisfactory. As for the conveyor system itself, only the two metal rollers within the antenna range need to be replaced with plastic rollers with corresponding thinner metal shafts.
Now, the MDS can be placed in the shipping box in any way without reading errors. Carsten Ranker talked about his experience of using Moby D in the storage location of the assembly line and said: “We handed over the components to the engineers in our plant. They installed and set up smoothly. After debugging, the system runs smoothly. During the installation of the assembly line Time provides complete protection.”
In addition to Simatic Moby D, BMW has also installed Moby E, I, R, in Factory 1.1 ─The application range covers vehicle positioning from body assembly to the work area. Following the good experience of Munich, BMW has planned to also use Moby D in the future for the identification of assembly lines in the Regensburg, Dingolfing and Leipzig plants.
About Siemens Industrial Automation Division/Industrial Automation Division
Siemens Industrial Automation Division is headquartered in Erlangen, Germany. It is a leading global supplier in the fields of manufacturing, transportation and building technology. It has complete software and hardware technologies and provides a wide range of solutions. Meet the needs of various specific industries. The Siemens Industry Automation Division (Siemens Industry Automation Division) is a leading global supplier in the fields of automation systems, low-voltage switchgear and industrial software. Its products range from standard products dedicated to manufacturing and process industries to solutions for the entire industry , Including auto manufacturing plants and chemical factory automation, to provide the most complete products and services.
[ad_2]