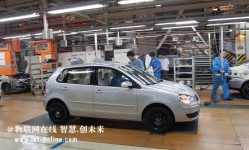
Volkswagen deploys RFID system to locate and track vehicles entering and leaving the inspection area
[ad_1]
The factory in Bratislava produces more than 1,400 cars every day, with a planned annual output of 400,000, including several models including Audi, Skoda and SEAT Mii. In the end, the inspection efficiency of the factory area greatly affects the annual output of automobiles, which is highly valued.
The car manufacturer Volkswagen’s Slovak branch uses a real-time location system (RTLS) for final inspection of vehicles that are about to leave the factory. The solution is provided by Identec Solutions. The RTLS system effectively locates vehicles that are about to leave the factory. In addition to identifying vehicles entering and leaving, it can also track parked vehicles, reducing congestion and greatly improving work efficiency.
The assembled vehicles enter the finishing area for final quality inspection before leaving the factory. If any problems are found, they will be repaired on site. The type and order of inspection vary with different models. A series of problems, such as locating a certain vehicle, guiding the vehicle to conduct inspections in order, and ensuring that the vehicle is in the plan, all require RFID systems to assist in solving them. The solution based on RFID technology not only helps workers to grasp the real-time location data of the vehicle, but also increases the virtual capacity of the sorting area.
Due to the metal structure and reading distance of the car, the RFID system can only use active RFID tags. The deployment of the RFID solution started in May 2011, and it took about 2 months to start testing in October.
The cars leaving the production line are not guided by conveyor belts or tracks during the entire process of factory inspection in the finishing area, and independently enter 15 different areas for inspection. The vehicle labeling process is carried out in the “clone zone” of the equipment line. The label is attached to the windshield near the rearview mirror. The label is the i-Q350 label provided by Identec. Prior to this, a passive tag has been affixed, and the vehicle identification code, color, manufacturing time and other information stored in the CrossTalk management system can be found through the tag code (CrossTalk system is developed by noFilis company). The RFID reader installed in the “clone zone” reads both active and passive tags at the same time, and associates the codes of the two. Through the CrossTalk management system, the designated vehicle can be located, so that the specific location of the vehicle can be easily found. In addition, an alarm will be issued when the tag is abnormally taken out of the workshop.
I-Q350 is a UHF UHF tag, powered by a lithium battery. The solution uses Identec’s i-Port M350 reader, with a reading distance of up to 500 meters and 100% coverage of the entire finishing area. The tag can receive the 2.45GHz signal from the i-SAT node in the parking area and the 125KHz signal from the i-Mark positioning. The latter is mainly used at the entrance and exit.
The assembled vehicle enters the sorting area through a passage equipped with i-mark2 or i-mark3 positioning devices. At this time, the label attached to the windshield receives the 125KHz signal from the antenna and stores the ID code of the positioning device. Then, the tag sends the code together with the tag ID to the nearest i-Port reader to record the location data. When leaving the sorting area, pass another i-mark positioning device, read its ID number, and forward the positioning.
In the open parking lot, the tag receives the 2.45 GHz signal from the i-SAT300 node, covering a distance of about 100 meters. The tag forwards the distance data from the node to the back-end analysis system, which is developed by Identec and uses a triangulation algorithm to calculate the specific location of the vehicle. The location data will be updated in the CrossTalk management software accordingly.
Before the new car leaves the factory, the i-mark positioning device will activate the i-Q350 tag, and when it passes the i-PortM350 channel reader, an alarm will be issued to remind workers to remove the i-Q350 tag.
After installing the solution, you can locate the specific vehicle location and sort out the number of vehicles in the area. Based on these data, help employees better manage the flow of vehicles in the detection area, thereby improving operational efficiency. The system test process includes the best position test for labeling. After the test, it can be installed in the upper middle of the windshield to achieve the best reading effect. In the test, it was found that the signal is easily reflected in the metal environment, and the position data cannot be accurate to within 2 meters. However, due to the large size of the car, the error can be ignored.
[ad_2]