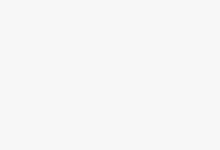
RFID auto parts container tracking application case
[ad_1]
CHEP, a provider of spare logistics materials for pallets and containers, is currently piloting RFID project technology to track the returnable containers of European auto factories. According to Floris Kleijn, RFID service director of CHEP EMEA (Europe, Middle East and Africa), FLC (Foldable) Large containers, Foldable Large Containers) industrial-grade plastic containers, used to transport suppliers’ large auto parts to the vehicle assembly plant. CHEP can issue, collect and adjust containers at its service center.
When CHEP launched this project, the company hoped that RFID container tracking would not only bring benefits to the company, but also automotive suppliers, such as improving the ability to locate goods in the supply chain. CHEP chose to implement and test the application itself before involving customers in the development and operation of the RFID system. Currently, CHEP shares information about the entry and exit of containers with customers. In the future, the company hopes to provide suppliers with RFID-based tracking services.
CHEP launched the container tracking application in actual operations in May 2008. There are now 150,000 labeled FLCs in use. The label produced by RF Identics contains the Impinj EPC Gen 2 chip and is affixed to the lower side of the container. Two barcode labels are affixed to the outside of the container, allowing operators to visually distinguish between labeled and unlabeled containers. Sirit production readers are installed in 9 factories in Germany, Hungary, Britain, Turkey, Poland, Spain and France. On average, each factory has two yard gate RFID readers, and the entire system uses a total of 14 handheld RFID readers.
The CHEP container tracking process includes four reading points, shipping, receiving, inspection and post-maintenance. First, when the labelled container loaded on the forklift passes through the yard door reader and is ready to be sent to CHEP customers (auto parts suppliers), the tags are read. The forklift driver views the SAP software work order on the touch screen of the on-board computer. The company to which the container will be sent can be identified from the number of the work order, so that the container can be matched with the customer. When empty containers are returned to CHEP, they will go through the same reverse process.
The returned container must be inspected to see if it is necessary to overhaul it. Workers scattered the containers on the floor and used handheld computers with touch screens to read tags. If any damage ring is found, the staff can select the type of damage ring through the on-screen menu and mark it in the system. Once the container is repaired, the operator uses the handheld to read the tag and record the work done. Because the system knows who the container is sent to, the company can determine the container circulation channel or collect data on damage to the ring. “Analyzing the difference in damage data, we can communicate with customers how to avoid damage,” Kleijn said, “helping eliminate unnecessary waste in the supply chain.”
The initial goal of the project is to prove that CHEP can obtain benefits from using RFID on returnable assets so that the company can start a dialogue with customers about benefits expansion. Kleijn stated that, in fact, this project provides a better responsibility ownership system for containers, including those with damaged rings, and provides CHEP with better brand recognition, which is conducive to the return of intact containers by automakers. In addition, the system makes it easier for CHEP to track maintenance and repair data. Before the implementation of RFID applications, the container (a single value of US$188) could not be individually identified.
CHEP was responsible for the implementation of the RFID project and was assisted by system integrator Infosys, who wrote software code for the application, based on Microsoft’s BizTalk and SAP’s Auto ID Infrastructure (AII) and Event Management (EM) software. CHEP’s next application challenge is to extend the project to the customer’s field.
Through the implementation of this project, CHEP provides suppliers with real-time location information of their goods in the supply chain, thereby helping them reduce inventory and respond flexibly to changes in demand. At present, this set of container RFID tracking system for auto parts is running well, and we are very satisfied. It fully demonstrates that the application of RFID can improve the efficiency of the automotive supply chain.
[ad_2]