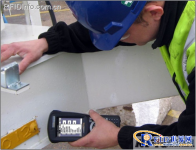
British construction company uses RFID to realize asset automation management
[ad_1]
Byrne Group, a British concrete construction company, has been using passive 125 kHz RFID tag tracking tools for three years. Now it has expanded the scope of use of the system, using the system to track users of 16,000 assets in many construction projects. Assets include heavy equipment such as excavators and trailers, as well as consumer goods such as gloves and boots. The company is also using the technology to manage online ordering of these assets.
By introducing RFID cards for 2,000 workers, Byrne Group was able to maintain an electronic record of which assets were used by which workers. In this way, the company can prevent unqualified workers from operating equipment that he has not trained, and track which consumer goods assets are used in which projects, and can identify which worker uses too much consumer goods, or which worker uses assets But it was not returned.
A Byrne worker uses a handheld RFID reader to read tags on heavy equipment
Paul Brooks, one of the managers of Byrne Group, said that the system can reduce theft and improve work efficiency, and it is expected that the cost of the expanded RFID system will be recovered next year.
In 2008, 4H Solutions, a provider of enterprise asset management solutions, provided Byrne Group with the original RFID tracking system, including Assettagz software. As of the end of last year, 4H Solutions upgraded the system and added the function of automatic ordering by installing the Plant Manager software of COINS.
Byrne Group has projects throughout the UK, including Heathrow Airport and the London Olympic Stadium. Before using RFID, the company used pen and paper to manually track various assets in different locations, and the company estimated that it would lose 100,000 pounds (US$153,000) worth of consumer goods and other items each year. The company reported that because each engineer or foreman has its own way of describing assets, not only assets are misplaced or stolen, but also assets required for a certain project are confirmed and used. This is a very important issue. Imperfect process. In addition, consumer products such as gloves and helmets and other personal protective equipment (PPE) as well as wood, gadgets and signs have not been tracked.
Initially, in 2007, the company attached low frequency (LF) 125 kHz RFID tags to all of its products. This tag works through a proprietary RFID air protocol and comes in the following forms: plastic credit card format tags for PPE, glass tags embedded in tools, and plastic molded tags for lifting equipment. The company uses Psion Teklogix’s handheld readers at Mitcham’s central cargo yard (where all equipment is stored and then shipped to the construction site). Workers can store the data of the removed equipment and the time it was taken. These assets are then transferred to a small warehouse on the construction site, waiting for distribution at any time. In August 2008, each worker in the Mitcham yard was issued an RFID ID card, which also contained a 125 kHz RFID tag.
Each asset tag is stored with a unique ID number, which corresponds to the data about the asset, and these are stored on the server hosted by 4H Solutions. This data includes very limited information about inspection records. Byrne Group hopes to get more data, such as which worker uses which piece of equipment, and whether the worker who uses the equipment has received training on the use of this piece of equipment and is qualified. The company also hopes to monitor which consumer products workers use and the quantity used. This will be able to solve the following problems, for example, which worker has taken too many gloves or other items, and track the exact number of personal protective equipment used in a certain job, so that similar jobs can be carried out smoothly in the future. In addition, the company hopes to improve its ordering system so that orders for small warehouses at each construction site can be made electronically, thereby increasing the efficiency of the ordering system and reducing errors in ordering based on telephone and paper.
Andrew Davies, sales manager of 4H Solutions, said that at the end of 2009, Byrne Group launched the next phase of deployment of the system by installing Plant Manager software to improve the inventory system. Using software running on a server hosted by 4H Solutions, Byrne Group was able to catalog all equipment, including consumer products. Therefore, workers at construction sites can use ID numbers to obtain electronic catalogs to select items and place orders.
At the Mitcham yard, workers retrieved orders and bills of lading for these assets from the server. These bills of lading are then sent to the handheld devices in the cargo yard via a wireless network connection. Use Assettagz software to compile the events read by the RFID device, and provide information and alarms based on these events. On the handheld device, the software displays the bill of lading, and workers can use the bill of lading to collect the ordered assets and then transport these assets to the construction site. When the assets were returned to the yard, a worker used a handheld device to read their tags, and the Assettagz software identified those items and indicated that they had been returned.
In addition, at the end of 2009, Byrne Group began to provide ID cards to every employee. In the warehouse of each construction site, a worker can show his ID card and use a handheld reader (two for each construction site) to read the ID card. Then the assets that the worker needs are also read, and the assets are connected to the worker’s information. If a worker is not trained to use the device, an alarm will be displayed on the screen of the handheld device to warn warehouse workers that the device cannot be used. All data is transferred from the handheld device to the server via a GPRS cellular connection.
If it is time for an asset to be inspected, the system will also display an alert so that the manager can arrange for an appropriate inspection. Inspectors can use handheld devices to read tags and their own ID cards, and follow the prompts to perform related inspections, indicating what inspections have been done and the status of the equipment.
Brooks said that as the system expanded, employees used fewer consumer products. Based on RFID data, Byrne Group now knows more accurately when a consumer product needs to be refilled in a small warehouse on a construction site. He pointed out that the company has reduced the need for reordering due to insufficient initial ordering, while also reducing the labor for searching for lost equipment and the labor for maintaining written records.
[ad_2]