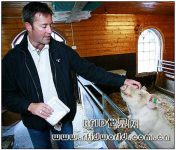
Norwegian food giant Nortura uses RFID technology to track fresh meat
[ad_1]
Nortura, Norway’s largest food supplier, will use RFID technology to track the entire process of meat from the abattoir-processing plant-store, hoping to eventually achieve the full tracking of chicken, beef, lamb and pork from birth to the table. This project cost a lot of money and is currently in the first phase of the pilot project. Nortura’s information technology subsidiary Matiq is responsible for project management. IBM provides software and integration services for this project.
A few years ago, Matiq began to study how to use RFID technology to track the process of meat from the processing plant to the store. Recently, Matiq and IBM jointly planned Nortura’s first pilot project, which will be launched in a distribution center and a supermarket in September.
Matiq President Are Bergquist and the labeling pig
Animal tracking is not a new concept for the Norwegian food industry. As part of the Norwegian government’s electronic tracking project, the government has set a deadline for the implementation of food traceability standards and policies in 2010. The government hopes to gain visibility of meat from farm to store, thereby improving food safety.
Nortura is Norway’s largest food supplier, providing 54% of consumer meat products and 73% of slaughtered animals for the country. Because the company occupies a large share of the meat market, and according to federal regulations, the company even sells part of the meat to competitors. Therefore, the meat shipped from the farm to Nortura is often shipped to another meat processing company and finally sent to the store. This process Make meat tracking more difficult.
Although the structure of the meat supply chain is complex, Matiq President Are Bergquist said that Nortura still wants to know the source and processing time of the meat, as well as the age of the animal and the feed it is fed.
This demand comes not only from the government, Bergquist said, but also from consumers and retailers, who all want to learn more about eating meat. Using the RFID tracking system, retailers can better track their inventory, ensure the freshness of the meat, and provide customers with detailed information about the meat. However, Bergquist said that so far the meat industry has rarely worked to solve this problem, mainly because the supply chain is too complicated.
“Meat tracking is a very complex issue that requires the participation of multiple parties, including farmers, processors, wholesalers, and retailers,” Bergquist said. “However, we have been discussing with IBM for some time, hoping to track animals from The whole process from birth to dinner table. Because Nortura is the country’s largest meat supplier and accounts for a large proportion of Norwegian meat production, he explained, “Matiq has a good understanding of the various steps in the supply chain and the complexity of operations. , This is our advantage. “
IBM provides Matiq with consulting, integration services and related software to help the company develop a system to share data with supply chain members. Software based on the EPCIS standard allows all parties in the supply chain to share relevant data on labels and meat products.
Norwegian meat goes through multiple steps before being sent to the retailer. Animals raised on hundreds of Norwegian farms are transported to the Nortura meat production plant for slaughter. The meat is first cut into large pieces, then cut into smaller pieces for processing, packaged and transported to multiple distribution centers, which then deliver the meat to thousands of food stores in Norway.
In the first phase of the pilot project, in Nortura’s processing plants in Tonsberg and Forus, workers stuck passive EPC G2 UHF RFID tags on plastic boxes. When sheep, cattle or pigs are slaughtered, the meat is placed in plastic boxes. When the plastic box flows through the conveyor belt, an Impinj or Intermec fixed reader reads the EPC code of the plastic box label, and associates the EPC code with the data entered by the employee. These data include farm, meat, animal age and health records. The size of the plastic box is 16*7 inches.
When the plastic box moves to the next processing station (such as cutting the meat into smaller pieces and processing), it will pass through another RFID reader, which reads the ID code of the plastic box and records the time, data and location. The processed meat is packaged and returned to the plastic box; when the meat is sent to the distribution center, the plastic box will pass through another reader, and the label will be read and recorded again. If, during processing, the meat is placed in another plastic box, then this data will also be entered into the system.
During the processing, Bergquist said that the plastic box will go through several cleaning steps and freezing environments, so the label must be very strong and durable. IBM and Matiq have tried several labels, hoping to find a label that can withstand the harsh environment of processing and cleaning. The company has not yet decided which label to use. Eventually, the company may embed the label in a plastic box.
When the plastic box leaves the processing plant and is ready to be sent to the distribution center, an RFID reader reads the tag and records the departure event. When the plastic box arrives at the distribution center and is unloaded, a reader at the warehouse door reads the label again.
When the plastic box is transported from the distribution center to the store, the readers at the entrance and exit of the distribution center and the back door of the store respectively read the tags and record related events.
According to Bergquist, RFID readers will no longer be installed in stores. The plastic boxes will be brought directly to the shop, and the empty plastic boxes will be returned to the processing plant. The information will be stored in Matiq’s data center. After authorized personnel enter the EPCIS system, they can see the data of specific goods and track specific plastic boxes and their loaded goods.
“The goal of this project is to gain full visibility into the value chain,” said Espen Braathe, IBM’s head of sensing and actuators. “In order to achieve this goal, we have to track plastic boxes all the way.”
In the end, Bergquist stated that the company hopes that animals will be tagged when they are born, so that chicken, beef, lamb and pork can be tracked from birth to dinner table.
[ad_2]