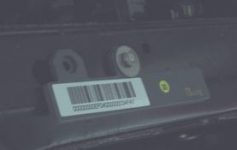
Taiwan Yulon Nissan uses RFID to improve service quality
[ad_1]
RFID is not only a cutting-edge technology, Yulon Nissan hopes that it can be used to narrow the distance with customers and improve customer satisfaction.
Company profile: Yulon Nissan is a subsidiary of the Yulon Group. Its main business is the agency and service of Nissan vehicles. In 2003, Yulon Group introduced the TOBE service of on-board computers in order to improve customer service. The car owner can use the wireless connection car machine and voice recognition to check the electronic map through wireless connection.
Question: I hope to improve customer satisfaction through individualized customer service, thereby highlighting the differentiated advantages of Yulon Nissan and other competitors.
In fact, as early as 2000, Yulon Group had adopted RFID for the first time, only for production lines. Zhan Lihong, manager of Nissan’s Information Department, said that RFID was installed in the paint tank to precisely control the paint time of each car. However, five years ago, the cost of RFID was as high as the sky-high price. Because RFID was not popular at the time, and the tags in the production process needed to resist high temperature and high oil pollution, each tag was as high as 10,000 yuan. The cost issue also made the introduction of Yulon Nissan hesitate.
However, automation technology not only helps improve operational efficiency, but also improves customer satisfaction. For the service-oriented automotive industry, this is an urgent reason. The main reason why Yulon Nissan introduced RFID this time is to improve the quality of customer service. Zhan Lihong pointed out that in the past, Yulon’s maintenance operations were not smooth, and cars often could not enter the factory smoothly during rush hours, causing the fleet to be blocked on the street. “Making customers feel welcomed is an important part of customer satisfaction,” she said.
Solution: The government pushed hard for RFID. In 2004, Yulon Nissan applied for a project subsidy from the Industrial Technology Research Institute. With the assistance of the Industrial Technology Research Institute System and Aerospace Technology Development Center, the IBM RFID solution was used to establish an RFID dynamic warranty system.
Build process:
There are many challenges in using RFID in cars. When the car is opened from the door to the maintenance personnel, the maintenance personnel can not only hold the basic customer information, but also test the scanning accuracy of RFID, the stability of network transmission and the printing speed of the printer.
First of all, how the RFID tag should be packaged and what shape has been modified many times. Luo Yifei, the project manager of the Industrial Technology Research Institute, said that he had also considered sticking it in front of the windshield, but there are aesthetic considerations. Insulation paper will also hinder the reception of radio waves, and putting it on the license plate may violate the regulations “not to deface the license plate.” Provisions. Therefore, the shape of the perforation can be hung under the fender. However, the car can be exposed to eight or nine degrees Celsius in the summer, and it may be less than ten degrees at night. Hanging under the fenders will inevitably cause oil and stone splashes. In the meantime, the Industrial Technology Research Institute has done water spraying and speed tests, so the label packaging needs to consider factors such as waterproof, high temperature, stone, oil, etc., and also meet the requirements of Yulon Nissan’s RFID signal can be read under 40 kilometers per hour. Requirements. He said that there are more than ten types of labels alone.
In addition, the specifications and placement of the Reader are also a problem. Due to the durability issue, Yulon Nissan and the Industrial Technology Research Institute decided to choose a passive tag with a frequency of 2.4 GHz that does not contain a battery. Therefore, the distance between the tag and the reader cannot exceed six meters. Does the reader have an antenna? What angle should be put and so on have to be considered. Finally, it was decided to dig a hole under the ground and cover it with a high-strength fiberglass board so as not to block the penetration of radio waves.
System build
The final product (pictured above)
The first phase of the entire system was introduced at the warranty center of Yulon Motors, one of the dealers of Yulon Nissan, located on Wenxin Road, Taichung City, and it was completed in June last year. The construction involves two parts, one part is located in the warranty center, and the other part is the customer data management system located in the Sanyi main factory in Miaoli. In the warranty factory, Yutang Warranty Center has a PC server equipped with IBM Websphere Edge Server and 13 readers, which are located under the gate, car wash, final inspection station, etc., and can read Nissan cars. RFID tags containing individual serial numbers are installed under the front fender.
At the same time, Yulon Nissan’s main plant in Sanyi, Miaoli had a Unix server, installed IBM including RFID intermediary software Websphere Premise Server, and executed database software DB2, integration software MQ Series, management software Tivoli. This system is also connected to Yulon Nissan’s distribution management system (called SmartDMS).
RFID Readers are respectively buried under the gate (top) and in front of the parking grid (bottom) in the factory.
Provide the latest car warranty status information
After the use of RFID, it has initially demonstrated the benefits of automation in the warranty service. A complete repair process is about fifty minutes. It is said that it is not long, but it is not short. “Some customers will go to the McDonald’s opposite to drink coffee, but some car owners will stay in the warranty factory.” The warranty personnel said that in the past, the warranty status was mainly used for the internal management of the warranty personnel, not for customer service, so They are all manually adjusted with a control panel similar to a whiteboard. If a customer wants to see it, he has to run into the warranty factory and compare the license plate number to know the current progress of the car.
Previously, manual and whiteboard were used to indicate the progress of the car (top), but now it can be seen on the big screen (bottom).
Now under the signal transmission of the RFID tag and the reader, the warranty status of the car will be immediately displayed on the electronic billboard in the customer lounge, and all progress can be seen at a glance in the spacious and bright lounge.
Provide individualized services
On the other hand, RFID integrated customer data system can further enhance personalized customer service. After the car owner enters the warranty factory, the RFID at the gate will detect the tag serial number and receive it through the IBM Websphere Edge Server in the factory, and connect back to the SmartDMS through the network to find out the owner’s relevant information, such as the owner’s name and insurance information , Vehicle number, preferences, etc., and then quickly return to the warranty factory. At this time, the electronic billboard on the gate will display the welcome message and the promotion plan of the day. At the same time, the maintenance staff immediately took out the note paper with the relevant information of the car owner from the printer. (As shown below)
After the car was scanned by the reader at the gate, the electronic billboard on the gate showed the welcome message and the promotion plan of the day.
Wang Yongjian, associate manager of the business planning team of Yutang Automobile, said that this step is very necessary. For example, for customers who like to bring their own fuel, the warranty personnel can ask if today is the same as usual, so that the owner does not have to re-explain their preferences, which helps to accumulate customer relations. The warranty factory can also provide promotional offers of the day based on this information.
Private issues
With the consent of the owners, Yutang Motor put up RFID tags for Nissan cars sold by the company. If a car owner who does not have a permanent tag wants to try this service temporarily, there are also temporary tags available. 170 Yulon Nissan car owners have agreed to use it.
Extended build
Each tag is 120 yuan, which is absorbed by Yutang itself. Since these are all free services, car owners are happy to accept them, and privacy concerns have not been taken into consideration. However, Yulon Nissan emphasized that the tag only contains a simple RFID tag serial number. However, the note paper printed on the hand of the customer service staff contains detailed car-related information, which can easily be lost or picked up. Therefore, Zhan Lihong said that Yulon Nissan is now also planning to replace the note paper with a PDA, which can transmit and download data through GPRS to reduce the risk of customer information leakage.
At present, only one Yutang repair center in Wenxin Road, Taichung City is the only warranty factory that deploys RFID solutions, but 11 Yutang Auto repair centers will also be deployed one after another. Yulon Nissan Motor said that the second repair center in Taipei will soon launch RFID services to serve about 3000 Yulon vehicles equipped with RFID tags in the province.
At this stage, RFID is regarded as a basic value-added service for all Yulon Motor owners, not a VIP-level car service. But Zhan Lihong said that as long as the RFID model is successful, various levels of services may be provided in the future. For example, Yulon Nissan is an agent of higher-end cars, such as TEANA owners, to provide higher-end services. Yulon Nissan also hopes that through cross-industry alliances, RFID automation can be more diversified, such as combining vehicle maintenance services and consignment management to provide value-added services for car owners.
future plan
Warranty service is only one part of Yulon Nissan’s RFID plan. Yulon Motor hopes to use the RFID system for the management of the entire life cycle. Following the introduction of RFID in the company’s Sanyi factory production line and customer-oriented front-end, Yulon Nissan also plans to extend this dynamic warranty system to the vehicle factory inspection (PDI) system in the next phase of next year, including engine testing, Inventory, finished vehicle management, etc., provide parts identification and inventory control.
Ultimately, Yulon Nissan hopes to establish an automated identification system from the front end (customer-facing) to the back end (production, shipment). Zhan Lihong said that as inventory pressure increases, it is necessary to implement full-process monitoring from front-end to back-end to achieve parts supply control, shorten operation time, reduce costs, and even implement a BTO (Built-to-order) production model.
Today’s automobile industry is no longer just a pure car sales, but also a service industry; how to ensure customer loyalty through more advanced and individualized services is the key to competition in the current automobile industry. “RFID is just the first step to improve security, convenience, and value chain efficiency.” She said.
[ad_2]