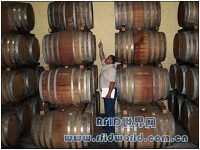
South African wine giant KWV uses electronic tags to track wine barrels
[ad_1]
South African wine giant KWV uses RFID to track and store wine or brandy barrels. The system provided by the RFID Institute uses Alien Technology’s electronic tags to help KWV track the location of the barrel, the number of times it has been used, and the time it takes to order a new barrel.
Wooden barrels are a very important asset in the wine industry. The price of each barrel is about $1,000. Tracking wooden barrels has always been a big problem for KWV. KWV’s Paarl manufacturing plant is divided into several small storage areas, which store brandy and wine respectively. Because the wooden barrel can be reused, the storage point of the wooden barrel is not fixed, but changes frequently. In the aging process, using the right barrels at the right time will affect the quality of the alcohol. However, tracking the barrels during the maturation process and the distillation process is a big problem.
Wooden barrels are a very important asset in the wine industry
When the new barrels are shipped to the manufacturing plant, KWV uses a paper recording system to assign batch numbers and track the barrels in groups. A batch of new barrels is divided into several groups, however, it is difficult for KWV to identify them. This is a big problem, because the origin and history of each barrel is crucial to the brandy and wine manufacturing business.
The forest source, wood grain and age of the barrel, the type and time of wine and brandy in the past will affect the taste and quality of the wine in the barrel. The wooden barrels will be reused many times during the 20-30 year period of use, but the wine manufacturer must track the number of times they are used, the time and the variety of wine stored each time, so as to understand the impact of the wooden barrels on the next storage. The influence of wine.
The wine is poured into wooden barrels and after several years of aging, KWV decides which batch of wine will be distilled into brandy. Brandy requires a longer maturity period-10 or 20 years. A barrel of 20-year-old brandy must undergo 8-10 barrel changes before bottling to enhance its taste.
After a year of testing and installation, KWV started to officially use the RFID system to track wooden barrels this month. KWV first affixed electronic tags to the new barrels it sent. Kevin O’Neill, a senior application engineer at the RFID Institute, said that currently KWV labels more than 70,000 barrels in several South African manufacturing plants.
When the new batch of wooden barrels arrived at the KWV Paarl factory, the plastic-wrapped wooden barrels were accompanied by a list with detailed information about the batch of wooden barrels, such as wood grain and batch identification code.
When disassembling the barrels, KMV employees put an Alien UHF EPC Gen 2 Squiggle label on the surface of each barrel, said Stephen Crocker, Alien’s director of Europe, the Middle East and Africa. The employee then uses a handheld reader (equipped with a Windows SE-based PDA) to read the ID number of each tag. The employees marked the batch number, cooperator, wood source and wood grain of the barrels according to the PDA.
KMV employees put an Alien UHF EPC Gen 2 Squiggle label on each barrel surface
The data is sent directly to the company’s SAP system through a Wi-Fi connection, and the system’s RFID Institute barrel tracking software creates a record for each barrel. In the life cycle of a wooden barrel, KWV employees can search for each wooden barrel through the ID code, query the use of the barrel, when the barrel is used, its location and usage, and the background information of the barrel, such as Coopers, etc.
The employees store the barrels on a labelled shelf. The label contains the location code of the storage area where the shelf is located and the number of rows of the shelf in the area. Employees only need to scan the RFID tags of a barrel and shelf in a batch, and the system will automatically correspond all the barrels in this batch to their locations.
When the batch of wooden barrels is filled with wine or brandy, the employee again uses the reader to read the RFID tag of the nearest barrel, which automatically includes all the barrels in this batch. The employee then enters his operation into the PDA, such as filling or emptying the barrel, and the SAP system updates this information. When a batch of wooden barrels is moved, or only some of them are removed, the employee reads the ID of the removed barrel and connects it to the new location.
O’Neill said that the system also encountered some reading problems during the test. In one test, 500 wooden barrels filled with water had readable labels; but when they were filled with wine, the labels were not readable. According to Crocker, the wine in the barrel affected the RF emissions. To this end, the RFID Institute embedded a 3 mm air bag in the tag to separate the RFID chip from the barrel. Another challenge is that the adhesive material must meet the very strict health and safety requirements of South Africa, those regulations.
After adopting this system, KWV not only locates the location of each barrel, knows the history of their use, but also understands the barrels that the company is currently lacking in a timely manner. In addition, the system can also find specific barrels for specific types of wine or brandy.
[ad_2]