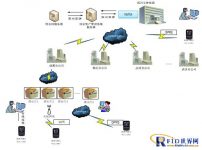
Honeywell assists Aipu Networks to achieve accurate asset management
[ad_1]
For asset-intensive enterprises, real-time grasp of the various conditions of equipment assets is undoubtedly an important goal of asset management, but the huge number of equipment makes it full of difficulties to complete this goal. In this information age, the use of information technology for asset management has become an industry trend. As the largest private broadband service provider in China, Aipu Networks needs to manage hundreds of thousands of network assets and equipment, which are widely distributed and discrete. It is a typical asset-intensive enterprise. In the past, it was difficult to use traditional manual methods for equipment management operations, with low accuracy and poor results. How to accurately manage these equipment has once become an urgent problem for the company. Under the recommendation of Beijing Netcom Jitong Technology Co., Ltd., Aipu Networks implemented a fixed asset management software system and used Honeywell’s Dolphin 6000 mobile computer for equipment management, making real-time understanding of the status of equipment and assets a whole A thing that can be easily solved.
Case background
The core business of AP Broadband is based on the IP broadband metropolitan area network, which provides high-speed fiber-optic Internet services for enterprises and residential users. Aipu Networks is the only high-tech private enterprise in Sichuan Province that has been approved to build and operate broadband IP networks in more than 20 cities across the country. It currently has Internet access services in 21 large and medium-sized cities including Chengdu, Chongqing, Wuhan, and Xi’an. Qualifications. Aipu has been successfully operating in the Chengdu market for 10 years. Its market share is second only to China Telecom, firmly occupying the second place, and it is also operating well in other cities. Up to now, online users have exceeded 70W, covering approximately 4.5 million households.
As a community broadband access service provider, Aipu Networks has hundreds of thousands of access devices in the community, such as switches, routers, electricity meters, and so on. Moreover, the layout of the equipment is scattered, the number of each point is small, and the location of the equipment is often changed due to the replacement and maintenance of the equipment, so it is very difficult for the company to count and manage these equipment. In addition, Aipu Networks has always used manual statistics of the number of equipment in the past, first by paper records and then entering the Excel table in the background for fixed asset management. The information that this statistical method can record is static and very rough. At most, it can record the location attributes of the device at the initial stage of installation. If the equipment adjustments between different communities are made due to maintenance or replacement, then record it before. The information is invalid. It is understood that only in the Chengdu area, the number of changes in Aipu’s network equipment can reach 30,000 to 50,000 per day. Not to mention that it takes a lot of repetitive work to count the equipment information again. The biggest drawback is that the accuracy of the recorded information is extremely low. Such rough information makes it impossible for Aipu to know the purchase date and warranty period of the equipment in real time, and the warranty of the equipment is also very troublesome. Although the company’s management has always wanted to grasp the company’s fixed assets data, it is difficult to achieve the goal only by relying on traditional statistical methods and table records. In order to make the company operate more efficiently, Aipu is also actively seeking solutions.
Solution design
In order to improve the efficiency of asset management and accurately understand the condition of the equipment in real time, after some comparison tests, Aipu Networks finally chose the fixed asset management solution recommended by Beijing Netcom Jitong Technology Co., Ltd. and used Honeywell Dolphin 6000 as the data Collected terminal equipment.
The solution consists of three parts: mobile data terminal equipment, fixed asset management applications and enterprise ERP (Enterprise Resource Planning) system. According to the actual business needs of Aipu Networks, Netcom Jitong recommends Aipu to use Honeywell’s mobile computer, and develops an asset management application on the mobile computer for it, which can achieve the same as Aipu’s ERP. System-UFIDA CRM software seamless data connection.
In this solution, all equipment assets of Aipu Network will be affixed with an exclusive barcode. The bar code can record very rich information: equipment purchase time, supplier, product batch, etc. The community managers of Aipu Company can count the corresponding community equipment assets through Honeywell’s mobile data terminal. After the mobile terminal scans the equipment bar code, the equipment information can be quickly entered into the fixed asset management system, and then unified transmission through GPRS and summarized to the ERP system of Aipu. The staff in the background can clearly see the condition of each equipment, which equipment is within the warranty period, which equipment has reached the time for maintenance, etc., which saves a lot of time and cost for the company’s equipment maintenance.
In addition to equipment warranty information, real-time knowledge of its location is also very important. Honeywell Dolphin 6000 comes with GPS function. Each scan of the device barcode can not only identify the information on the barcode, but also record the longitude and latitude location of the device at the same time. The collected data information is transmitted to the background via GPRS. The system, corresponding to the electronic map of the Aipu network, the staff can clearly see which cell the equipment is in which location. It is worth mentioning that Beijing Netcom Jitong Technology Co., Ltd. has successfully solved the major problem that assets cannot be accurately located due to weak or no GPS signals in the community through its excellent software development capabilities and the application of A-GPS functions. .
The completeness of equipment status and location information can not only help Aipu carry out equipment inventory, but also help them understand the working conditions of employees. When the company’s supervisors go to draw the equipment, they can understand the location and specific conditions of the equipment after scanning. If the situation of the disk draw does not match the records of the back-end system, the supervisor will communicate with the maintenance personnel, what is the reason for the discrepancy, and whether there are errors or omissions in the work, so as to improve the effectiveness of the company’s management of employees.
System inventory process: Establish an inventory plan in the Aipu fixed assets system (the fixed asset system calls the basic data of the UFIDA U8 system). Handheld PDA downloads inventory data via GPRS or WIFI or data line. After the PDA downloads the data, the operator conducts an inventory in the community. The handheld PDA automatically generates the corresponding wins and losses, and uploads them to the fixed asset system via GPRS or WIFI or a data cable to update the data of the UFIDA U8 system.
System asset inventory process: Handheld PDA downloads the latest asset basic data from the fixed asset system (the fixed asset system calls the basic data of the UF U8 system) through GPRS or WIFI or a data line. After the PDA completes the data, the operator checks the assets in the community, and through the scan, he can understand the location and specific conditions of the device. If the situation of the inventory does not match the records of the background system, what is the reason for the discrepancy of the system records, and upload the corresponding GPS coordinates and the records of the discrepancies and the reasons. (Upload via GPRS in real time, if there is no network, it will temporarily exist locally, and then upload automatically when there is a network)
At present, the use of Honeywell Dolphin 6000 to scan device barcodes has become a common task for the front-line staff of Aipu. Honeywell Dolphin 6000 will be used to scan the equipment during storage, delivery, installation and replacement, so that even if the equipment is replaced and moved, their location information can be recorded in real time and reflected in the background system , Provide detailed data information for enterprise asset management and operation.
In the past, only the rough location information of the equipment could be understood, to the detailed real-time tracking of equipment procurement, quality assurance, and location information. Now using Honeywell mobile data terminals for unified equipment inventory has become a piece of work for Aipu Networks. Very simple thing. In addition, on the basis of the asset management system, Aipu Networks has also carried out a new development of client applications. By connecting with a Bluetooth portable printer, Aipu staff can directly carry out the broadband door-to-door charging task of the community. The charging information is sent to the Bluetooth printer through the data terminal, and the charging receipt is directly printed, achieving multiple goals with one stone.
Features
Due to the huge amount of equipment to be managed and various application environments, Aipu also puts forward very high requirements on mobile data terminal equipment. According to Aipu’s own application, they tend to choose terminal products with smart phone functions. In addition to completing bar code data collection, data real-time network transmission functions and GPS positioning functions need to be run on this mobile terminal. Honeywell Dolphin 6000 products can be said to be their best choice.
Dolphin 6000 is a device that integrates smart phones, Internet phones, GPS navigation systems, and barcode scanners. It has built-in GSM/GPRS, WiFi, Bluetooth and GPS technologies, enabling operators to communicate data anytime and anywhere, obtain important information in real time via a wireless wide area network, or connect to a portable printer via Bluetooth communication. The A-GPS positioning assistance function enables the staff to know the distribution information of fixed assets well, and the integrated one-dimensional barcode scanning head can quickly and accurately scan the barcode.
Due to the special environment in which the equipment is installed, the front-line employees of Aipu Networks are often in low-light or dark working environments, so not all mobile terminal products are capable of such scanning tasks. The Honeywell Dolphin 6000 uses a laser scanning head, which can be used normally in a dark environment, and the scanning is equally accurate. And Honeywell Dolphin 6000 is compact and very durable, IP54 industrial grade, can withstand 1.2 meters of air falling to the concrete floor. For front-line workers who often travel to various communities, such a durable product can ensure the continuous and normal work, and at the same time reduce the cost of equipment maintenance and replacement.
There are still many asset-intensive companies such as Aipu Networks, and they are also facing the problem of asset statistics. The use of bar code equipment for asset management is an excellent solution. Mr. Xu Li, Director of AP Network Information Center, said: “Honeywell Dolphin 6000 products are versatile, reliable and durable, and scan fast and accurate. The implementation of data transmission and positioning functions ensures that our equipment inventory and audit work is carried out in an efficient and orderly manner. After adopting Honeywell Dolphin 6000 products, Aipu not only realized the accurate management of equipment assets, but also expanded our new services such as on-site service and instant payment on the client side, and improved the quality and level of service. In the future, we Continue to promote this application and consider using mobile computers in more cities and a wider range to improve the accuracy, efficiency and service level of our work.”
[ad_2]