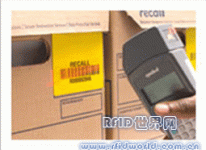
Australia Recall company uses RFID to recall cartons
[ad_1]
Recall is one of the subsidiary companies of the Australian corporate group Brambles Gmp. It has 240 service locations and 78,000 customers in 23 countries around the world. Its customer base includes public and private companies, law firms, medical providers and government agencies. Usually some documents need to be maintained to comply with regulatory requirements. The Recall company is specialized in providing file and record storage and management services.
Import RFID to inspect and label cartons
This company stores cartons of documents in the warehouse, and then the customers must send them back when they need them, and use barcodes for inventory management, but it cannot verify the correct location of the customer’s documents. Until recently, we considered the need to audit the file cartons in the warehouse, so we looked for effective methods to provide audits of customer files to assist in the execution of the company’s contractual responsibilities. Before the introduction of RFID, the way to handle audits was to require employees to move these cartons and scan the barcodes on them one by one. This is very error-prone, time-consuming and costly. Since the introduction of RFID, the company will be able to inspect the labeled cartons in the entire warehouse equipment within a few days, and can begin to provide customers with an audit report confirming the location of the cartons.
Figure 1. Recall company imported RFID in the inspection and labeling carton
Each carton is equipped with RFID tags, and each storage station has RFID reading gates and mobile interrogators, so that the company can provide customers with a new level of guaranteed service, which is the security and placement of their documents. Place it where it should be stored.
Recall’s first RFID station was chosen in the Northboro station in the Boston area, because this is a high concentration area for medical finance and legal services. The storage station is about 45,000 square meters, 6 stories high, and can accommodate 700,000 document boxes. . This company has actually used a barcode system to track the location of cartons. Each cartons has a barcode label, and there are also barcodes related to location information on the shelf. When the staff moves in or out of the cartons on the shelves, they must not only scan the barcodes on the cartons, but also read the barcodes on the shelves at the same time, and maintain this information in the Recall company’s global inventory management system. Coupled with the use of RFID, it will be possible to check and identify the location of the carton. Before the formal introduction of RFID, Recall and the CHEP expert group development team tested related technologies at the Orlando R&D Center and completed the proof-of-concept test at the Balitmore station where 5,000 document cartons were stored. During the initial test, the biggest obstacle encountered was the tag cost and reading rate. Because the documents contained in the cartons were quite thick, the reader must be able to penetrate 3 rows of cartons, but until (2006), the cost of RFID tags Significant decline and the release of the second-generation label has improved the reading rate problem.
Skinner, vice president of corporate integration at Recall, said that when the label price drops to less than 50 cents and moves toward 30 cents, the overall economic benefits are meaningful. Recall company currently uses Gen 2 UHF passive tags manufactured by KSW Microtec, each with about 30-40 points, the reading rate is greatly improved, and finally 100% accuracy rate is achieved, so that it has the ability to audit. Recall provides customers with KSW labels at Northboro station. The labels operate at frequencies from 902 to 928MH and are attached to the upper right corner of the carton. Each label contains 10 alphanumeric identification codes to match the relevant information on the barcode. It is also output by the printer.
More efficient inventory
When the carton arrives at the storage location, the first RFID reading begins. An RFID reading gate is installed at the entrance of the warehouse, provided by Venture Research. It is about 8 meters high, equipped with ThingMagic interrogators, antennas and power supplies. The RFID reading at Northboro Station The gate can read 40 cartons at the same time at one time. After checking the cartons, they are stacked on the warehouse shelves that also have labels. In order to inspect these boxes, Venture Research designed and customized mobile devices to overcome the harsh environment of the warehouse and move through narrow lanes. This mobile device has wheels. The employees call it “Sherlock” with interrogators and antennas. , Power supply and touch screen PC to run SQL database management program.
Figure 2. The interrogator on “Sherlock” can read an entire row at a time
When an employee drives a “Sherlock” through the stacked cartons, the interrogator can read the labels on a whole row of cartons at a time. At this time, the screen on the PC will flash a green light to show how many successfully read, so that the employee can continue to download A row of file reading jobs. The data collected by the audit will be merged into the Recall database. After the audit is completed, it will be uploaded from “Sherlock” to the USB flash drive, transferred to the RFID reading gate, and then transferred to the inventory management system. The audit data contains the date of the audit. Depending on how many cartons are read, this information will be added to the audit report and provided to the customer. It is expected that the audit will be conducted every 6 months.
Follow-up benefits
The future expansion plan is that the company expects to import RFID technology to warehouses across the United States, and complete the RFID equipment testing in Spain in 4 months and the feasibility of completing the labeling and auditing of the European market by the end of the year. The technology is brought to other regions to continue to be used. Recall company Skinner said: The use of RFID in the file and record management industry has endless potential value. For Recall, the key issue of RFID is how to bring the most benefits to customers in related applications. The basic driving force is to bring the most to customers. The added value of the market and make a distinction between market services.
[ad_2]