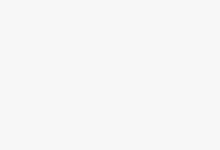
Application of Tool Recognition Technology in Aerospace Manufacturing Enterprises
[ad_1]
Tool management is an organic combination of modern management science and high-tech applications. Faced with the development and challenges of flexibility, high efficiency, high-speed machining, and multi-variable control in aerospace manufacturing enterprises, tool management has an impact on the production efficiency and manufacturing costs of the aerospace manufacturing industry. The significant impact of the company is attracting more and more senior managers’ attention and thinking. Now, more and more aerospace manufacturing companies are trying to improve the management of tools, explore new tool management models or management methods, and try to use effective tool management to greatly improve the performance and life of tools, reduce manufacturing costs, and increase productivity. And processing quality. With the continuous development of information technology, aerospace manufacturing companies have begun to use information management systems to realize the entire life cycle management of tool planning, procurement, tracking, monitoring, and scheduling. In the process of tool management, tool identification is an unavoidable problem. Especially in inventory management, there are many types of tools, a huge number, and frequent warehousing operations. If there is no effective and reliable identification technology, inventory management can easily fall into chaos. At the same time, tool identification plays a vital role in tool tracking, tracing and monitoring. Therefore, how to effectively use the identification technology is a key issue for the successful application of the tool management system.
Overview of Tool Marking Technology
The identification of traditional tool management mainly relies on barcodes, lettering or code discs on the tool holders to identify, manually enter information, and track, measure, and record the tools. With the improvement of processing efficiency and automation and more frequent tool changes, this traditional way of manually tracking tool information has been difficult to meet the current processing requirements for tool information. Therefore, the tool itself or the tool user needs an automated tool identification system, and the tool electronic tag came into being. The meaning is to identify and monitor the tools to ensure that there are suitable tools in the machining process. According to the way of reading tool data, tool identification electronic tags can be divided into contact type and non-contact type. The current main non-contact recognition technologies for tool recognition are:
(1) Bar code recognition technology in the tool management system. Barcode (BarCode) is a tool that uses a set of black and white bar symbols with different thicknesses to indicate the name, origin, price, type and other information of the tool. Bar code is by far the most economical and practical automatic identification technology. The main advantages of the tool management system are low cost and flexible application; the disadvantages are easy tearing, staining or falling off, limited information storage, and only one bar code can be identified at a time.
(2) RFID technology in the tool management system. RFID (Radio Frequency Identification Technology), commonly known as electronic tags, is an automatic identification technology that began in the 1990s and gradually matured. It uses radio frequency signals through spatial coupling (alternating magnetic fields or electromagnetic fields) to achieve contactless information transmission And through the information transmitted to achieve the identification purpose. At present, RFID technology has been widely used in industrial automation, object tracking, transportation control management, anti-counterfeiting and military applications. The main advantages of RFID technology in the application of tool management systems are pollution resistance, large readable distance, identification of high-speed moving objects, rewritable information, large storage data capacity, and the ability to identify multiple tags at the same time; its disadvantage is that the price is relatively high. At present, the lowest cost of a single RFID tag is 7 cents, which is much higher than the cost of bar codes—the lowest cost is 3 cents. Omron company uses radio frequency technology (RFID).
(3) Special recognition technology for tool management system. From the perspective of sensor applications, sensors can be divided into dedicated sensors and general-purpose sensors. For tool management systems, some companies have specially developed tool recognition sensors. For example, Pepperl+Fuchs company uses its own-developed identification sensor; Bilz company also specially developed a “tool diagnostic system” product, providing contact and non-contact sensors. The advantage of this kind of tool-specific recognition technology in the tool management system is that it is highly pertinent; the disadvantage is that it lacks versatility and is relatively expensive.
The Realization of Tool Marking Technology in Aerospace Manufacturing Enterprises
Business analysis of tool management department
In aerospace manufacturing companies, the tool management model is mainly based on the general/sub-library management: the general library is responsible for the purchase and storage of tools; the general library is responsible for the issuance of tools for individuals and departments; the workshop workers send to each sub-library Borrow and return knives.
If the general warehouse does not have the necessary tools, the general warehouse submits an application for purchase, and after approval according to the relevant procedures, the materials department will purchase it, and then enter the general warehouse after the goods arrive, and then fill in the picking list for each sub-warehouse.
Overview of Tool Management System
Aiming at the characteristics of tool management in aerospace manufacturing enterprises, and the urgent need for the establishment of enterprise digital production workshops, in accordance with the needs of the enterprise tool management department, a tool management system combining C/S and B/S structures has been established. Among them, the tool management personnel conduct management through the C/S mode, and other personnel conduct data query and sharing through the B/S structure. At the same time, it is equipped with automated three-dimensional storage equipment to meet the requirements of automated tool inventory management.
Bar code technology and coding realize tool identification
The manufacturing tasks of aerospace manufacturing enterprises belong to single-piece small batch production. In the production process of model tasks, the special requirements for the use of tools have become the key to the selection of tool identification technology. In the original tool warehouse, each type of tool is stored in a special metal box. The manager manually fills in the name and specification with an ink pen on the box, and places it in the tool cabinet. The tool is borrowed with a tool card as a voucher. Manually record it on the tool ledger. This kind of management method is relatively simple, the tool placement is not flexible, the accumulated amount of tool accounts throughout the year is relatively large, and it is quite inconvenient for the retrospective query of tool borrowing.
Therefore, aerospace manufacturing enterprises, as the defense technology industry, urgently need to improve this backward management method, and must adopt advanced tool identification technology to meet the technical needs of aerospace manufacturing. The development of aerospace models belongs to the defense technology industry and has strict confidentiality requirements. Therefore, RFID technology cannot be used in the current tool identification system of aerospace manufacturing enterprises. From the perspective of cost, the sensor method is not suitable, and its technology is not mature. Therefore, during the implementation of the tool management system, aerospace manufacturing companies consider the cost, technical maturity, and difficulty of implementation. It is a more scientific and reasonable choice to use barcode recognition technology as a tool recognition technical means. Barcode technology has the advantages of fast input speed, high reliability, economical and practical, and easy to make. There are many types of barcodes, one-dimensional and two-dimensional. One-dimensional codes include 128 codes, UPC codes, EAN-13 codes, etc. From the consideration of equipment cost and practicality, enterprises finally choose one-dimensional 128 codes as the output format of the barcode. . At the same time, considering the various types and shapes of tools involved in model tasks, in order to achieve effective management and reasonable use, reasonable coding rules must be established. The coding system of each type, each type, and each tool must be The combination of technology can realize the effective retrieval, scheduling and distribution of tools in management, and at the same time rationally arrange the production plan and purchase plan. According to the production needs of aerospace manufacturing enterprises, combined with the basic parameters of the tool itself, a coding rule that conforms to the actual situation of the enterprise is formed. In order to ensure the scalability of the coding, a spare coding field is provided in the auxiliary code part.
The tool coding rules are set as follows: the tool coding consists of four parts: the first to third parts are the main code of the tool coding, and the fourth part is the auxiliary code. The main code adopts a rigid coding system, that is, the number of digits is fixed, and the auxiliary code adopts a flexible coding method. The auxiliary code mainly describes identification features, such as tool manufacturers, industry standards, tool parameters, etc., and reflects the automatic identification of CNC tools and machining center tools. According to the requirements of production and processing, aerospace manufacturing companies choose tool specifications as the auxiliary code of the tool. After defining the tool coding rules, the operator defines a code for each type of tool. The tool bar code label is generated in batches through the tool management system. The tool bar code label is composed of five parts: tool name, tool specification, one-dimensional 128 code, tool number and purpose.
The reality of barcode technology
In order to reduce the complexity of the work of the tool managers and improve their work efficiency while realizing information management of all the tools of the application enterprise, in accordance with the defined tool coding rules, according to the types and storage locations of different tools, they are produced in accordance with the actual production of the enterprise. The required tool bar code book. Due to the wide variety of tools, divided according to usage and specifications, each warehouse has more than 5,000 types, with a total quantity of up to tens of thousands. How to obtain tool information quickly and accurately has become a difficult point for the entire project.
In order to solve the problem of tool bar code recognition, the project team has proposed a variety of solutions. Finally, according to the actual situation of the enterprise, it was unanimously approved to use a bar code book to record tool bar codes. The barcode book is designed as a 30-page loose-leaf book according to the size of A4 pages. Each page can be inserted into 20 barcode labels. The labels are marked with the tool name, specification and barcode printed by the barcode printer. According to the actual production needs, make a barcode book for each warehouse according to the types of tools, and classify the barcodes of various tools into the book to achieve the requirements of barcode scanning. Tool coding rules combined with the implementation and application of barcode scanning can match the barcode recognition system. After the barcode scanner scans the tool identification, the tool management system can identify it, automatically locate the tool, and display the relevant information of the tool. Barcode scanning replaces the original manual record borrowing/returning management method. Summary Due to the particularity of aerospace manufacturing companies, some advanced and mature recognition technologies cannot be applied to actual production for the time being. For example, wireless identification RFID based on radio frequency technology has been promoted and applied in many industries. At present, the use of barcode technology is a better choice for aerospace manufacturing companies that focus on single-piece and small-batch production. It can meet the enterprise’s need for standardized, systematic, and informatized tool management, and improve the level of automation of enterprise production assurance. It has laid a good technical foundation for the establishment of aerospace model digital production line. With the continuous development of information technology, the way of tool identification will surely change and progress with each passing day, and it will also play an active role in the advancement of science and technology in the field of aerospace engineering.
[ad_2]