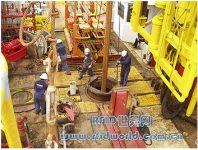
Trailblazer drilling company uses unique RFID tags to track oil drill pipes
[ad_1]
It is said that Merrick Systems’ embedded RFID tags used in oil drilling are more durable and robust than similar tag products on the market, and can withstand high and low temperatures. When in the environment of swirling flow, pressure, hot gas, abrasion, and a variety of chemical substances in the oil well, the tag still has strong adhesion to the drill pipe. Currently, this tag has been used by Trailblazer Drilling Company.
Trailblazer drilling company uses unique RFID tags to track oil drill pipes
Although many oil companies, oil drilling teams and drilling equipment providers use RFID tags to track multiple drill pipes (the drill pipes are connected to each other to form a vertical drill string for drilling), but due to the large amount of heat generated during the drilling process, Many RFID tags are affected and fail: the tags are loose or are wrapped in thick mud and cannot be read. The size of the Merrick tag is equivalent to a 25-cent coin, and the embedded position is where the drill pipe and tubing are unlikely to be damaged. The labels sold by Merrick are encapsulated with Victrex polyetheretherketone polymer, which can withstand extremely high temperatures.
Polyetheretherketone polymer is stronger than the label itself and can withstand chemicals and heat. This is an application advantage for the oil industry, said Melanie Gast, Victrex’s regional business director for oil and gas. Most plastics cannot withstand the chemicals and high temperature corrosion common in oil wells.
Merrick Systems was originally an information technology software provider, said Kemal Farid, president of Merrick Systems. In 2005, when the company entered the drilling industry, it realized the advantages of using RFID technology; Merrick Systems developed a set of software systems and RFID tags for drilling tools. The RFID tag contains a 125 kHz passive chip that complies with the ISO 18000-2 standard. According to Ian Binmore, Merrick Drilling Tool Product Supervisor, the 125 kHz frequency has a shorter reading distance, less interference in a high-metal environment, and better reading of tags in the chemical environment of drilling. Some chemicals are often used in drilling, such as drilling fluid, acidizing treatment, polymer fluid used to blast the rock, and cement for the borehole wall. In 2007, Merrick began to provide a complete set of RFID systems, including HP IPAQ handheld computers, RFID readers supplied by Ecom Instruments and other industrial providers.
Before adopting RFID technology, oil exploration and drilling companies faced several problems. They cannot know exactly where the drill bit is, how it is used, and when it is used. During the drilling process, the drill rods used to construct the drilling rig unit are stored on the support of the rig or the support of the pipe yard. In order to find the correct components of the drill string in the structure, workers often need to climb on the drill pipe rack and measure the drill pipe with a tape measure. Next, the worker writes down the specifications on a piece of paper, and then manually enters the data into the computer. In some cases, they may also spray paint on the drill pipe to identify numbers, but this is of limited use. If the drill pipe mark on the bracket is in the wrong direction, or is covered by mud or is worn out, then the incomplete mark will have no effect.
The equipment manufacturer embeds the Merrick tag in the ring storage and places it on the side of the drill pipe through its own or a third-party installer, Binmore explained. These embedded RFID tags, together with Merrick software, allow oilfield companies, drilling companies, and drilling tool rental companies to track the location of equipment, and electronically record the location of each equipment and the temperature, chemical composition, pressure, depth, and length of time in the environment. Understand the usage of the equipment. This type of tracking can help equipment users avoid accidents, such as catastrophic underground drill string collapse or fracture.
Merrick tag embedded in the ring storage
“Drilling operations are very expensive,” Kemal Farid said, costing $1 million or more per drill string. Oil wells are like screw plugs, he said, twisting and turning will damage or weaken the drill pipe. The temperature in the drill hole is as low as -320 degrees Celsius and as high as 400 degrees. The pressure per square inch exceeds 20,000 pounds. If a drill bit breaks, the entire drill string must be removed, which is very time-consuming.
Merrick tags can not only withstand high temperatures and the surrounding chemical environment, but can also be read when wrapped in thick mud
After adopting the Merrick system, drillers use computers to design the drill string they need. The drill string includes drill pipes of various sizes and joints connecting the drill pipes. All these equipment are affixed with electronic tags. Merrick software helps workers locate the unique ID number of the device they will use. Then, use the handheld reader to identify the required pipes and nodes. Each drill rod is equipped with three tags with the same ID number. The figures related to those drill pipes, such as the time and location of their use, are stored on a local server and hosted on a server managed by Merrick or the exploration company.
When the tag is read, the drill pipe or node is connected to other parts of the drill string. When the drill string begins to drill, the rig’s induction system tracks torque, shaft pressure, downhole pressure and temperature. This data is stored on a server running Merrick software. Through these data, drilling companies can understand their previous environment before reusing the drill pipe.
At the end of this year, Farid said, Merrick will install a fixed reader under the drill floor; this will read the RFID tag again when the drill pipe is placed underground. Farid also said that the company understands that the drilling industry is still interested in applying RFID tags to torque wrenches to track the torque of the bolts to prevent accidents.
[ad_2]