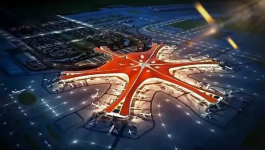
Beijing Daxing Airport RFID Equipment Operation and Maintenance Information System Project
[ad_1]
1. Project background
Beijing Daxing International Airport plans to construct 7 runways to meet the annual passenger throughput demand of 100 million passengers. According to the operational goals of 45 million passengers and 72 million passengers in 2021 and 2025, it will form a coordination with Beijing Capital International Airport in the future The development, moderate competition, and international competitiveness of the “dual hub” airport structure promotes the Beijing-Tianjin-Hebei Airport to become a world-class airport group.
Dianke Network Control participated in the construction of Beijing Daxing Airport this time, and was mainly responsible for the research and development, design, product production and system implementation of the information perception system of the cable wells, power distribution rooms and other equipment and facilities in the flight area.
2. Project overview
1 System overview
The equipment operation and maintenance information management system constructed in this project mainly uses active RFID technology to change the collection method of airport equipment inventory data and improve inventory efficiency.
Able to inquire and inspect various types of mechanical and electrical physical information of airport equipment such as weak current boxes, cabinets, servers, information screens, cameras, printers, etc., including the brand, name, model, network address, purchase date, maintenance manufacturer, and maintenance of the equipment Date, cable type, specification, direction, and the number of circuits and switches in the equipment box, etc.
It can be mastered by a handheld terminal and checked on the go, making it easier and more effective for companies to manage airport equipment. Related managers and leaders at all levels can quickly inquire and count the situation of airport equipment, so as to realize the rational allocation of resources and make decisions. Provide evidence.
2. Project implementation
According to the scale and characteristics of the project, the project team carried out a planned, organized, efficient, scientific, and coordinated management of the quality, safety, construction period and civilized construction of the project. After in-depth design, demand analysis, continuous communication, perfect improvement, and continuous optimization The perfect process has won the recognition and trust of users. The project will complete all deliveries in August 2020 and has now entered the quality assurance stage.
3. Project quality
Since the implementation of the project, with the attitude of serving customers wholeheartedly, we have used excellent technology and carefully deployed to ensure that the quality meets the needs of end users.
In the process of information system development, we always adhere to the actual needs of end users as the first principle. In addition to completing the technical specifications and conditions agreed in the contract, we should fully communicate with users to fully meet the actual needs of users. Not only make the system usable, but also It is more practical and easy to use as the high-quality requirements of the project.
[ad_2]