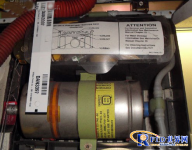
Delta Airlines uses RFID technology to inspect oxygen generators
[ad_1]
Delta Airlines uses RFID technology to improve the visibility of oxygen generators on the plane, reduce the number of generators that are lost due to premature discarding, and the time required to check the validity of the equipment. The service time of each generator is limited, generally 12-15 years. If the product is placed on the shelf in the storage room for too long, the service time of the product will be shorter. Before adopting the RFID solution, Delta Airlines estimated that up to 15% of the oxygen generator’s service life was wasted in the storage room.
In addition, the oxygen generator installed in the engine room needs to be checked regularly to determine whether it has exceeded the validity period. The inspection process requires a lot of labor. Before the implementation of the RFID system, the date check of the generator requires opening the panel above the seat. This means that many generators will be discarded before their useful life, resulting in unpredictable inventory requirements.
So far, Delta Airlines has installed Frick’s RFID tags on all oxygen generators on its 100 aircraft.
In 2011, Delta Airlines began to adopt a solution called RFID AeroCheck, which was designed and developed by two companies, Technology Solutions and Aerospace Software Developments. EPC Gen 2 passive UHF RFID tags were attached to the oxygen generators of 10 Boeing 757 aircraft, these tags were specially customized by William Frick and Co. In the past, the validity period of the generator on each aircraft required 8 person-hours; currently, through the Motorola MC9090G handheld reader and the RFID AeroCheck software that stores the generator’s tag code and validity period, the same inspection work requires only 2 employees per employee. It was successfully completed in minutes.
When starting the inspection, a list of all oxygen generators will be displayed on the handheld reader. As the generator tags are read, the list is constantly updated to find missing or expired generators. The reading distance of the tag is between 3-6 meters.
After adopting RFID technology, it only takes 45 seconds to inspect the oxygen generator of a two-aisle Boeing 777 aircraft, which is the time for the staff to walk from the cockpit to the back kitchen. Small in size, it only takes 30 seconds to inspect a single aisle aircraft. William Frick and Co.’s specially customized label inlay comes from Alien, which meets specific environmental test indicators, such as flammability and resistance to extreme temperatures, humidity and vibration. In addition to designing and producing tags, Frick will pre-encode data in accordance with industry standards EPC and Spec2000 into the RFID chip of the tag.
The RFID AeroCheck software parses the RFID data and associates the tag ID code with other information such as the oxygen generator type and expiration date. The software is not only installed in the handheld reader, but also runs on the aircraft background server. The software can track up to 32 different devices. Each tag not only records the device’s own information, but also includes its location information, such as the seat number.
The adoption of the RFID system began in 2011 and was first used on a dedicated Boeing 757 aircraft in Atlanta. According to Delta Airlines’ estimates, using RFID solutions to check the validity period of the oxygen generator saves 98% of labor time. Delta Airlines has installed RFID tags on 87 Boeing 757 aircraft (implementing more than 6000 tags) and 13 Boeing 777 aircraft (2100 tags in total).
Delta Airlines plans to expand the application of RFID technology to other equipment besides oxygen generators, such as life jackets, oxygen masks, ride manuals and other equipment that requires regular inspections.
[ad_2]