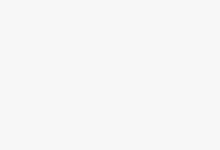
NASA uses RFID technology to obtain vibration data during the launch of space shuttles and rockets
[ad_1]
At the Kennedy Space Center in Florida and the Cape Canaveral Air Force Station at Patrick Air Force Base, the National Aeronautics and Space Administration (NASA) uses RFID technology to obtain vibration data during the launch of space shuttles and rockets, while measuring (gauge It means to set a standard, that is, to determine the corresponding relationship between the vibration mode and the sound source, so that the sound source that causes the vibration can be quickly determined by measuring the vibration in the daily analysis. The solution provided by the wireless sensor company MicroStrain uses 2.4 GHz active RFID tags with built-in sensors. They are installed at different locations around the launch pad to measure the level of vibration generated during the rocket launch. Through the analysis of the data, NASA has a deeper understanding of the sound waves generated during the launch process and predicts the potential damage caused by the sound wave vibration to the equipment and buildings in the launch center. In the future, the space agency plans to apply RFID tags with built-in pressure sensors to fuel tanks or the tracks of giant tractors that transport rockets to the launch pad.
Earlier this year, during the last space shuttle launch at the Kennedy Space Center, NASA aerospace engineers Rudy Werlink and Ravi Margasahayam tested the wireless system for the first time. Now, the two men are responsible for continuing to put the system into use at Cape Canaveral (the US Department of Defense rocket launch center).
System usage background: For decades, NASA has been studying the sound, vibration, and cumulative pressure levels that may be generated by rocket launches. Margasahayam said: It is difficult to predict the sound waves generated by the interaction between the rocket exhaust and the surrounding air, and the cumulative stress generated by the sound vibration may cause potential damage to the surrounding buildings. The goal of this research is to ensure that the equipment at the rocket launch site and surrounding buildings are safe, reliable, and easy to operate. However, the research involves a large number of equipment and buildings on a few acres of land, which is very complicated, and it is indeed difficult to achieve the above goals.
Because the rocket launch is dangerous, researchers use sensors instead of manual testing. Limitations of using wired sensors: First, NASA has limited engineers who can install wired sensors; second, the installation location of wired sensors is limited. Third, the harsh environment of the rocket launch will cause damage to the cable; in addition, the long-distance line transmission will affect the quality of the data. The Florida launch center has not only mechanical damage caused by the launch itself, but also damage from the natural environment. For example, wire-connected news camera equipment is vulnerable to attacks by American crocodiles.
System introduction and use process: Due to the installation of MicroStrain’s wireless solution, the sensor can be placed in any reasonable location, and then the data is transmitted to the data collection base station. The location of the base station is positioned in a broad field of view to maximize the reading of the system. Take the range. Although each sensor has a built-in battery, engineers also equip an external battery to increase its service life. A reader connected to a computer with MicroStrain software is responsible for collecting and storing information. Through the Ethernet connection, the data is forwarded to a web server called SensorCloud. At present, NASA has not used the Ethernet connection, but used the MicroStrain software to store the data. Once the launch is completed and the safe area is reopened, people can take out the data and analyze it.
The MicroStrain sensor includes a 2.4 GHz active RFID tag that complies with the IEEE 802.15.4 air interface protocol (the same standard as ZigBee), and has a transmission distance of up to 2 kilometers (1.2 miles). The tag receives sensor data and sends data information with a transmission rate of 256 times per second.
In May and July of this year, NASA deployed the system for the first time during the launch of the space shuttle Endeavour STS-134 and Tlantis STS-135 at the Kennedy Space Center. In these two launch missions, NASA installed three MicroStrain sensors on an aluminum plate about 7,000 feet away from the launch pad 39A. Margasahayam said: Based on this system, researchers can study the impact of far-field vibration and acoustics on buildings. Todd Nordblom, an application expert at MicroStrain, said: The reader is installed in an outbuilding about 200 feet away from the sensor.
The sensor will continue to collect data within three to five days after the launch of the rocket (because it is impossible to move the sensor device within a few days after the launch is completed), about 3GB of data is transmitted to the computer. Once the computer retrieves the data, it forwards the information to the SensorCloud server. Then use the filtering algorithm developed by MicroStrain engineers and NASA researchers to obtain key data, such as the time during which the vibration reaches a certain level during the launch.
NASA researchers calculated the peak value of the sound wave based on the measured vibration level. It is then compared with previous far-field acoustic wave estimates to determine its accuracy. The test data has a good correlation with NASA’s analysis, showing that both are reliable.
Application prospects: According to Margasahayam, the next step is to use pressure-sensing tags to measure the degree of deformation of composite overwrapped pressure vessels (COPV, used to store pressurized liquids). In addition, pressure-sensing tags can also be applied to crawler tractors responsible for transporting rockets.
In addition, the sensor can be used for operations near the launch pad. However, people are worried that during the countdown to launch, the radio frequency signal from the sensor tag will interfere with the communication between the astronaut and the ground control center. However, Margasahayam said that the technology can be improved so that as soon as the countdown starts, the remote operation stops the signal transmission of the RFID system.
[ad_2]