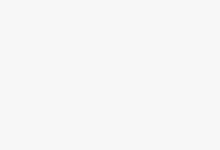
Application of Bar Code System in Manufacturing Production Flow
[ad_1]
In the automated assembly production line and each processing process, the barcode is used to label the main components, and the barcode information is collected and decoded by the barcode reader, and then the barcode information is input into the database of the computer server. Each product and main component will have a unique No matter where the product is sent, it will be recorded. If a quality problem occurs, just read the barcode on the warranty card, and then you can call up the product’s related information in the database, which facilitates product quality tracking and after-sales service.
1. Quality tracking:
By recording and tracking the production site, production date, team production line, PCB board version number, batch number and serial number of the whole machine and main components, the quantity, time, operator and machine number of each link of the production material, etc., a good establishment is established Traceability-can be traced from the finished product to the raw materials used.
2. Material cost control:
Establish a unique number for all raw materials used in production, attach a barcode label, and establish strict picking control. Through the bill of materials of each type of product, the product production plan is decomposed into a material use plan, and the material balance can be calculated reasonably, and the deviation of the material consumption of each batch of products from the standard finished product can be controlled.
3. Operation time control:
By scanning the operator number and machine number, the working time of each operator is recorded. After statistical analysis, the deviation between the operating time of each batch of products and the standard operating time can be calculated.
4. Production statistics:
By scanning the body number of the finished product and the barcode of each main component, the output statistics and material consumption statistics of the finished product can be automatically completed, and the waste status can be calculated at the same time.
5. Piece counting statistics:
Many companies adopt the piece rate method. Piece rate statistics is a very cumbersome task. Through the bar code identification on each product and the production worksheet, it is easy to count the number of products completed by each worker, and to investigate the defectiveness. The responsible person for the product.
6. Production scheduling:
Manage online production tasks, orders, batches, work orders, etc., and modify the dispatch list according to the specific situation.
7. Product archives:
Using bar code to collect data, a complete product file including detailed information such as product manufacturing process, component configuration, and quality inspection data can be established.
8. Process data query:
Traditional inquiries on production site information are based on manual operations. It is better to input various production reports, receipts, and form data into the computer for summary, and then obtain various data. However, this approach cannot guarantee the real-time, accuracy and comprehensiveness of the information inquiry, and there are many man-made data errors. Barcode technology is used to store various basic information in the ERP system, and business data is collected from the production line in real time to ensure the real-time nature of the information. At the same time, because the data is input at one point and shared as a whole, the consistency of the information is guaranteed ; And because the information inquiries come from all the processes of blanking, processing, assembly, quality inspection, maintenance, packaging, and warehousing from the entire production site, the comprehensiveness and accuracy of the information are guaranteed. ERP combines e-commerce technology to develop a production site portal based on Web technology. Before the management wanted to know the production status, they had to go to the production site to find a bunch of people to ask, and the information they received was not necessarily accurate; or the customer wanted to know the production progress of his order at the manufacturer, then he had to call the left Call right. With the Web-based query interface and advanced OLAP technical support, everything is under control whether it is within the enterprise or around the world.
[ad_2]