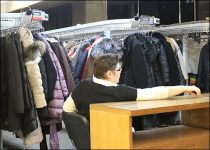
Fresh USA launches RFID delivery system to help manage dressing room clothing
[ad_1]
Recently, several Russian companies are using an RFID transmission system to allow people in locker rooms or clothing storage and areas to get clothing more quickly. When a person stores a coat or other clothing, he will receive a badge or bracelet with a built-in RFID tag whose ID number is bound to the item’s location information. Fresh, the company that provides this technology, has established a US subsidiary to provide this solution in North America. The system includes a delivery system for storing or retrieving garments, RFID readers, tags, and software for identifying garments.
Currently, a Tigre de Cristal casino and resort and Izmailovo concert hall in Russia are using this technology to manage company clothing.
(Izmailovo concert hall uses Fresh’s RFID conveyor belt to manage audience coats)
Tigre de Cristal also uses Fresh’s RFID solution to manage its coat inspection service and uniforms. The casino and resort officially opened in mid-2015, and the system was also put into use at the same time. Tigre de Cristal deployed a conveyor system to manage 6,000 coats of customers, and another to manage uniforms for 1,000 employees.
Leri Tomin, CEO of Fresh USA, said that customers can put their coats in the cloakroom. Then you will receive a plastic card with a built-in NXP high-frequency 13.56MHz Mifare DESFire EV1 4K RFID chip. The staff placed the card near a reader (manufactured by a third-party supplier in China) to read it, which was built into the control box of the conveyor. After the reader reads the card’s unique ID number, it transmits this information to the software to bind the tag ID number with the placement position of the employee’s coat. When retrieving the coat, the customer only needs to return the plastic card to the employee for reading, and the conveyor belt will automatically send the coat to the employee.
The system for management and uniform cleaning is also fully automated. All uniforms (such as shirts and pants) have a washable UHF RFID tag (Fujitsu WT-A521) built in. In Fresh software, the tag’s unique ID number and the owner’s employee information are bound to each other.When employees leave work, they will take their uniforms for cleaning, and they only need to get the RFID badgesRFIDRead before the reader to unlock the conveyor compartment.
After the reader reads the RFID tag (compatible with ISO 15693 standard) in the card, the system will pass the ID number to the software to confirm the employee’s information and then open the compartment door. After the employee puts the clothing in the compartment and closes the door, the software binds the compartment number to the employee ID.
A UHF RFID reader is installed on the conveyor belt to read the ID number of each garment tag. In this way, the software can update the status of these items to be cleaned.
After washing, drying, and folding, these garments will be put back on the conveyor belt, and the reader will read the tag ID again. The reader will then instruct the controller to put the garment back into the compartment where it is bound. In this way, employees can retrieve their garments in the same compartment.
When retrieving the uniform, the employee needs to read the ID badge on the reader again. After the check, the compartment door opens automatically and the employees can retrieve the clothes.
Mikhail Tureyskiy, Tigre de Cristal’s venue management manager, said the system was installed as soon as the casino opened. He explained: “We want to have all the new technologies. The speed of customer service is very important.”
The Izmailovo concert hall is also using this technology, which they installed early last year to manage the coats of attendees. This technology replaces the past methods of storing and obtaining artificial coats. Igor Mikhailovich said: “Previously, we used ordinary wardrobes and hangers to store overcoats. After the concert, the audience lined up to lead the clothes.”
The software not only helps Izmailovo employees quickly identify clothing and uniforms, but also creates a record of how often the cloakroom is used.
According to Tomin, the system has tripled its efficiency. Currently, the company’s US branch is negotiating with several potential customers. The company can customize the program for each customer, and the compatibility of RFID hardware is also very high.
(Exclusive manuscript of rfid world network, please indicate the source author for reprinting!)
[ad_2]