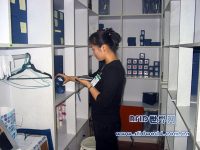
Intermec helps Swarovski shine in China
[ad_1]
The crystal-like Chinese market
Statistics show that as of 2008, the average annual growth rate of China’s high-end consumer goods market reached 20%. By 2015, sales of high-end consumer goods will exceed 11.5 billion U.S. dollars, accounting for 29% of total global consumption. As of the end of January 2009, China’s luxury goods consumption totaled US$8.6 billion, accounting for 25% of the global market. This is the first time that China has surpassed the United States and ranked second in the world.
The world-famous Swarovski is one of many high-end consumer goods brands that value the development of the Chinese market. In 2007, the Swarovski Group had revenues of 2.56 billion Euros, making it the world’s largest manufacturer and seller of artificial crystals. The company entered the Chinese market in 1971 and has now developed for nearly 40 years. Swarovski crystals are pure in quality, unique in cutting technology, and lead the international design trend. Therefore, they are deeply loved by Chinese fashion and high-grade people.
Warehouse management needs to cope with the rapid growth of business
Swarovski has more than 100 stores in China, directly facing consumers all over China, providing exquisite Swarovski products. Swarovski has a shipping center in Shanghai, China, with a warehouse area of tens of thousands of square meters, and more than 10,000 items are shipped in and out every day. The sales and inventory of each branch need to be counted in time, and then reported to the delivery center on time according to the situation, and the warehouse management personnel will deliver the goods on time according to the order form of each branch.
Same as most traditional inventory management methods, Swarovski’s shipping center originally used a set of SIT system. Warehouse managers and maintenance personnel could only manually carry out warehousing and inspection by relying on computer information and traditional paper data. , Delivery, inventory, repair, return items and other operations. Therefore, there is an urgent need for improvement in efficiency and accuracy.
With the increasing shipment volume and sales demand, Swarovski needed a set of advanced and comprehensive solutions to meet the needs of inventory management, delivery, maintenance, and store management, thereby enhancing customer satisfaction.
Unparalleled fully automated management
After months of research and selection, the warehouse management and service solutions (SWMS) of American Intermec (hereinafter referred to as “Intermec”) and Shanghai Zhelin Software Technology Co., Ltd. (hereinafter referred to as “Zhelin Technology”) Selected by Swarovski. Zhelin Technology’s SWMS system and SAP work together to provide customers with a convenient and complete software platform. Intermec’s PD41 and PB42 printers and CN2B handheld terminals provide customers with support for data collection, information verification and store sales management. Therefore, its original semi-automated inventory management has become a fully automated method.
In the receiving process, the warehouse management staff needs to count and verify the goods sent from the headquarters. PD41 will print its information barcode for the required product. The CN2B handheld device collects and records product information and transfers it to the back-end database to prepare for the outbound operation. Intermec CN2B has high-end system configuration, compact structure design, and is light, strong and durable. The product has the Cisco CCX certification to provide customers with network compatibility, network security and other guarantees.
The characteristics of Swarovski crystal products pose challenges for the warehouse and inventory operations. Because crystal products are usually small in size, it is difficult to immediately distinguish the desired product from the product packaging alone. At the same time, it is time-consuming and labor-intensive to identify the product through the label. Then, the adoption of the barcode system easily solves this problem. Warehouse managers only need to find the corresponding shelf based on the database information, and then use Intermec’s CN2B handheld terminal to verify the identity of the product. After confirming that it is correct, the goods will be quickly packed out of the warehouse. The software system generates the packing list, which is printed by Intermec PD41. Intermec Easycoder PD41 barcode printer is a reliable multi-function printer. The design of all-metal chassis and shell is sturdy and durable.
The program also extends to Swarovski’s store management. Intermec PB42 printers are used to print sales receipts, and CN2B handheld terminals are used to store warehouse management.
In addition, after-sales maintenance, as an important indicator of Swarovski’s customer satisfaction, also greatly benefits from this program. This warehouse management and service solution makes it possible to trace the repair order. The system can generate a return report on the same day to provide reliable data for customers’ real-time query. At present, Swarovski has made a solemn promise to consumers to ensure that the repaired products will be returned within 5 working days.
Results are immediate
The program was formally implemented in September 2008, and the first phase of deployment was completed at the end of December. Currently, Swarovski uses more than 80 Intermec wireless terminals CN2B and nearly 20 PD41 and PB42 printers.
After several months of successful application, Swarovski’s delivery efficiency has been greatly improved, reaching 43%, shelf management accuracy has reached 100%, and maintenance time has been shortened by 32%. Greatly improved the management level of the business in China and customer satisfaction.
Min Wang, General Manager of Intermec China, said: “When it comes to the application of automatic identification technology, people usually think of the deployment of industrial products such as automobiles or manufacturing. This time Swarovski adopted Intermec’s solution. The program shows that automatic identification technology can serve the high-end consumer goods and durable goods industries and create value. At the same time, automatic identification technology can provide support for enhancing the company’s operational efficiency in many aspects.”
Next, Swarovski will continue to expand the deployment of Intermec PB42 printers and CN2B handheld terminals for store management. In order to further improve customer satisfaction, Zhelin Technology will also develop and deploy a comprehensive business management system for Swarovski, and upgrade the customer service system to a unified national platform.
[ad_2]