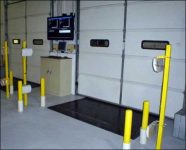
Nursery company uses RFID technology to improve work efficiency
[ad_1]
After four years of trial and error on the RFID system, the plant cultivation company in the Cayman Islands of Paris has passed the busiest season (spring) with the help of RFID technology. The RFID system can monitor the location of the metal trolley at any time, when it will be delivered, when it will be returned, and which retailer it will be sent to. In addition, through the information displayed on the display screen integrated into the RFID system, warehouse staff can load goods faster. According to the destination of the metal trolley, the system can guide which metal trolley should be loaded and in what order.
Color Point provides ornamental flower bed plants to stores in Kentucky, Indiana, Ohio, Tennessee and West Virginia. The greenhouse used for cultivating all plants covers an area of nearly 15 acres, and an average of 25 trucks of plants are transported out of the two trolley stops every day. Brad Slattery, IT manager of Color Point, said that after adopting the RFID system, the company has become one of the fastest loading companies in the nursery industry.
The picture shows Color Point’s car stop using RFID technology
The 6000 metal carts used by the company to ship plants generally have display shelves. They are directly transported to Lowe’s or other stores, and then transported to the storefront, where the plants are displayed and sold. Once the plants in the metal trolley are sold out, the Color Point truck loads them back to the nursery in Paris for reuse. Manually recording and tracking the shipment or shipment of these metal trolleys is an inefficient way for Color Point.
In some cases, for example, if the metal trolleys are finally left in the store, are loaded with other goods, or are lost, it is difficult for the staff to know when and where these metal trolleys worth $400 to $500 each were delivered, and Whether to return to the nursery. More importantly, Color Point’s drivers will regularly load the metal trolleys at the retailer, but it is difficult for them to know how many metal trolleys are ready to be loaded, so they have made a plan to load the metal trolleys at the appropriate time. It is even more difficult (when the truck can load empty metal trolleys, there have been too many metal trolleys waiting for shipment before).
Slattery said that in order to solve this problem, Color Point tried to track the metal car through the bar code, but found that scanning the bar code label was time-consuming and problematic. So about 4 years ago, the company began experimenting with systems provided by several RFID vendors with 13.56 Hz high-frequency (HF) passive tags. The company installed interrogators at both loading points, buried antennas, and placed tags on the bottom of metal carts. However, the tag cannot reliably read the data, so Color Point took the antenna out of the cement and moved it to another place at the loading point, he said. Despite the company’s many efforts, the tag still cannot obtain a suitable reading range. Slattery said: “If there is no infrastructure that can give a 100% read rate, then nothing will work.”
At the beginning of 2008, Slattery said that he started discussions with SATO, and SATO provided the system with a 100% read rate. SATO replaced the high frequency reader with Alien Technology’s UHF interrogator, and installed two readers (corresponding to two parking spots) and installed antennas on the ground. According to SATO’s national sales manager John Anderson, the company placed Avery Dennison’s D-222 EPC Gen 2 tag on the bottom of the metal car and provided iTrack software, which can be installed in Color Point’s back-end system. Make the nursery company arrange the loading plan for each trolley, and track the transportation of each metal trolley at the same time.
The final system can enable Color Point to load trucks faster and more efficiently by knowing where and how many carts are needed and where the carts need to be shipped. When a trolley is transported to the truck, data about the transport and the trolley number are entered into the system, and this information can be stored in a computer in the warehouse. The monitor connected to that computer will display a chart of the truck, with squares representing the carts. Through the ID number of the trolley and its description, the system shows which trolleys need to be loaded onto the truck and the order of shipment. Based on the design of the system, trucks will have several representative parking points in their transportation routes, so the cars can be loaded onto the truck according to the order in which they are unloaded from the truck at each parking point, without reloading.
Each car is equipped with two tags with the same ID code number
Color Point uses SATO’s GL408e thermal printer and RFID encoder to write a unique ID number in the RFID tag, and then installs two tags with the same ID number on each metal trolley (one is on the upper part of the right front wheel, The other is on the upper part of the left front wheel). When the metal car passes through any stop, the RFID interrogator there will obtain its ID number and transmit the information to the iTrack system via the connected cable. The tag’s unique identifier is connected to the shipping number in the system, so Color Point’s managers can know when the metal trolley was shipped, which store it was shipped to, and which truck it was shipped by. Warehouse workers can see through the screen what plants these metal trolleys contain, the next trolley that needs to be shipped, and whether they have shipped the trolley by mistake.
When an empty metal trolley returns to the nursery of Color Point, the interrogator will obtain its tag ID number to record the return information of the metal trolley in the corresponding retail customer’s account.
Through the system. The company’s managers can track the length of time the metal trolley stays in a particular retail store, so as to know how many empty metal trolleys will be available at a certain time, thus reducing the number of times the truck drives to pick up the empty metal trolley.
[ad_2]