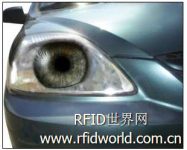
RFID helps realize self-service state monitoring of assets and improve maintenance efficiency
[ad_1]
How often should an asset be overhauled? Where are the spare parts that need to be repaired? Who is the best technician for this job? The answers to these questions can reduce asset maintenance costs and improve work efficiency. At the Auto-ID laboratory in Cambridge, UK, researchers have developed RFID tools and solutions to automate the asset repair process and improve the availability of information used to determine repairs.
In order to achieve effective maintenance, it is very important to understand the existing configuration of the asset and its configuration changes during the life cycle. The current method of manually upgrading asset records makes the maintenance management system inefficient. RFID technology can automate these processes and ensure more accurate data.
Take automobile maintenance as an example. As part of the EU-sponsored PROMISE project, the laboratory has developed a set of RFID solutions that can automatically establish a vehicle configuration: paste passive UHF RFID tags for metal on important parts of the car, As a unique identification code for the part. A “service mat”, including an RFID reader and four antennas, can capture the ID code of a single component. The service mat can detect the replacement of any part. Touch the system to upgrade the vehicle configuration database. The ID code can correspond to the online data-EPCIS database and Discovery Services, providing maintenance personnel with a complete service history of the vehicle.
In the future, assets will realize intelligent self-service maintenance monitoring
Researchers have also developed a set of RFID solutions that align spare parts management with maintenance plans. Take a washing machine as an example to show the workflow: a condition monitoring platform helps to assess the status of laundry equipment, using some embedded wireless sensors to monitor important parameters in real time, such as vibration, temperature, humidity, current and tilt. Data from the condition monitoring platform and the supply chain platform, along with other information such as personnel availability and operation plans are imported into the Decision Support System (DSS). DSS uses this information to determine the best time for repairs.
Researchers are also developing a “self-service asset” project that uses active RFID to automate and optimize service operations for civil aviation. The system not only monitors physical assets, but also selects the best component suppliers.
In the future, companies can use smart assets that can monitor their conditions on their own, that is, the assets themselves can determine the repair time.
[ad_2]