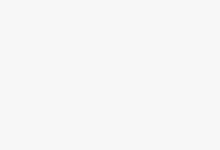
A company car uses QR code application management solutions in the production process
[ad_1]
Company A Automobile Co., Ltd. is the first car production base of Company A Automobile Company in China. Here, A company automobile company will not hesitate to invest in TOYOTA’s latest technology to produce a new type of car specially developed for China, with full consideration of environmental protection, safety and other factors.
The use of two-dimensional code application management solutions enabled company A’s cars to successfully apply QR two-dimensional bar code data collection technology in the production process control and management system, and completed the establishment of the production process control and management system.
1. Data collection and management of company A’s automobile assembly line
Automobiles are produced on a small-batch, multi-variety mixed production line. The cards with product types and production instructions are placed on the product production table. These commands are read by various operators and complete assembly tasks. There are serious problems in using these cards. Problems and big hidden dangers: Including a series of problems such as speed, error rate, data statistics, coordination management, and quality problem management.
System summary
If two-dimensional codes are used to replace manual cards, the initial investment cost is not high, but a high-reliability system is established.
1) At the front end of the production line, according to the production instruction information sent by the main control computer, the barcode printer prints a barcode label and sticks it on the product carrier.
2) In each operation process, the operator uses a barcode reader to read the barcode symbol on the carrier, enter the information of the operation into the computer, and the main system issues instructions to the operator and the inspection device.
3) In each process, the barcode label attached to the mounting part is read by the scanner, and then the 2D barcode attached to the carrier is read to confirm whether the part is installed correctly.
4) In each process, the production instruction number of the two-dimensional bar code, the production line sequence number, the body number data, the data of the mounted parts, and the inspection data are all fed back to the main control computer to manage the progress.
  
Application effect
1) Lower investment.
2) The two-dimensional barcode can be stably read by the reader (low error rate).
3) A lot of manpower and time can be omitted.
4) The command of the main system to the production process is comprehensively improved.
5) The whole production process is connected with the main system, and the production efficiency is greatly improved.
2. Application of company A’s automotive supply chain acquisition system
Application Environment
Auto parts suppliers produce spare parts according to auto manufacturers’ orders and supply them for a long time. This can reduce manual operations, reduce costs, and improve efficiency.
Application description
1) The car manufacturer sticks the kanban label on its turnover box, and first defines the box number.
2) The car manufacturer reads the one-dimensional bar code on the kanban label, makes the ordered part number, quantity, box number and other information into a QR code, and produces a kanban receipt with the QR code.
3) Deliver the kanban bills and kanban labels to the parts manufacturer.
4) The parts manufacturer reads the QR code on the kanban receipt provided by the vehicle, processes the accepted order information, and prepares a delivery instruction.
5) The parts manufacturer attaches the kanban label to the shipped product, and the kanban receipt is sent to the automobile manufacturer as a delivery note.
6) The automobile production plant reads the QR code on the kanban receipt for receiving statistics.
Application effect
1) The use of QRCode enables automatic comparison of “product name”, “specification”, “batch number”, and “quantity” that could not be barcoded. The visual observation operation when leaving the warehouse is greatly reduced, which reduces the errors of the operator for human identification and inspection, and avoids Occurrence of misdelivery.
2) The outbound order system prints two-dimensional barcodes that are encrypted, safe and not easy to make mistakes.
3) The inspection and delivery work can be completely separated from the main system and the network environment to operate independently, with little dependence on the main system, reducing the pressure on the main system’s network communication and system resources, and at the same time reducing the safety requirements.
4) Really achieved, the two-dimensional bar code data and the outbound order data and the attribute characteristics of the actual outbound items are unified.
5) Speed ​​up the time of outbound inspection and acceptance operations, shorten the work process, and greatly increase the amount of information for acceptance, thereby improving efficiency, reducing costs, ensuring safety, and preventing errors.
[ad_2]