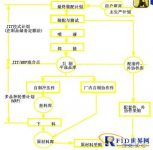
Application case of Langfeng barcode in FAW car production process management
[ad_1]
In order to pursue higher quality and customer satisfaction, and at the same time respond to the requirements of the automobile recall system, FAW Car Co., Ltd. plans to first introduce a production site management and control system in the assembly workshop of the new factory to improve the efficiency of the production process and the level of quality control, and assist Quality improvement and quality improvement, and quality traceability management, thereby greatly enhancing the competitiveness of enterprises.
Project Background
FAW Car Co., Ltd. is a holding subsidiary of China FAW Group. It is the first joint-stock company in China’s car manufacturing industry. It was formed by the reorganization of high-quality assets of FAW Group Corporation, which is mainly engaged in the production of Hongqi cars and their accessories.
In the past few years, the successive launch of various Hongqi cars and variants and the timely introduction of the world-class new product M6 signify that the company has achieved substantial results in adjusting product structure, expanding product series and independent development. In July 2004, the new factory was put into use.
In order to pursue higher quality and customer satisfaction, and at the same time respond to the requirements of the automobile recall system, FAW Car Co., Ltd. plans to first introduce a production site management and control system in the assembly workshop of the new factory to improve the efficiency of the production process and the level of quality control, and assist Quality improvement and quality improvement, and quality traceability management, thereby greatly enhancing the competitiveness of enterprises. In May 2004, FAW Car Co., Ltd. began to implement the production site management and control system of Guangzhou Jinzhao Technology Co., Ltd. to record, monitor and analyze production, quality, materials, equipment and other information. The system has now become a powerful tool for FAW Car’s production and quality management.
Facing problem
The final assembly shop is the final production link of the entire automobile, and is the top priority to ensure the quality of the automobile and the production schedule. The final assembly shop includes sub-assembly assembly, main assembly, inspection and test runs and other technological processes, with a total of more than 100 processes, and it also needs to meet the mixed-flow mode of simultaneous production of multiple models. To this end, advanced automation equipment is used in key processes, and vehicle model management is carried out through bar codes. Nevertheless, production and quality management personnel are still troubled by the collection, monitoring and analysis of production and quality information. After in-depth understanding, the main problems were found to be:
* When customer complaints occur, how to find out the quality, equipment, personnel, time, test results, safety/critical part numbers and other information of the car in various production links based on the VIN code in a timely and accurate manner?
* How to trace the batch according to the VIN code of the defective car to determine the scope of the recall?
* How to collect on-site information in time? Some data is scattered in different devices, can it be centralized?
* Which defects often occur? Which parts have the most defects? Which operators/equipment are most prone to quality problems?
* How to count the defect rate in real time and alert the abnormality in time?
* How to provide a basis for quality improvement through in-depth analysis?
* Is there a way to free us from the time-consuming work of summarizing reports?
Longwind barcode solution
FAW Car conducted an in-depth inspection and demonstration of the project, and finally decided to cooperate with Guangzhou Jinzhao Technology Co., Ltd. to build a production process quality control system covering the entire assembly shop.
The system uses a ring optical fiber network as the backbone to form a redundant backup to ensure the reliability of network operation.
The system uses a three-tier architecture. The database adopts dual-system hot backup. The application server is used for system logic business processing.
The bottom layer of the system is a workstation directly facing the production site, which is used for vehicle VIN code collection, defect collection, key component correlation, repair processing and final defect verification. The data of automation equipment such as screwing machines, filling machines, and testing line equipment are collected in real time by the equipment data collection server through industrial Ethernet. The system is equipped with bar code guns in all workstations, which can quickly enter information such as VIN codes, defects, and component codes.
The system takes the automobile VIN code as the main line, and forms a complete archive of quality, equipment, production and key components through on-site data collection.
The system monitors defects, equipment parameters and test results in real time, and informs relevant personnel in time if any abnormalities are found.
Quality management personnel use the system to perform defect analysis, SPC analysis, and quality problem tracing. Equipment management personnel can centrally analyze the operation and capability of equipment, and production management personnel can compare and analyze defect self-detection rates, teams, and operators. To better improve production.
With the help of a flexible and easy-to-use secondary development platform, the system can easily find out the quality, production, equipment, parts and other information of a single car in each production link, restore the production site, and realize quality problem analysis and traceability. It can also track the batches of parts and complete vehicles, and can be traced back to level, thereby meeting the requirements of vehicle recalls.
The system provides a variety of commonly used routine reports, and can adjust or add new data collection interfaces and report formats through the secondary development platform.
All management departments interact with the system through a firewall through the network, realizing the timely, accurate, safe and sharing of information, and at the same time ensuring that the equipment connected to the system is protected from virus attacks.
Project benefits
* The workshop management is transparent, breaking the “black box operation”, and the information and status of quality, production, equipment, and components are clear at a glance, which improves the management level.
* The response speed is greatly improved, and the problems at the production site can be found in time and dealt with in time.
* Quality improvement, real-time quality information collection and monitoring, changing post-event analysis to pre-prevention, effectively reducing the defect rate.
* Realize analysis and traceability in the true sense, laying a solid foundation for automobile recalls.
* Centralized storage of information and resource sharing improve the timeliness and accuracy of data. The system automatically generates various routine quality, equipment and other reports.
long term planning
In view of the good application effect of the system, the next step will be to increase on-site data collection points, and gradually expand to painting, car body, stamping workshops
[ad_2]