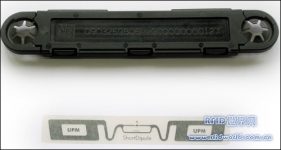
Auto parts supplier ZF Friedrichshafe launches RFID production line
[ad_1]
The well-known automotive component supplier ZF Friedrichshafe introduced a set of RFID systems to track and guide the production of eight-speed transmissions in its Saarbrücken factory in Germany, thereby expanding the company’s RFID application scale.
ZF uses UPM Raflatac RFID inlay, enclosed in a plastic protective shell
In the past three years, ZF Friedrichshafe has been using RFID technology to track cargo and assembly line engine maintenance records, and has gained experience in RFID applications.
For this new RFID application project, ZF specially designed a new production process. The company used bar codes to identify products before, but the bar codes are easily damaged or fall off during production. The company needs a new solution that can identify each transmission. After testing the RFID tags and confirming that they can withstand the harsh production environment of ZF, the company introduced RFID technology directly into the production process and established an eight-speed transmission production line, including about 15 RFID tag reading points, and tag storage to control production. Process information.
When ZF or its supplier casts the transmission case, the case houses a UPM Raflatac ShortDipole passive UHF RFID inlay, encapsulated in a protective plastic case. The inlay conforms to the EPC Gen 2 standard, has 512 bytes of user memory, and contains production-related data, according to Gerhard Schaller, the company’s information technology and factory automation manager. Such information includes item numbers, serial codes, transmission production dates, and production machine models.
Labels are installed on the transmission housing
Once the tag is applied to the transmission, ZF or its suppliers use an RFID reader-hand-held or fixed-to test the tag and store the casting information in the tag. The supplier then sends the transmission case to ZF, and ZF uses a reader to read the tag to identify the transmission case before sending it to the production line.
On the production line, ZF has identified the housing about 15 times in three production stages: mechanical processing, transmission assembly and inspection. According to Jürgen Kusper, business solutions manager of B&M Tricon Auto-ID Solutions in Australia, B&M Tricon Auto-ID Solutions is responsible for the project Planning and integration.
At multiple points in the fully automated production line, ZF uses remote readers or read-write stations to read tags and obtain information that can change the production process of specific transmissions. For example, process parameters and measured values may be used for customized production. At the reading and writing station, the system upgrades the label data, such as supplementing production status information.
Readers read tags at multiple reading points on the production line
“RFID controls the entire production process,” Kusper said.
In the final stage of production, each transmission is filled with oil, and running tests are carried out to ensure its normal operation. Once the transmission passes the test, the system then writes the serial number to the RFID tag, and the tag still retains some production information for diagnosis and process monitoring purposes. Other production data is kept on the ZF server and can be used for production traceability if there is a problem with the product.
The system was implemented in early 2009, and ZF hopes that the RFID-controlled production line can produce 100,000-200,000 transmissions per year.
Kusper said that the main benefits of this system are stability, low cost, unique identification of the transmission, and production control capabilities.
This system uses the You-R OPEN middleware produced by RF-IT Solutions. ZF has adopted software in other applications to achieve central management. The system uses Siemens RF 660 reader and Psion Teklogix Workabout Pro handheld reader.
[ad_2]