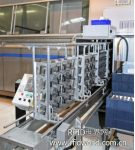
Bosch, the world’s largest auto parts manufacturer, quickly returns on RFID investment
[ad_1]
Bosch, the world’s largest auto parts manufacturer, uses RFID-labeled kanban cards in its two diesel injector manufacturers in Bamberg and Homburg, Germany, to replenish the parts needed for production in a timely manner. Among them, the kanban cards at the Bamberg manufacturing plant use passive high frequency. RFID tags, while Homburg uses passive UHF RFID tags.
Several diesel injector production lines in Bosch’s two factories are mainly controlled by computers. Workers supervise the operation of the machines and add necessary components such as screws and springs from time to time. Before the implementation of the RFID system, the replenishment of components often took two hours to complete the order. The components are stored in a container box. When a container is full of components, the worker places a kanban card (printed with a bar code of the component type and a number that can be recognized by the naked eye) on the box. When the components in the container box are used up, the worker removes the kanban card and sends it to a workstation. There, workers manually scan the barcode and place an order for replenishment, but since a single card is easily overlooked, this process is prone to errors.
In order to speed up the replenishment process of components, Bosch decided to introduce RFID tags to kanban cards and test two different types of RFID technology. Bosch chose to test Brooks Automation’s high-frequency technology at the Bamberg plant. In the Homburg plant, considering the possibility of reading labeled kanban cards in batches or remotely, the company adopted an ultra-high frequency RFID system.
Martin Doble, chief technology officer of RFID software company noFilis, stated that Bosch and software vendor SAP started conceiving the project in early 2008 and selected the hardware in April of the same year. Pilot tests were carried out in Homburg in May and Bamberg in July. Pilot test. SAP Deutschland is the software integrator for this project, and noFilis is the equipment integrator and provides local hardware installation services for the project. Bosch hired these companies one by one, and none of them was the total integrator of the project.
Production line of diesel fuel injector
Brooks Automation provided the Bamberg factory with 13.56 MHZ high-frequency readers and tags that comply with the ISO 15693 standard. Each high-frequency tag is encoded with a non-EPC Gen 2 ID code, but it follows the same format and is generated by the SAP system that supports RFID applications. The operating frequency of the UHF tag is 868 MHZ, which complies with the EPC Gen 2 standard. When these tags are compiled, they correspond to specific types of components in the database. Kanban cards of the same component can be reused.
In Homburg, Bosch uses Feig Electronic’s UHF readers and UPM Raflatac tags that can be read in the near or far field. The RFID application process in the two places is basically the same. Bosch used a total of 2,000-3,000 labels, laminated on the printed kanban cards generated by the SAP system.
The company uses SAP’s Auto-ID Infrastructure (AII) software module to integrate data collected by RFID and noFilis CrossTalk Control Center software, which is responsible for managing the RFID reader of this application. At present, Bosch uses a total of 80 readers; when Bamberg and Homburg complete the plant-wide implementation, the company expects to use 200 readers.
According to Dobler, both UHF and HF systems are operating normally without any problems. Due to the impact of the world financial crisis, global auto suppliers are facing tremendous pressure to reduce costs. Although Bosch has slowed down the project, it will still advance the implementation of the project.
Although both factories have adopted RFID systems, this has not changed the production process. After the employees poured all the components in the box into the production machine, they took away the RFID Kanban card and placed the card in a specially designed mailbox-similar to a box with an embedded RFID reader and antenna. This is the first reading point of the card. When the employee puts the card into the box, a green light turns on, indicating that the RFID tag was successfully read. The system then places an order to order the required components. CrossTalk software manages the communication between the reader and the local server running SAP software.
Within a working day, another employee collects all the cards in the mailbox according to a certain period of time, and then takes the cards to the component receiving area. In another location, employees visually compare the numbers of the kanban card and the component box or read the barcodes of both to match the kanban card with the new component box.
The advantage of the high-frequency system is that the high-frequency reader is cheaper than the UHF, although the high-frequency tag is more expensive; the advantage of the UHF system is that the card can be read in batches, and the reading distance can reach 16 feet. The reading distance is only a few inches.
Now, Bosch saves two hours of replenishment time each day, which will quickly bring the company a return on investment. Based on this prospect, the company plans to also promote this application in 8 other factories around the world. Considering the cost and reading distance factors, Bosch will be more likely to choose a high-frequency RFID system.
[ad_2]