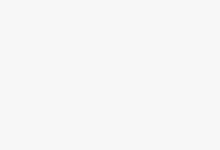
Dongfang Hope Baotou Rare Earth Aluminum Co., Ltd. self-provided power plant RFID coal delivery project
[ad_1]
l Introduction
Dongfang hopes that Baotou Rare Earth Aluminum Co., Ltd.’s self-provided power plant will take the lead in the industry to use RIFD technology to manage the metering of coal entering the plant after comprehensively considering the economic benefits of the enterprise and the implementation cost, and upgrade and transform the company’s original process. Achieved the goal of unmanned.
l Original process
The factory’s coal loading management before the RFID system upgrade is based on the “coal loading notice”, and the specific process is as follows:
1. Generate a notice. The purchaser generates a “coal loading notice” in the original information system according to the purchase contract every day. The generated notice contains the date of coal delivery, coal type, manufacturer number (the name of the manufacturer is kept secret from other internal links), and the documents Serial number and other information. After the purchaser generates the notice, it is sent to the coal merchant. Coal dealers dispatch vehicles according to the notice, which is generally one vehicle per order, and the receipt is valid on the same day.
2. Sampling coal dealers hand over the vehicle bill to the coal truck and send coal into the factory. The coal must be sampled first. The sampling process is that the driver of the coal truck will tell the sampler the number of the vehicle sent, and the sampler will use the paper report obtained in advance. Switch the sampling machine to the corresponding sampling tank. Sampling is done afterwards.
3. After over-sampling, the heavy-duty process of the coal car to the weighing room. The specific process is that the driver will show the notice to the weighing staff, and the weighing staff will enter the order number in the existing system, and the vehicle number and model Entering, and then weighing. The weight data is real-time collection of the original system with instruments.
4. Receipt. After the coal truck is weighed, go to the coal yard to unload the coal. At the same time, the coal management personnel signs on the coal loading notice to prove that the coal truck has entered the yard. If necessary, deduct the weight, that is, write the sensory judgment of the coal quality on the notice, that is, the deducted weight.
5. Tare back/print scale sheet After unloading the coal truck, go to the light scale in the weighing room for backing. Tare is still based on the notice, and the weighing staff will record the tare weight and print out the weighing list.
l RFID metering system process
1. Card issuance After the sample purchaser sets the coal type, the manufacturer, and the coal delivery date in the system, the RFID card is issued in batches, that is, the card is initialized. The initialized card is used to replace the original notice and is sent to the coal merchant.
2. After the sampling driver gets the card, he will swipe the card for sampling. During sampling, the sampling personnel will input the vehicle number in cooperation with the monitoring system. During sampling, the system will automatically fetch the sampling tank number information from the card and send it to the upper computer of the sampling machine. , Realize the automatic can change of the sampling machine.
3. Overweight After sampling, the coal truck is weighed on the RFID unmanned truck scale. In the specific process, after the system senses that a vehicle has entered, it starts the scanning system and scans the card. After scanning the card, it waits for the scale data to stabilize and then writes the weight data.
4. Receipt The RFID system is equipped with RFID handhelds for coal yard personnel. When unloading, the coal yard personnel scan the card to obtain vehicle information, and operate the PDA to input the receipt/deduction information. The data will be written into the database in real time via the wireless LAN in the factory.
5. Leather backing After signing/unloading, the coal truck performs a backing operation on the unmanned truck scale.
6. Receiving card/printing the weighing list. After the tare is returned, the driver inserts the card at the unattended automatic card collection terminal. And the terminal system will automatically play out the pound singles.
l Comparison of old and new systems and implementation effects
System Major Items |
Minor item |
Legacy system |
RFIDUnmanned weighing system |
Staffing |
Procurement staff |
constant |
|
Sampler |
constant |
||
Site personnel |
constant |
||
Weighman |
Pound per person |
unmanned |
|
Weight certificate |
Credentials |
Coal notification |
RFIDCard |
Features |
1. Paper 2. Fragile material 3. Single use 4. Rainy weather seriously affects the actual effect |
1. Plastic package 2. Not easy to damage 3. Recyclable 4. Not affected by external factors |
|
Each link time |
Print notice/Card issuance |
The original system is a dot matrix printer when printing notices, and duplicate copies, so the new system is slightly improved |
|
sampling |
constant |
||
too heavy |
1Minute40second/vehicle |
30second/vehicle |
|
Sign for |
The new system is slightly improved |
||
Peel back |
40second/vehicle |
25second/vehicle |
|
Receiving card and printing scale |
The original system receipts are in duplicate, printed by Epson dot matrix printers, and the driver’s receipt sheet needs to be stamped.30second/vehicle |
10second/vehicle |
|
System throughput |
—- |
In the case of one heavy balance and one light balance, the reasonable throughput of one day is150-180Around the car.If it exceeds200Car, the weighing staff need to work overtime |
Under the condition of one heavy balance and one light balance, the reasonable throughput of one day can reach300Above the car. |
other |
Weight method |
The original system saved the real-time data of the weighing scale manually by the weighing personnel. |
Save the data when the scale is stable |
[ad_2]