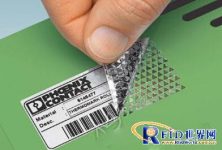
German Robert Bosch adds RFID tags to auto parts
[ad_1]
Boxes of automobile engine parts piled up into “high buildings.” The green light was shining, and a box of parts was “spit out” from the stairway, which arrived at the terminal along with the conveyor belt. The worker master put it on the luggage rack. There, it will be transported together with more parts to the “bus station” of the assembly plant, and then unloaded into the “supermarket”, waiting for assembly… The production line of the Humboldt factory of Robert Bosch Co., Ltd. (hereinafter referred to as “Bosch”) The special feature is that all parts have a unique radio frequency identification code, which can automatically “talk” with checkpoints along the way, thereby improving the overall production efficiency. As it is an effective application of “Industry 4.0” technology, this system won the logistics award from the German Automobile Industry Association this year.
Affix a smart ID card to each product to seamlessly connect parts produced in different regions
At the Humboldt Logistics Center, the reporter saw that every time workers took out a box of parts, they clamped the “kanban strip” that recorded product information into a rectangular plastic clip. The clip is pasted on the box, and there is a radio frequency identification code at the bottom of the clip-the ID of the box. After each production link, the card reader will automatically read out the relevant information and feed it back to the control center for corresponding processing. For example, if a freight truck drove it out of the logistics center, the assembly factory 5,000 meters away learned of the dynamics; before the assembly workers put it on the production line, the logistics center and suppliers knew that it was time to replenish the goods.
The production line visited by the reporter is mainly equipped with diesel engine injectors. The outer body and inner ejector rods of the injectors are provided by different suppliers. Each of the two parts samples is printed with a QR code, which is when the supplier left the factory. which provided. Andreas Muller, manager of Bosch’s “Industry 4.0” strategy, said that this is done to speed up visual management. To label a single product, a QR code is more convenient than a radio frequency code. But for every box of such parts, Bosch will give it a radio frequency identity.
As a radio communication technology, the principle of radio frequency identification is not complicated. Mueller said that the core of “Industry 4.0” is “Internet of Things.” There are several ways to attach smart labels to products: barcodes, QR codes, radio frequency codes, and sensors.Barcodes and QR codes must be scanned at close range and are easily corroded by water and chemicals.RFIDRadio frequency codes can be quickly read through various media. The RF code system introduced at the Humboldt factory costs hundreds of thousands of euros, but it is worth it. Before using the radio frequency code system, workers need to manually scan and input relevant information on the computer, which is not only cumbersome but also prone to errors. After the new system was put into use, the factory inventory was reduced by 30%, and the production efficiency was increased by 10%, resulting in savings of tens of millions of euros. The use of radio frequency codes also makes the control of the entire product process more transparent and real-time. At present, Bosch scans 2 million RF codes every month in ten factories around the world.
Mueller said that the biggest difficulty in applying radio frequency code systems is how to integrate new technologies into the original process for standardized production. A smart label is attached to each spare part. No matter where these spare parts are produced or what kind of “dialect” they originally used, they must speak “Mandarin” that each other can understand after entering the process.
In 2010, the German Federal Ministry of Economics and Technology took the lead in 20 parts supply, vehicle production and logistics related companies to carry out a demonstration project to popularize radio frequency codes in the automobile production chain. The project lasts for 3 years and the government and enterprises jointly invested 46 million euros. Among them, the Daimler Group installed radio frequency identification codes on the containers carrying automobile engines, and realized seamless docking in factories in different countries.
In the human-machine relationship, humans are problem solvers, and the boundaries between vocational training and academic education tend to be blurred
What do people do when production becomes more intelligent? The reporter noticed that Bosch’s injector assembly line has two lines running at the same time, one is a fully automated production line, and the other is “mixed and matched” by 15 workers and robots. The assembly speed is slightly higher than that of labor. Tim Dieudone, the person in charge of the production line, said that the factory had envisaged only automated production, but found that the error rate of the machine in many fine links was high. However, as production becomes more intelligent, the use of labor may be reduced. “After all, you have to pay workers but the machines are not used.” However, Mr. Ties Trapp, the director of the diesel system department of the Humboldt plant, held different opinions. He emphasized that the purpose of developing intelligent systems is not to reduce manpower, but to improve production efficiency and transfer manpower to more dexterous and complex processes. go with.
When talking about the relationship between humans and machines, Dietrich Zilke, a professor at the German Artificial Intelligence Research Center, told this reporter that humans can always find a place in intelligent production, because humans are the most flexible in the entire production system. Part. Zilke presided over the development of a set of intelligent demonstration production lines, which can automatically decide to fill blue, yellow or red soapy water without manual intervention based on the internal information of the products to be processed. In his eyes, the “Industry 4.0” production method is like this: the factory receives the products ordered by the customer on the Internet, without the need to modify the production line, it can immediately manufacture according to the customer’s individual requirements. In other words, the factory, like building blocks, can be easily dismantled and assembled into a new form.
Zilke pointed out that in the era of smart factories, the existence of workers is by no means to complete the remaining manual work of the machine: “They will become problem solvers, walking through the factory and observing whether everything is functioning normally.” He emphasized that this means The method of talent training also needs to be changed accordingly, and the rigid boundary between vocational training and academic education will be broken.
[ad_2]