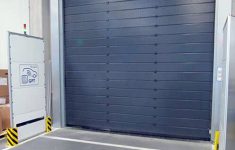
Radio Frequency Identification Tracking System in Volkswagen Transparent Prototype Project
[ad_1]
Opportunities and Challenges
The main challenge Volkswagen faces in the production process of prototype cars is how to achieve real-time and effective information about automation and supply chain. Now, the original parts of the vehicle and the installed prototype can be quickly and automatically detected, and then the data of the original part of the prototype that directly enters the relevant development process will be generated. Therefore, the right information needs to be delivered to the employees at the right time and at the right place, so as to ensure an efficient process for vehicle development.
Project Introduction
Volkswagen’s suppliers use radio frequency identification technology to confirm and mark the original parts of the prototype, so these parts can be identified by radio. The supplier transmits the logistics data and development data of related designated parts to Volkswagen through the business-to-business (B2B) platform. After processing, the associated data can be obtained once the corresponding part is identified. This result is an automatic query and tracking solution that allows companies to quickly and directly access relevant development information.
Radio frequency identification technology is considered to be a key technology to realize Industry 4.0, but it has not been widely used in the entire automotive industry so far. The transparent prototype project adopted by Volkswagen is the first demonstration of radio frequency identification technology in the automotive industry. Radio frequency identification technology makes the work process faster and makes the work more transparent. Compared with previous applications, the use of radio frequency identification technology is no longer confined to the company’s internals, it will also be the first cross-enterprise application.
The application of radio frequency identification technology requires the standardization of the entire industry. At present, the transparent prototype project has established corresponding standards with the help of the Automobile Industry Association and has been successfully put into practice gradually.
“When the supplier attaches standard electronic tags to the prototype parts, the parts can be efficiently identified in the automated production process,” said Hermann Dreyer, head of the general development of Volkswagen brand cars. In the development and testing phase, the production car is the main test object for continuous change and optimization of production. The production process is often dynamic, which makes it particularly difficult to record the production status of the vehicle.
Volkswagen launched the “Transparent Prototype” project in 2011, which shows how to accomplish this task in practice and development. In the transparent prototype project, Volkswagen must first master all necessary conditions, such as existing hardware and software standards, and get the help of the German Automobile Industry Association (VDA). After the establishment of appropriate infrastructure, the transparent prototype project can be gradually carried out.
During the implementation of the project, the supplier labeled the prototype parts in accordance with the quality management system audit 5509 standard (VDA5509) recommended by the industry and applicable to all companies. Therefore, prototype parts have a new “IP address”, and different labeling methods are involved, such as two-dimensional code (DataMatrix) guidelines and radio frequency identification. The use of radio frequency identification transponders has special significance. Hanno Wolff, the leader of the logistics department in the technology development department of the Volkswagen brand, said: “Even if the prototype parts have been installed in the car, the car manufacturer can automatically The prototype car parts with the RFID code are recognized, so many daily mass production tasks do not need to record the data of the manufacturing status during the car and part testing process.”
At present, Volkswagen now purchases prototype car parts marked with radio frequency identification technology from 250 parts suppliers of Volkswagen, Porsche and Audi. The exchange of production-related electronic data between the supplier and Volkswagen is very important for the effective work of this system. Volkswagen’s suppliers use the B2B platform supported by GroupIT to transmit the logistics data and development data of prototype car parts to automakers. The combination of radio frequency identification tags and additional electronic data exchange makes it possible to automatically enter parts such as prototypes in the receiving department. The part information provided by the supplier can also be entered in the subsequent departments and the testing process, thus realizing the “dialogue” between the test car and prototype car parts and the department engineer. This process can support process analysis and make it more efficient.
Company / Organization
The German Volkswagen Group was founded in 1937 and is the largest company in Germany. In 2010, it defeated Toyota Motor Corporation of Japan and General Motors Corporation of the United States to become the world’s largest automobile company. Volkswagen is a multinational automobile group with production plants in many countries around the world, ranking first among the top ten automobile companies in the world. The company is headquartered in Wolfsburg, Germany.
[ad_2]