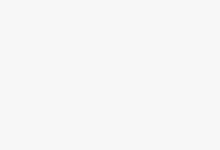
RFID automated management of A-Plant’s construction equipment rental trailer
[ad_1]
At the beginning of this year, Ashtead Plant Hire Co. (A-Plant), a British construction equipment leasing company, used a set of RFID solutions to automate the company’s new on-site tools to rent trailers. This 27-foot trailer is loaded with various drills, grinders, saws and other specific tools required by the workshop. The construction workers rent the tools they need, and the unused tools are still kept on the trailer. In order to better manage trailers, A-Plant hopes to implement a system that minimizes the number of visits by employees to construction sites, eliminates the need for manual monitoring of equipment loading, and provides customers with better and lower-cost services to ensure that they only pay The tools and equipment they actually use.
“We have been looking for a fully automated system in the past to allow users to rent the tools they need 24 hours a day, 7 days a week,” said Asif Latief, Marketing Director of A-Plant. “Our goal is to provide customers with high-quality services while reducing Environmental impact (the distance between the customer’s construction site and the store, and multiple trips to and from the store to rent tools)”. A-Plant has a total of 100 shops distributed throughout the UK, and the company has a total of 40,000 leased customers. If the company loads the equipment needed for guest rooms into trailers and directly transports them to the customer’s construction site, this can eliminate the need for customers to fetch equipment from the store multiple times.
The British company 4hSolutions specializes in providing tracking solutions for construction site equipment based on RFID technology, but the application solutions required by A-Plant are unique. “They are very clear about their needs and want to know how to use technology to achieve this,” said Andrew Davies, 4hSolutions sales director. The management of A-Plant not only needs to know the specific equipment removed from the trailer and the corresponding users, but also want to know which equipment needs to be repaired. This system is developed by 4hSolutions and includes a low-frequency RFID tag permanently attached to each toolbox (the toolbox usually only contains one tool and its related accessories), and an RFID reader that can be deducted and taken immediately.
Each construction worker is assigned a Paxton ID card with an LF 125 kHz RFID tag. When the worker took the equipment, he waved the card in front of a Paxton access control RFID reader at the entrance of the trailer. The system obtained the ID code and sent it to a PC in the trailer. The Assettagz software provided by 4hSolutions correlates the ID code with the information of the person carried, and the data is then forwarded to a server in charge of 4hSolutions to indicate to the system that the person has entered the trailer. This information is then sent to the A-Plant back-end system. At the same time, the scanning of the Paxton ID card by the first door also triggers the system to open the closed-circuit monitoring at that point. When the user enters the trailer, closes the door and locks it, he or she then scans the ID card with a second reader installed next to the entrance wall of the trailer storage area.
Rows of tool racks are placed in the trailer, connected to 100 power outlets, each of which contains a socket and an Elatec 125 kHz RFID reader. Each toolbox is also equipped with a socket. When the toolbox is inserted into the plastic socket of the shelf, the reader obtains its unique ID code and sends the information to the Assettagz software of the trailer computer. If the user takes the toolbox, the toolbox must be separated from the shelf socket first. In this way, the reader cannot detect the ID code, and the system upgrades the software, indicating that the toolbox has been taken away.The system then learns the user’s identity based on the employee’s ID code
By connecting various tool boxes with readers, Davies stated that the company has ensured that workers are responsible for the return and proper storage of tools, rather than simply placing them on shelves or on the side of trailers. Workers must read the tags again when they leave the trailer.
Return to the toolbox, the construction worker can insert it back to any reader in the trailer. The reader obtains the ID code of the toolbox tag and transfers it to the back-end system. The software upgrade toolbox status is returned. If the worker judges that the toolbox or an item in the toolbox needs repair, he can place the item on an isolated shelf where the tool cannot be reused. The shelf reader obtains the ID code of the toolbox label, and the system then upgrades and instructs the tools waiting to be repaired so that employees can make arrangements.
Each A-Plant maintenance worker carries a Psion Teklogix Workabout Pro handheld computer, including a 4hSolutions RFID reader, which is used to upgrade the data of the maintenance equipment. First, the maintenance worker reads the RFID tag of the toolbox. The handheld computer stores each ID code and the information of the corresponding toolbox, and then a series of drop-down menus pop up, prompting the staff to choose the maintenance process.
This system helps leasing customers to understand the tools used more clearly. In the past, leasing companies charged all the tools in the trailer, regardless of whether the tool was actually used. Now, the application of the new system allows the company to clearly understand which tools are taken out, when taken out and when used, so that customers can be charged accurately.
Moreover, if A-Plant finds that a tool is missing or damaged, it can use the system to determine the last user of the tool and charge a fee for using the tool.
[ad_2]