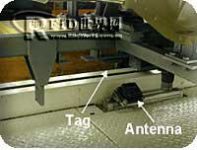
Successful application of RFID South Africa Toyota automated production line
[ad_1]
Toyota Burnaston South Africa is an automobile assembly plant with more than 3,000 workers and an annual output of 220’000 vehicles. This plant produces Toyota’s Corolla and Avensis series cars and sells them all over the world. Burnaston’s equipment department recently added EMS’s RFID equipment to its production line. Toyota is no stranger to RFID technology, and has used the old active RFID equipment produced by AB in its coating production line for more than 10 years. However, the obsolete equipment can no longer adapt to the new production process, and it has exceeded AB’s technical maintenance capabilities. Therefore, it is necessary to find a new system to replace the existing equipment and realize new functions.
For the past 11 years, Toyota has used AB’s RFID tags and readers in its production lines (AB has stopped production of its RFID products). The tag capacity is only 40 bytes, and the maximum storage temperature is only 140° F. The maximum temperature of the newly built paint shop will reach 200° C. And more importantly, the active tag of AB Company has a writable life of 5000 times, and the life of the old active tag is almost reaching its limit. AB has decided to stop the production and technical support of its RFID system from 2003. So Toyota hopes to replace this RFID system with cheaper and more technologically advanced products.
With the above thoughts in mind, Toyota is looking for another RFID system in the market to replace and upgrade its own ID identification system. And it is best to provide a wide range of interfaces to connect to Toyota’s original PLC system. After Toyota plans to upgrade, the system will use an independent PLC system to control the transmission process. In this system, the old AB PLC 5/25 and the new PLC 5/40 will work together. There are also interface issues that need to be considered. Among them, the interfaces provided on PLC5/25 do not have serial interfaces, and PLC 5/40 does have serial ports.
When choosing a suitable RFID product, maintenance and protection also need to be considered. The environment where Tag is used includes painting workshops and assembly workshops. There are a lot of dust, grease and various corrosive wastes in the environment. Therefore, corrosion resistance, durability and high temperature resistance have become areas that field engineers have to consider. In these places, RFID tags such as tags (some say only the size of a coin) cannot be used for a long time.
In the expected design, the RFID Tag of the paint shop must be baked at 200°C for at least 20 minutes in the paint shop. The original tags of AB can only work normally at 60°C at room temperature.
Finally, Toyota requires that the RFID system must be seamlessly integrated into the production process. Moreover, the two new models (Corolla and Avensis) produced in the workshop are on hot sale, and the production line cannot be stopped. As a result, the modification process can only be modified step by step by means of step-by-step replacement. If the method of completely renovating the stop line is adopted, it will cause very serious economic losses, and it may also affect production due to the discontinuity of data caused by the stop line.
South African system integrator Datascan helped Toyota develop a reasonable system transformation plan. At the beginning, Toyota took a fancy to Baumer’s active high-frequency tag. However, there are problems with the connection between Baumer’s products and the entire system. Baumer’s hardware interface requires a DH+ PLC and another new AB PLC 5/40. These conditions limit the application of Baumer’s products.
EMS company has been cooperating with Toyota for many years. Toyota companies in France and South Africa have used EMS company’s RFID equipment in their automobile engine/parts production lines and paint shops. The system of the EMS company with a history of cooperation for many years can provide an interface directly connected to the two PLCs mentioned above, and the quotation of the EMS company’s solution is only 60% of Baumer’s, so the RFID system of the EMS company has become Toyota The company’s inevitable choice.
In order to seamlessly replace AB’s RFID system with EMS products, the project team (including Datascan, Toyota, and EMS) decided to replace all antennas and tags with a step-by-step replacement method. The specific measures are first of all, using AB and EMS company RFID equipment at each site. Write the same information on the original AB company’s active tag on the EMS company’s Tag. The independent operation of the two systems can ensure the correctness of the Tag information and also allow independent communication of a single site. It also ensures the accuracy and security of the data. If necessary, it can be switched to another system without affecting production without any changes.
For this project, Toyota chose the LRP250HT high temperature resistant tag from EMS. LRP250HT Tag storage space is 48 bytes, and the number of reads and writes is 100,000 times. The maximum temperature that this tag can withstand is 200° C, which just meets this requirement.
Another factor that needs to be considered is the installation of the tag on the transport cart. The cart is made of metal, and metal will affect the read and write performance of RFID products. Finally, we used ceramic gaskets produced by EMS company and GM company technology and self-processed metal brackets to keep Tag away from the metal on the trolley, which satisfactorily solved this problem.
For the reader, the LRP820-04 reader controller is used this time. The reader uses an antenna specially designed for transmission belts and metal environments. The read-write distance of 152mm fully meets the needs of this time.
The installation of antennas is also something to consider. The space under the transport cart is too small to be used for antenna installation. Moreover, if the installation is unreasonable and heavy vehicles pass by, the antenna or Tag mounting bracket may be damaged. After several hours of research, it was decided to install the antenna at a height of 2 to 3 inches from the metal plate surface and install it at a certain angle to reduce the impact of metal objects on RFID.
Toyota used a total of 39 LRP820-04 read-write controllers and more than 20 CM52 network interface modules. The CM52 network interface module is used to connect the EMS read-write controller and AB’s PLC 5/25 and 5/40.
Finally, Toyota also purchased the handheld reader LPR7400 provided by EMS to maintain the production line. Workers can use LRP7400 to write data to the tag installed on the transport cart to record the product model/color/assembly information and so on. And if there is a write error or missed write during the production process, you can write manually to ensure the continuity of production.
EMS Radio Frequency Technology China Service Center |
Phone: 010-88430403 Fax: 010-88447190 |
[ad_2]