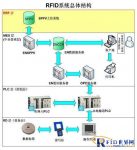
The successful application of RFID technology in the automobile manufacturing industry
[ad_1]
Preface
In recent years, with the rapid improvement and rapid development of the automation level of the manufacturing industry, the information tracking management of the production line has become more and more important. The core of realizing product information tracking management is to have a carrier that indicates the information of the product itself. Common information carriers include two-dimensional codes, bar codes, and radio frequency identification (RFID). RFID is a rapid identification technology that has developed rapidly in recent years. The stored information code is obtained through non-contact identification of the code carrier. The code carrier is also commonly known as the electronic tag (TAG). Compared with the traditional bar code technology, the electronic tag has the advantages of large data memory capacity; readable and writable, non-contact identification; high temperature resistance, corrosion resistance, and adaptation to harsh environments; and has the advantages of penetration It can read and write without barriers, and can penetrate non-metallic or non-transparent materials such as paper, wood, plastic, etc., and has a low misreading rate. Therefore, it is widely used in various industries.
This article introduces the use of RFID technology in the automobile manufacturing industry based on the actual project experience, and realizes the tracking management of the body information of the paint shop.
The overall structure of the system
2.1 The structure of the body tracking system
The paint workshop of Wuhan No. 2 Plant of Shenlong Automobile Co., Ltd. has reached the benchmark level of PSA’s global lean model factory from production management to manufacturing process equipment and technology. The body tracking system in the workshop uses the current advanced RFID identification technology, and the overall design structure of the system is shown in Figure 1. From the control point of view, it can be roughly divided into three levels as shown in the figure: basic equipment level, control level, and central management level; the ERP level belongs to the enterprise management level. The data flow of the car body is shown by the arrow in the figure. The data is transmitted in both directions between the levels, and the car body information required for production management is permanently stored in the data server. In the production process, crafts, robots, and conveying equipment can obtain the body information necessary to guide the production from the electronic tags.
Figure 1 Overall structure of RFID system
2.2 Brief description of the tasks of each component of the system
1) Central management: The EN data server is the data processing and management center of the entire system. Responsible for information management and control of the production process, connected to the ERP system of the enterprise, and under management of the production logistics guidance and information collection of the entire paint shop. The on-site client belonging to the central control system, through the application system CCR-View operating platform, can realize online query and modification of the actual car body information in the workshop, such as color, car model and other information.
2) Control layer: The local conveyor PLC mainly controls the operation of the conveyor chain, and is responsible for uploading and distributing vehicle body information. After receiving the information from the central management, it is responsible for transmitting it to the lower-level read/write station, and after receiving the lower-level read/write The information uploaded by the station is sent to the robot PLC, the large-screen display board and the process PLC. The electrophoresis line control PLC can call different voltage parameters when receiving different vehicle information; the painting robot PLC can be based on the received vehicle type and color information Choose different spraying trajectories and paint pipelines to spray paint to achieve process control. This project uses Schneider Premium 57 series 5634M CPU, and uses Ethernet connection to realize information transmission.
3) Basic equipment layer: mainly includes a complete RFID (Radio Frequency Identification System) and field operation terminal. The RFID system includes an electronic tag (Tag) and a read/write station. The electronic tag is used to store necessary body logistics information. The read/write station reads and writes data from the tag. The communication protocol of the read/write station is based on TCP/IP. It is directly connected to the control PLC via Ethernet; the on-site operation terminal is used to control the reading and writing station, providing a human-computer interaction interface for people, which can display the relevant information stored in the electronic label, and can realize the input and modification of local information in the case of emergency or information error , Query and other functions.
[ad_2]