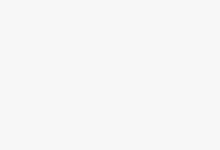
ZF uses RFID system to achieve regular maintenance during the launch period
[ad_1]
Automobile transmission and chassis manufacturer ZF Friedrichshafen (ZF) is now using RFID technology to manage the maintenance of the company’s production line engines in Saarbruecken, Germany. ZF has a total of 119 production sites around the world, and its fiscal revenue in 2007 exceeded US$12.6 billion. After successfully adopting passive UHF tags to manage parts in the Friedrichshafen plant, ZF began to expand the application of RFID technology throughout the company.
At the Saarbruecken plant, Friedrichshafen manufactures 4, 5, and 6-speed transmissions for cars. The company has already completed the labeling of 6,000 engines (running production machines and conveyor belts). These engines must be repaired and serviced regularly (2-3 months) to ensure the stable operation of production equipment.
Before the introduction of RFID technology, ZF relied on a metal tool identification plate attached to the engine to identify the engine. When workers need to identify the engine to be removed or repaired in the work order, they have to visually check the work order and the numbers on the metal plate. However, the common oil and dust in the production environment often makes the numbers difficult to distinguish. Tricon Consulting ZF project manager Jürgen Kusper said that Tricon Consulting is an Austrian software and hardware supplier and a system integrator for this project.
After adopting the RFID system, workers use handhelds to read tags to confirm which engines need repair, and they no longer worry about whether the identification code of the tool can be distinguished. Since the production machine must be kept running all the time, and employees need to turn off the entire engine for maintenance and testing, workers must replace the new engine after removing the engine from the production machine, and the old engine is moved to a spare parts warehouse and repair station. When the engine is repaired, the worker enters the number of the last repair order into the handset, and the system writes the repair data to the tag.
Workers use handhelds to read engine tags
This RFID system was officially launched in mid-2008. When the engines were moved to the warehouse for routine or special inspections, workers installed a passive high-frequency RFID tag on each engine. The label contains the 13.56 MHz Mifare chip from NXP Semiconductors. ZF chose passive high-frequency RFID tags because this application does not require long-distance reading. The label is encapsulated in a round, gray plastic jacket and adhered to the engine. The metal tool identification plate installed next to the RFID tag can be used as a backup.
Workers use Psion Teklogix handheld readers to write basic engine data on the tags. Every repair, maintenance information or plan will also be written into the RFID tag of the engine. In this way, employees can immediately understand the history of the engine by reading the tag. This information is stored in the tag, the memory size of the tag is 1 kilobyte.
In the testing phase, ZF tests the tags to ensure that they can withstand the abrasion caused by handling and cleaning in harsh industrial environments. The company said that so far there have been no problems with this system.
Tricon provided hardware and software and system integration services for this project. ZF Saarbrueckenr continues to add labeled engines.
ZF Saarbruecken is currently considering expanding this application. Kusper said that the RFID system reduces the time for workers to search for the engine and its related history, thereby reducing the overall cost of engine maintenance.In addition, if a problem occurs when an engine is purchased, its repair history can also be used for related claims
ZF plans to focus on expanding this system for material flow and parts management, tracking spare parts entering and leaving the warehouse.
[ad_2]