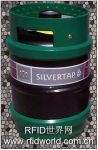
Free Flow Wines launches RFID barrel tracking system
[ad_1]
The Free Flow Wines factory in Sonoma County, USA produces, stores and transports Silvertap organic wine made from 6 types of local grapes. The factory does not use bottles for wine, but uses recyclable plastic barrels. And bars can sell wine by the bosom instead of the traditional bottle. The company uses nitrogen to fill wine from wooden barrels into plastic barrels (stored for several months). The company uses RFID technology to track the location and status of these plastic barrels to ensure their timely return, correct cleaning and refilling.
Free Flow Wines just opened a year ago. Currently, it sells 200-300 barrels of Silvertap per month and is shipped by distributors to restaurants and bars across the United States. However, as the company grows, Free Flow Wines needs a system that can automatically Track the location of the reusable plastic bucket. RFID technology is a good choice, according to Jordan Kivelstadt, creator and production director of Free Flow Wines, the company uses a system provided by Mobile BIS.
The barrel manufacturer inserts a UPM Raflatac DogBone UHF EPC Gen 2 tag between the barrel and the plastic handle on the top of the barrel
Free Flow Wines has completed the labeling of all plastic barrels in the past few weeks and shipped them to the distributor. If this system works as expected, the system’s automatic tracking function will reduce the frequency of loss of plastic barrels (the phenomenon of barrel loss often occurs in the wine industry, and the loss is serious); and this system can also ensure that the plastic barrels are cleaned correctly and in time. Reuse, if there is a recall, you can quickly locate all buckets. The company will also learn about the percentage of plastic drums not returned by dealers, and investigate the delivery time and destination of the unreturned drums in a timely manner. Moreover, by knowing the return time of the barrel, the company can return the deposit to the dealer more quickly.
“Before the adoption of RFID, the company had considered barcodes. The biggest reason for not adopting RFID was that barcodes could only be scanned one at a time,” Kivelstadt said.
Using the RFID system, the barrel manufacturer embeds a UPM Raflatac DogBone UHF EPC Gen 2 tag between the barrel and the plastic handle on the top of the barrel, and then Free Flow Wines writes a unique ID code to the RFID tags of 4,800 barrels. .
The employee uses the Psion Teklogix handheld to read the barrel label and write the date and other information
When the plastic barrel is filled with wine, the employee uses the Psion Teklogix Workabout Pro handheld with an embedded RFID reader module to read the ID codes of all plastic barrel labels in a batch, and also enter the time and date, as well as the wine in the barrel. type. The data is then sent via a Wi-Fi connection to a server in charge of Mobile BIS, where the information is stored in an Oracle 10g database.
Free Flow Wines managers then log in to the WEB-based software system to obtain relevant data. There are a total of four reading points in the whole process, when the plastic bucket is delivered to the dealer (the dealer’s name is entered at that time), when returning to the dealer, when cleaning, and when detecting faults.
Mobile BIS has designed server software specifically for this application, according to Michael Macho, Chairman of Mobile BIS. This system helps Free Flow Wines establish company rules, such as adding additional read points or setting alarms. For example, if plastic barrels reach the upper limit of use time, the system can send emails or text messages to employees; the system can also provide business analysis, Macho said, such as how many barrels of wine a certain dealer purchases in a year and the sales volume of a certain type of wine.
In the near future, Kivelstadt stated that the company hopes to sell thousands of barrels of wine every month. The RFID system can ensure that distributors return to the barrels as soon as possible, clean and refill them as soon as possible, thereby reducing barrel turnaround time.
[ad_2]