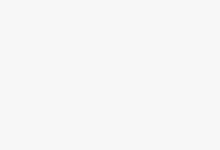
Yoshinoya meets IT: RFID helps companies realize fresh delivery
[ad_1]
Nowadays, in almost all commercial centers in the capital, you can see the scene of Yoshinoya’s beautiful city. It should be said that China’s fast food industry is the product of rapid development in the past 10 years. Take the restaurant chain Yoshinoya as an example. In 1992, the first domestic Yoshinoya signboard was hung in Beijing. It was not until 2000 that Yoshinoya’s 9th store in Beijing officially opened. Since 2001, almost 10 stores a year Speed quickly gained a foothold in the fast-food restaurant market in Beijing. Today, there are more than a hundred Yoshinoya restaurants in the capital, and you can see the Yoshinoya restaurants in almost all commercial centers.
When fast food meets IT
The 10 years in which the fast food industry has fully blossomed are the 10 years in which IT information technology has fully penetrated into various fields. The development of information technology in the fast food industry has effectively promoted the rapid growth of fast food companies headed by Yoshinoya in terms of efficiency improvement and food safety. . So, when catering meets IT, how does IT help fast food companies ride the wind and waves? Let’s take a look at Yoshinoya, who broke through and succeeded in Western fast food chains.
Like other Western fast-food chains, the more stores there are, the greater the challenge. Because only by allowing customers to enjoy the same quality and taste dishes at each Yoshinoya restaurant, can they win the customer’s lasting trust and maintain the Yoshinoya fast food consumption habits that have been cultivated with great difficulty. The basis for the unification of dishes is the unified supply of ingredients. Yoshinoya, which uses rice and other oriental cuisines as chain dishes, has more ingredients than Western fast food such as hamburgers and sandwiches. It is more challenging to achieve unified delivery of all fresh ingredients. . Therefore, Yoshinoya strictly selects various ingredient suppliers, and each unified ingredient supply base distributes the ingredients to each restaurant every day to ensure the unity of Yoshinoya throughout the city.
RFID helps achieve fresh delivery
Food ingredients are different from other products, and freshness is always the first priority. The ingredients are transported out of the warehouse and transported to each restaurant by refrigerated trucks. In the process from out of the warehouse, transportation to receipt, each ingredient must be kept within a suitable and relatively constant temperature range to ensure that each restaurant receives it. The ingredients are fresh and intact.
In order to achieve the goal of full freshness, Yoshinoya put forward strict standards. Today, Yoshinoya is equipped with an RFID radio frequency identification cold chain temperature monitoring system customized by NEC. This small RFID temperature tag-it is equipped with a chip and a temperature sensor inside, and is equipped with an ultra-thin button battery, which can be used continuously for more than five years. The temperature information collected by the temperature sensor at all times can not only be stored in the RFID chip in real time, but also can be transmitted through the RFID read-write antenna, and can realize long-distance reading and writing (the longest distance is 30 meters).
When the food is stored in the warehouse, Yoshinoya can constantly observe and record the temperature information of the food incubator through RFID. At the same time, the RFID cold chain temperature monitoring system well covers the entire refrigerated truck transportation system. During transportation, the RFID temperature tag on the incubator not only faithfully records the temperature changes of the ingredients, but also transmits the temperature data to the management system of the Yoshinoya headquarters in real time through the GPRS wireless transmission system installed on the top of each transportation vehicle. In this way, the staff can get the real-time temperature situation of the ingredients without leaving the house. Once the temperature is abnormal, the system will automatically alarm, and the driver can take measures as soon as the temperature is abnormal, thereby avoiding the risk of cold chain caused by human negligence.
Since then, Yoshinoya’s logistics management staff only need to sit in the headquarters office to observe the temperature of the ingredients from time to time.
“Distribution on demand”-unified quality and cost savings
Also based on the requirements for the freshness of ingredients, and in order to ensure the on-demand delivery of various ingredients in various restaurants, avoid waste or insufficient supply of ingredients, basically realize the “on-demand distribution” of ingredients for each restaurant, Yoshinoya headquarters, restaurants and warehouses Through NEC’s WMS warehousing and logistics management system, you can observe the supply and demand of food at any time, realize barrier-free communication, realize the perfect combination of batch, cargo location and temperature management, and greatly reduce operating costs.
It is no exaggeration to say that every bowl of delicious beef rice contains information technology. It is for this reason that the fast-food industry has developed so rapidly. We look forward to more information technology products entering the fast food industry to help the entire fast food industry to fully informatize and achieve the rise of more trustworthy fast food brands like Yoshinoya.
[ad_2]