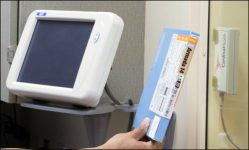
BJC Medical Center uses RFID storage cabinets to track medical consumables
[ad_1]
BJC Medical Center operates 12 hospitals in Illinois and Missouri and is currently usingRFIDThe technology tracks and manages the thousands of medical consumables it uses.
The HF RFID system uses a cabinet with a built-in reader, passive HF RFID tags, a handheld reader, and Cardinal inventory management solution software running on a cloud server to manage the collected data. These are all Provided by Cardinal Medical. This technology was first used in the cardiac catheterization laboratory, followed by the gastrointestinal (GI) laboratory, interventional radiology department, and operating room. At present, the company has installed 70 cabinets in 27 rooms in 9 departments and 5 hospitals, tracking a total of 2,708 stock-keeping unit items (SKU). It is expected that the system will be deployed in the first quarter of 2017, when 3 to 5 times the number of existing cabinets will be installed in its 12 hospitals.
BJC is the largest non-profit medical institution in the United States, and its services are in the Greater St. Louis area, central Missouri and southern Illinois. These hospitals use medical equipment or implant medical consumables in patients during surgery.
BJC Supply Chain Operations VP Stephen Kiewiet said that before installing the RFID system, these hospitals used a variety of methods to control equipment and consumables. The hospital purchases a large number of items from the supplier, and will inventory the unused items. Hospitals need to closely track the expiration date of products to avoid expiration and discarding. In addition, items are sometimes lost, and hospitals need to spend a lot of labor to check inventory or recall products.
Kiewiet said: “These departments are very busy. Sometimes the items seem to be in small quantities, and they will replenish them.” This manual replenishment process can cause excess inventory on site. Using RFID technology, BJC believes that they can know the location, expiration time, batch and serial number of the item in real time.
In 2014, the hospital began piloting use in 2 cardiac catheterization laboratories and a gastrointestinal laboratory, which lasted less than one year. Subsequently, BJC increased its capital to use this program in all medical and surgical supply rooms.
Some items have been affixed with HF RFID tags by the supplier before they arrive at the hospital, and hospital employees need to tag other items. According to Jean-Claude Saghbini, General Manager of Cardinal Medical Inventory Management Solutions, employees use a variety of brands and models of 13.56 MHz tags that are compatible with the ISO 15693 standard.
For those products that are not pre-marked by the manufacturer, the staff must first scan the QR code on the packaging of the item. The QR code contains the universal product number (UPN), model, batch, serial number, and expiration time information of the item. By scanning the QR code, employees can bind this information to the RFID tag to be attached. In this way, employees can start to read the RFID tag using shelf or handheld readers. These data are stored on Cardinal Medical’s cloud server.
These items will be placed in the Cardinal medical cabinet in the storage area of each laboratory. The RFID reader of each cabinet reads the item tag ID number and transmits the data back to the software through the hospital’s local area network. Then, the software will update the item status to stored.
When a specific item is needed for a diagnosis and treatment, the staff will take it out of the cabinet. After the item is taken out, the cabinet will not be able to read the label, so the software will judge its status as taken out. In the operating room, the doctor will use the RFID reader to read the tag ID and assign it to a specific patient for use. The cloud software will collect this data and update the item status as used. If the item is not used, the employee will put it back on the cabinet. If the item has not been read by the operating room reader and has not been put back into the cabinet, the software will judge it as lost and warn it on the software dashboard. Kiewiet said that he or other employees would log in to the software every day and would ask the doctor on duty to inquire about the situation when they found a warning.
In the six months since the pilot project, BJC has discovered the advantages of this system. The biggest advantage is that it reduces losses due to expiration, improper placement of items, and low inventory visibility. Kiewiet hopes that the RFID system can also reduce losses caused by employees spending on inventory counting or searching for expired items. In addition to these two cardiac catheterization laboratories and a gastrointestinal laboratory, other cardiac catheterization laboratories have also begun to use this system.
In addition, clinicians can also check whether consumables such as implants in use are out of date on the computer screen in the operating room.
Kiewiet said that after the system is put into use in all departments, the company will launch a new Epic medical record system. At that time, the company will integrate the Epic system and Cardinal’s label data collection system. In this way, when the lab reads the label, the information will be automatically bound to the medical record, simplifying the billing process.
BJC hopes to use the RFID system to determine the frequency of use of specific items and understand the information of items that expire before use, thereby reducing unnecessary inventory. At the same time, BJC will use this system to share information about less frequently used items, thereby reducing large-volume orders.
BJC is sharing these data with some suppliers to help them better manage inventory. These companies can know the time of use of consumables, the expiration of consumables and the time of replenishment.
In addition, BJC also uses the Cardinal handheld reader to read items that are not stored in the cabinet. Saghbini said the program is designed for medical consumables rather than reusable assets.
The use of high-frequency RFID technology instead of ultra-high frequency technology is to ensure that the tag can only be read within a controlled storage range, thereby preventing misreading. In addition, high-frequency tags are better used in metal and liquid environments. These labels are cheap, and medical institutions can use them on all types of goods. According to Saghbini, every year the country wastes $5 billion on high-value medical implants due to expired and excessive purchases.
[ad_2]