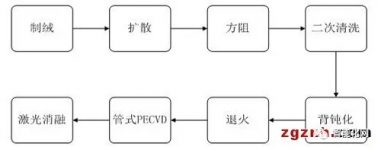
Application of Yike’s RF30 series RFID products in the production traceability system of photovoltaic PERC crystalline silicon cells
[ad_1]
As a renewable clean energy, solar energy has become one of the energy fields with the most potential for development. As an efficient way to use solar energy storage, solar cell technology has also undergone rapid upgrading. For the commonly used crystalline silicon battery technology, the most convenient technology upgrade solution is PERC, which is the emitter and back passivation battery technology. Compared with ordinary batteries, PERC batteries add back passivation, laser slotting and other processes, which can make the photoelectric conversion efficiency higher, which also puts forward higher technical requirements for the production process and manufacturing process.
In order to build a high-efficiency PERC battery production line, a photoelectric technology company in Hunan introduced an MES system to the existing automated production line. Among them, the most important method of obtaining data for the production of monocrystalline silicon wafers uses RFID technology.

The main process flow of PERC battery
Since the entire production process is relatively complicated and involves the immersion process of corrosive liquids such as pickling and alkali washing, an efficient and reliable identification scheme will definitely help the operation of the MES system. Relying on the rich experience accumulated in the field of automation for many years, Eike applies the RF30 series of RFID products to provide a complete RFID solution for the entire PERC battery production system:
1. Install custom-developed corrosion-resistant code carriers for all flower baskets (trays) that carry silicon wafers. Use the existing mounting holes of the flower baskets to customize the shape and size of the code carriers to make the installation of the code carriers convenient and efficient;
2. Install the RFID Q80U UHF read-write head at the entrance of the main process section to read the serial number of the monocrystalline silicon wafer passing through the process section, so that the MES system can record and track the current batch of data;
3. After the completion of the process section, the RFID Q80U read-write head at the exit position reads the serial number of the code carrier of the pallet again, so that the MES system can make statistics on the completion of the current batch.
The entire RFID system adopts the Q80U read-write head of ultra-high frequency technology as the read-write terminal of the tag data, and the read-write data is high-speed and accurate. The data interface adopts the PROFINET bus protocol, which is convenient for integration and on-site debugging. Standardization and modular design greatly shorten the implementation time of the entire MES system.
product model:

Reader:
Considering that the distance between the on-site read-write head and the tray is basically maintained at 10-20cm, and is limited by the installation space, it is the best choice to install a small-size read-write head at a close distance. At the same time, in order to ensure the reliability of dynamically reading tag data, The electromagnetic field of the read-write head is required to cover a larger read-write area as much as possible. Therefore, the RFID Q80U UHF read/write head is the best choice.

Q80U read-write head to read the data of the pallet
The Q80U read-write head adopts a brand-new appearance design, optimized internal circuit structure, and a more stable UHF UHF dual-feed point antenna. The maximum recognition distance can reach 300mm, and the transmission power can be adjusted according to site needs to meet different installation distances. The read-write head is required to read the tag data stably.
Interface module:
In order to ensure the reliable operation of the entire system, the MES system adopts the design concept of control and information shunting. The PLC responsible for the operation and logic control of the entire process equipment is only used for control, while the RFID equipment uses an independent PLC for tag data reading and At the same time, the PROFINET bus network is used in the project to network the RFID devices of each reading station, and configure and communicate with the PLC, and the MES server obtains the relevant information through the PLC.
Each distributed standard RFID gateway can connect up to two Q80U read-write heads, and set up 4 I/O signal interfaces, so that the sensor signals such as photoelectric switches can be connected nearby, so that the system can achieve fine control of the RFID read-write head .

MES system network structure
Code body:
Since the upgrade and transformation of the entire MES system needs to be carried out without stopping production, higher requirements are put forward for the installation time of thousands of pallet code carriers. At the same time, since silicon wafers and trays have to undergo necessary processes such as acid-base treatment and cleaning, higher requirements are also put forward for the corrosion resistance and waterproof performance of the label.
In the code carrier solution customized by Ike for customers, the outer dimensions of the label are designed according to the installation space reserved for the pallet, and the PVDF material shell is used for packaging to ensure that the pH value is 4-9 and the temperature is -40℃~ It can be used stably for a long time in the range of 150°C.

Corrosion-resistant code carrier installed on monocrystalline silicon wafer tray
User benefits:
·The application of RFID products from Eike provides real-time statistics of pallet information for the customer’s MES system, which can track and control the monocrystalline silicon wafers in the entire process flow, and realize the intelligence, visualization and transparency of the process flow in the production workshop.
·Through the RFID Q80U UHF read-write head to identify the tray, optimize the production process, and through the intelligent analysis and processing of the data, realize the management intelligence, and promote the cost reduction and efficiency increase of photovoltaic cell manufacturing.
·The successful implementation of the PERC battery intelligent manufacturing production line project reduced the labor intensity of front-line workers, increased the overall production capacity of photovoltaic cells, and provided reliable product guarantees for the utilization and promotion of new energy.
In addition, the application of Q80U UHF RFID products has improved customers’ production efficiency and product yield, providing a model for the standardization and standardization of the entire industry.
[ad_2]