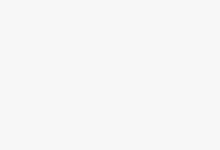
Ling Frog Manufacturing Execution System (LINX-MES) Application Case
[ad_1]
User: Shanghai Schneider Electric Power Distribution Co., Ltd. (Sino-French joint venture)
Shanghai Schneider Electric Power Distribution Co., Ltd. was established as a joint venture between Schneider Group Corporation and the Shanghai local government in 1996, with an investment of 18 million US dollars and more than 200 employees. Its main product has international leading advantages, and it is the only manufacturer in China that produces this product.
The company produces according to the production-to-order (MTO) model. Orders are small in batches and have many changes. Sometimes an order has only one finished product. The production process and product specifications are not continuous. In addition, there are many types of parts and employees face changes at any time. In order to meet the order, wrong installation, multiple installation and missing installation of parts will occur, which will affect product quality and reduce production efficiency.
Since the products of this company belong to industrial electrical appliances, once quality problems occur, it will have a great impact on customers, and at the same time, it will definitely affect the competitiveness of the company’s products. The quality of parts is an important factor that causes problems in the use of products. However, when a company discovers that a certain important part of a finished product has a hidden quality problem, it cannot quickly and accurately locate the product using the same batch of parts. Therefore, Failure to make up for defects and reduce losses in time.
Another major problem with Schneider is that the production line is divided into three sections: two sub-component production sections and a final assembly section. The semi-finished products of the two sub-sections require high synchronization. Due to the small batch and multiple changes of orders, the ERP system cannot effectively schedule production accurately to the production section, which often results in inconsistent production between the two production sub-sections, and the final assembly section is often in a waiting state.
Beginning in 2002, the implementation personnel of Shanghai Lingfrog Technology and Trade Co., Ltd. and Schneider production management personnel have conducted many communications and analysis, and grasped the above major issues, and around these major issues, built the most suitable The manufacturing execution system of the enterprise.
First of all, in response to the production scheduling problem, Lingfrog uses its previous experience in successfully integrating with mainstream ERP products to connect the company’s existing ERP (SAP) system and MES system into an organic whole, and design and optimize production scheduling algorithms according to the actual production of the company. The ERP production plan production process is decomposed into each section and process of the production line, and on the basis of giving full play to the production capacity of each section, the synchronization of the final assembly of the product is ensured, and the on-time delivery of the product to the customer is also guaranteed.
The designers of our company use bar code automatic identification technology to build a complete automatic identification and traceability system for materials and finished products for the enterprise. Unify the raw material code and finished product identification code. During the production process of employees, the system automatically records which materials are used for each finished product. Because the materials and finished products already have an “ID card”, once a quality problem occurs, the company can quickly find other related products that may have problems, and minimize the company’s losses by replacing parts for customers in a timely and accurate manner. Recognized.
With the automatic identification system of materials, Ling Frog has implemented a production process control module for the enterprise, and through a flexible production process customization mechanism, a standard production route is formulated for each finished product. In the actual manufacturing process, if an employee fails to install a wrong or multiple installation, the system will automatically remind and strictly control the continuation of the manufacturing process to ensure the correctness of the production process, and every unqualified operation is timely. control. In addition, data interaction with large-scale test equipment is realized, and the results of quality inspection are directly applied to the process control of the system.
Shanghai Lingwa Technology and Trade Co., Ltd. uses the Lingwa management platform independently developed by the company for development. Both the server and client operating systems use the WINDOWS series, which is easy to operate and maintain. Since the design of the workshop did not consider the wiring problem when the factory was built, we designed a network architecture that combines local area network, RS845 and 802.11b wireless network for the enterprise, which enhances the convenience of enterprise use.
The design of system architecture and data structure has reserved interfaces for the vision of comprehensive enterprise informatization, which can be integrated with other top-level or bottom-level information systems (such as CRM, SCM) at any time. The application of advanced management platform and development technology also ensures the easy upgrade and secondary development of the system.
The entire system has set up 24 data collection points, and the implementation period is 4 months. The entire implementation process has received strong support from the high-level leaders of the enterprise and foreigners.
After the implementation of the system, due to the strict process control mechanism adopted within the system, the defective rate of finished products in Schneider’s production process has been reduced by more than 50%, and the phenomenon of incorrect, over-installed or missing parts has been basically eliminated, and the production efficiency has also increased by 20%. % Improvement. A detailed file relationship is established between the product and the raw material, and the loss caused by the raw material defect is reduced to the lowest point in the quality management. Accurate production scheduling enables products to be produced on time, improves factory efficiency, and delivers to customers in a timely manner.
Through the collection and analysis of production data for a period of time, detailed basic data and analysis results helped Schneider find some unreasonable configuration of the production line, and through gradual adjustment, the production capacity was greatly improved. At present, the system has gradually been promoted and used within Schneider Group.
company profile:
Shanghai Lingwa Technology & Trade Co., Ltd. is a high-tech enterprise specializing in providing comprehensive solutions for barcode application systems.
The company has an excellent software development team and experts who have been engaged in barcode research and application for many years, and are familiar with enterprise manufacturing and management processes. A series of barcode application software has been developed and developed by itself. It has many customers in all walks of life, from manufacturing, Wholesale, sales and retail services to maintenance, transportation, warehousing, government departments and public utilities are well received by customers.
After several years of hard work, the company has established strategic partnerships with many well-known hardware manufacturers at home and abroad.
The main products of the company’s software division, MES and WMS, were awarded the titles of “Excellent Recommended Products” and “Excellent Successful Cases” in the 2004 annual inventory of manufacturing informatization.
contact method:
Tel: 021-64687977, 64687978 Address: 9D, Zhonghua Gate Building, 520 Yishan Road, Shanghai
Fax: 021-64687335 Website: http://www.linxvalley.com.cn
Postcode: 200233 E-mail: linx@ linxvalley.com.cn
[ad_2]