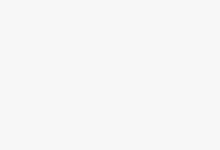
Intermec automatic identification solution brings perfect workflow
[ad_1]
Every company will pay a different price for mistakes.
Sometimes this cost needs to be accurately measured, such as a sudden decrease in sales; sometimes this cost may be more subtle and less noticeable, such as the unknowingly lack of consistently good reputation. Suppose there is a situation: a certain company has a certain error, and before the error is corrected, the company will lose a large amount of money every minute, which will inevitably make the company highly nervous. For a time, auto parts manufacturer ThyssenKrupp Budd faced this situation every day. For ThyssenKrupp Budd, reducing errors in packaging and transportation is not only a need to be responsible to customers, but also vital to the development of the company.
Company Profile
ThyssenKrupp Budd is part of the German ThyssenKrupp Automotive Company, one of the world’s largest auto parts suppliers. Headquartered in Troy, Michigan, USA, it operates 30 factories in North America. ThyssenKrupp Budd designs and produces parts for more than 100 motor vehicles, has 11,000 employees, and has annual revenues of more than 2.5 billion U.S. dollars.
Challenge and response
Research by automakers has shown that errors in the transportation of parts are the main reason for the interruption of the assembly line. Therefore, automakers often warn their suppliers that labelling errors can bring serious consequences and even lead to the suspension of the entire production line.
ThyssenKrupp Budd produces different parts in different parts of its North Baltimore plant in Ohio. Two parts with similar appearance but different functions will be produced at two locations 50 feet apart, so there is little possibility of mixing them together. However, after casting, these parts and other parts will be concentrated in the spray paint production line, painted with the same color and dried. This greatly increases the possibility of errors.
ThyssenKrupp Budd has already strongly realized the importance of maintaining this accuracy before the transportation link is running accurately. Therefore, they chose the technical solution of Intermec and its partner ToolWorx Information Products Company to keep the transportation link error-free.
The advanced ITM solutions provided by Intermec (Identify, Track and Manage) are widely used worldwide. In the early years, Intermec invented the most widely used 39-code barcode in the world Technology. Today, as the world’s leading developer, production and integrator of products and solutions for automatic data collection, item tracking and item management, Intermec’s barcode scanner equipment, MobileLANTM wireless local area network and wide area network data acquisition equipment,IntelLitag RFID®, barcode printers and consumables have long been famous in the field, especially in the field of RFID. Intermec, which has many key patent technologies, is playing an important role in this field.Now, Intermec has hundreds of top companies in 70 countries around the worldsoftwareIntegrators have reached a cooperative relationship and established a huge sales and service network to provide services for 75% of the Fortune 500 and 60% of the Fortune 100 enterprise users, helping these global industry users to improve production efficiency and product quality , Improve the rapid response degree of business operations. From supply chain management, enterprise resource planning to on-site sales and service, people can easily find Intermec.
Ed Weber, vice president of sales and marketing at ToolWorx, believes that the solution to this problem is very simple. He believes that “if the correct barcode label is affixed to the first part at the beginning, then it can be accurately scanned and tracked in all subsequent links. As long as the parts are marked, error prevention and Traceability can be achieved smoothly.”
Industrial scanning, printing, wireless transmission: Intermec’s solution
ToolWorx willsoftwareInstalled in Intermec’s EasyCoder F4ci barcode printer, it becomes ToolWorx Programmable Logic Controller (TWPLC) printer.This smart printer comes with aindustryThe panel and the internal computer programmed in the Fingerprint language completely eliminate the need for a separate personal computer to drive the printer.
In the manufacturing process, the programmable logic controller is a small computer installed inside the parts processing machine to control the operation of the machine. The TWPLC printer can be directly inserted into the parts processing machine. In the process of punching or molding each part, the processing machine will send a digital signal to the TWPLC printer, and the TWPLC printer can obtain the part number corresponding to each signal through the program, so as to print out each part number. Barcode labels that match the parts.
Weber commented: “There is no PC, no keyboard, no need to connect to the network to enter any programs, and no need to guess or estimate. Everything is done by a printer. And this printer is convenient and easy to carry, and workers can use the printer. Unplug it and take it wherever it is needed. The only requirement is that there is a 110-volt power outlet nearby and a connection port to the PLC.”
When the parts are off the production line, workers will affix the just printed labels on them. Each label is individually manufactured according to the command language sent by the parts manufacturing machine. After each part is labeled with the correct label, these newly cast parts can be transported across the factory and mixed with other similar-shaped parts because their labels will reflect their differences.
The most frequent place for parts to go back and forth is the painting line. For example, a large number of engine covers need to be painted here and baked in a toaster. Intermec’s heat-resistant labels can be fixed on parts and can withstand high temperatures of 325 degrees.
In the finishing workshop, all parts are packed into boxes, waiting for delivery. The barcode label on each part is first scanned by the Intermec1552 wireless laser scanner. Workers can walk freely in the workshop while scanning labels, and can scan barcode labels 50 feet away from the Intermec9745C base station. Scanners and base stations form Intermec’s wireless local area network and work through the 2.4GHz wireless frequency. Each base station can accommodate 9 scanners working simultaneously.
After each scan, the information on the barcode label will be transmitted to ThyssenKrupp Budd’s SAP R/3 system via wireless equipment. After a certain number of the same parts are packaged, the software toolkit provided by ToolWorx, namely Loftware, will be connected to the SAP R/3 system and the information will be sent to the Intermec EasyCoder 3400e or 3600 label printer to print out the shipping label . In sharp contrast to this, all previous shipping labels were printed in batches, and then workers put the corresponding labels into the correct containers.
Scott Stemen, a quality control manager at ThyssenKrupp Budd, said: “We not only verified the part number, but also the number of parts. If someone scans the error, the system will send out a visual alarm, and it will be reflected on the computer monitor. come out.”
Stemen believes that the greatest benefit of Intermec’s intelligent printing system is customer satisfaction. Whether the system is installed or not has become a decisive factor for the customer to choose between two suppliers with the same quotation. When customers see that you take steps to help them avoid potential mistakes, they will definitely shine!
end
In my country, Intermec ITM (Automatic Data Acquisition and Item Tracking Management) solutions have entered various industries, especially in the construction of logistics supply chain has played a huge role: from manufacturers to transportation service providers, wholesalers, retailers and The customer’s entire process adopts Intermec’s automatic data collection and mobile computing solutions to varying degrees; at each key point of business activities, such as manufacturing origin warehouses, shipping docks, trucks, and even stores, managers and clients, Intermec’s ITM Products and solutions are everywhere: it connects the movement of people and objects with real-time information, and provides customers with real-time collection of production information at production sites, real-time tracking of items, and real-time management of moving items, effectively improving production efficiency. Reduce labor costs, optimize work processes, and improve customer satisfaction and sales. All of this reduces the user’s operating costs and enhances the competitive advantage of enterprise users. Intermec’s ITM automatic data collection and item tracking management concepts effectively combine products, managers, space and time in a timely manner to achieve transparent, accurate and efficient data management.
[ad_2]