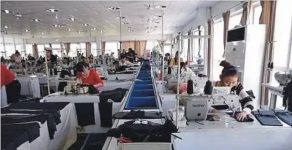
RFID helps garment factories reduce rework rate from 25% to 3%
[ad_1]
The clothing production managers are most concerned about two things, one is output, and the other is quality. Today, I will talk to you about the key indicator of the quality control of garment production-the rework rate.

The rework rate remains high. Generally speaking, either the process is unreasonable or the machine has a problem, which leads to a high rework rate of a certain style. In this case, the manager must find out and deal with it in time to avoid more defective products. ; Either the workshop management is not in place, especially the defective products cannot be traced back to the people accurately, causing everyone to shirk each other’s responsibilities and fail to improve the quality awareness of all employees.
For the treatment of defective products, the current common method is to produce them on the same day. All employees will spend half an hour to an hour together before the end of get off work on the same day and deal with them on the same day. However, this delays normal production, and some factories may not be able to clean up on the same day, resulting in a backlog of defective products.
As for personnel management, generally, the rework rate of each worker is high or low, and if it exceeds a reasonable or average range, money will be deducted in a stepwise manner. This requires that the rework rate data must be accurate and convenient to record. Inaccuracy will cause dissatisfaction among workers, and cumbersome methods will increase the difficulty of the quality supervision department and make it difficult to implement.
XXX garment factory encountered this difficulty. They have relatively high requirements for product quality. Manager Lin has also done a lot of work in quality management and put forward various requirements for each inspection post.
For example, QC is required to manually draw “positive” characters to count the relevant quality inspection data, but the rework rate has been maintained at 25%, which cannot be reduced.
After analysis, there are several problems:
1. The inspection data and defect data are inaccurate. Because it is manually registered, once the pipeline cannot keep up with the beat of the assembly line, the data is often inaccurate if it is filled after the fact.
2. The inspection data and defect data are not timely. On the one hand, it is the reason for the post-reposting. On the other hand, the relevant data can not be counted until at least the work of the day is completed, causing the problem to be discovered and resolved the next day;
3. There is no way to record the information of the production staff that caused the defect, and it is impossible to guide the production staff to improve and solve the defect problem in a targeted manner;
4. To fill in multiple inspection reports at the same time, resulting in too many inspectors’ actions, which seriously affects the work efficiency of employees;
5. There is no way to count the re-inspection process and data of reworked products, so there is no way to accurately consider the actual number of inspection pieces and the number of defects of each inspector, and there is no way to count the number of pieces and the number of defects that each inspector missed. Therefore, It is difficult to conduct performance appraisal for inspectors.
In the final analysis, what Mr. Lin needs is data, accurate and timely data! But where does the data come from? After trying various methods, Mr. Lin finally found the answer in RFID technology.
RFID (Radio Frequency Identification), that is, radio frequency identification technology, is a communication technology that uses radio signals to identify specific targets and read and write related data. It has been widely used in production management, warehouse management, access control cards, traffic cards and other fields.
After more than two months of exploration and trial operation, Mr. Lin has comprehensively promoted the use of RFID technology to record and count quality management data throughout the plant, and achieved good results.
The basic idea of optimizing the quality inspection process is:
RFID data collection terminals are installed in semi-finished product inspection (interim inspection), finished product inspection (final inspection), and subsequent inspection (final inspection), which can collect inspection data and defect data of all production lines and subsequent lines in real time, and generate various aspects at any time The report form is convenient for managers to find and solve problems in time.
Step 1: Count the top 10 defects of each production line, and focus on solving the problem of high defect rate

Step 2: Perform data analysis according to the defect rate report to find the problem.

Step 3: Summarize the defect rate, display the quality of each production line, and focus on teams with a higher defect rate.
The specific operation method is:
1. After adopting RFID data collection terminal, all inspection data and defect data are recorded by swiping card. Each RFID data collection terminal is equipped with several RFID cards, and the inspection is passed and each defect cause is equipped with an RFID card. After the inspection is completed, the inspector can only swipe different RFID cards according to the actual inspection results to complete the data. The recording work greatly reduces the workload of the inspectors and improves the work efficiency of the inspectors.
2. At the same time, an electronic kanban is installed on each production line to display key data such as the target output, the number of put into production, the number of finished products, the number of defects, the defect rate, and the target of the defect rate on the day to all production personnel and inspectors for viewing. The activities can be made transparent, so that every production staff and inspector can know well and have a clear goal.
3. Set the target value of each inspection post for semi-finished product inspection (interim inspection), finished product inspection (final inspection), and subsequent inspection (final inspection) of each production line. Once the defect rate of a certain inspection post of a production line exceeds the target value, Immediately send reminder emails to the mobile phones of the relevant personnel of the quality control department and the technical department, and immediately notify the relevant personnel to rush to the scene to find the cause of the defect and solve the defect;

4. Data statistics for production personnel can easily find the personnel or reasons causing the defects and improve them.

5. Perform data statistics for inspectors, which can count the actual workload of inspectors, and include re-inspection of reworked products.

After XXX Apparel Co., Ltd. implemented and implemented RFID technology for nearly half a year, the defect rate of semi-finished products inspection (intermediate inspection) was controlled within 15%, and the defect rate of finished product inspection (final inspection) was controlled within 8%. ) The defect rate is controlled within 3%, which can basically achieve the pre-determined target, which provides a solid foundation for the further development of the enterprise.
[ad_2]