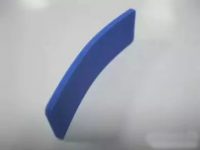
Application of RFID technology in linen tracking management system
[ad_1]
Hospitals, hotels, linen factories or any companies that need to deal with several types of textiles need to sort the linen for cleaning. The sorting process usually requires 2-8 people to sort the linen into different chutes, and it may take several hours to sort all the linen.
1Reduce manual linen sorting
With the RFID linen management system, RFID tags are sewn into each piece of linen. When the RFID tags pass through the assembly line, the RFID reader will send a query signal and read the tags. After all tags have been read, the system will confirm what type of linen is being read, and send the linen to a suitable place or machine. The processing result of the system will be displayed on the screen, so that you can immediately send your linen to the next place.

RFID tags
Companies now use RFID to eliminate human linen sorting and greatly reduce the labor expenditure on linen sorting. Instead of relying on human eyes to distinguish bar codes or distributing grass, now only 1-2 people need to be assigned to send the linen to the next procedure in an orderly manner.

RFID linen tracking flow chart
2Provide accurate records of cleaning quantity
The number of cleaning cycles of each piece of linen is a very important data, and the cleaning cycle number analysis system can effectively help predict the end of life of each piece of linen. Most of the linen can only withstand a certain number of high-intensity washing cycles, and the linen will begin to crack or damage after exceeding the rated number of times. It is very difficult to predict the end-of-life date of each piece of linen without a record of the quantity of cleaning, which also makes it difficult for the hotel to formulate an order plan for replacing the old linen.

RFID, linen, washing machine
When the linen comes out of the washing machine, the RFID reader will detect the RFID tag sewn into the linen. Immediately afterwards, the number of cleaning cycles for the linen will be uploaded to the system database. When the system detects that a piece of linen is approaching its end of life, the system will prompt the user to re-order the linen. This procedure can ensure that the company has necessary linen inventory reserves, thereby greatly reducing the replenishment time due to linen loss or damage.
3Provide quick and easy visual inventory management
The lack of visual inventory management will make it difficult for companies to accurately formulate emergency response plans, achieve efficient operations, or prevent linen loss and theft. If a piece of linen is stolen and the company does not implement daily inventory audits, the company may face the risk of potential delays caused by inaccurate inventory management in its daily operations.
The RFID tags sewn into each piece of linen can help companies perform daily inventory management faster and more efficiently. The RFID reader placed in each warehouse will conduct continuous inventory monitoring to help pinpoint exactly where the linen is lost or stolen. Inventory reading through RFID can also help companies that use outsourced cleaning services. Read the inventory quantity before sending the linen to be washed, and read the quantity again when the linen is returned to ensure that the linen is not lost during the final washing process.
4Reduce loss and theft
At present, most companies in the world are still using simple, human-dependent inventory management methods to try to count the number of lost or stolen linens. Unfortunately, when relying on manpower to count hundreds of pieces of linen, the errors caused by humans are considerable. When the statistics are over, the next step is to work hard to find the vulnerabilities of the system. Normally, when a piece of linen is stolen, it is almost impossible for the company to find the thief, let alone get compensation or return it.
The unique EPC serial number in the RFID tag enables companies to identify which piece of linen was lost or stolen, and to know where it was last found. If a piece of linen is taken away from a room in a hotel or hospital, the guest in that room can be charged for the piece of linen to ensure that the company will not suffer losses.
5Provide meaningful customer information
Companies that rent out linen have a unique way to study user behavior, which is to learn about customers through the RFID tags on the linen rented out. The RFID tags sewn into the linen can help record customer information, such as historical renters, renting dates, and renting duration. Keeping these records can help companies understand product popularity, product history, and customer preferences.
6Realize accurate check-in and check-out system management
The process of linen rental is usually very complicated, unless the company can establish a concise concept of storing information such as rental dates, expiration dates, and customer information. The RFID system provides a customer database, which can not only store important information, but also promptly remind the company of small matters such as the expiration date of a certain piece of linen. This function allows companies to communicate with customers about the return date and provide it to customers instead of just providing customers with an assumed return date, which effectively enhances customer relationships. On the contrary, it also reduces unnecessary disputes and increases linen rental income.
[ad_2]