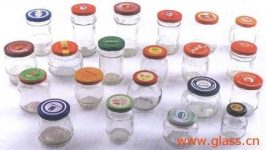
Innovative application of RFID technology in glass bottle manufacturing industry
[ad_1]
The British non-profit organization-Waste and Resources Action Plan (WRAP) launched a project to encourage glass bottle manufacturers, and food and beverage companies to adopt lightweight glass containers to reduce the fuel consumption of glass waste and glass product transportation.
WRAP prompted the British glass industry to produce a new lightweight glass bottle for various liquids such as wine and coffee. However, the existing manufacturing, bottling, and transportation processes are specifically designed for traditional heavier and stronger glass containers, and are not suitable for this new and sustainable design. Light glass, whether empty or full, increases the risk of glass breakage in container manufacturers, beverage bottling plants, and delivery trucks.
In order to identify where the glass is fragile in the bottle factory and improve the efficiency and quality control of the production line in the bottle making process, Irish glass manufacturer Ardagh Glass uses the RFID-based Agent QC system provided by Sensor Wireless. By locating the source of excessive pressure and collision problems between bottles and machines or other bottles, Ardagh can reduce product loss costs and slow down the landfill problem caused by broken glass.
The Agent QC system includes a smart bottle-a replica of an actual glass bottle with an embedded RFID tag with a sensor. By placing the smart bottle in the assembly line, the company can identify the exact location where the glass container will be damaged, according to Wayd McNally, President of Sensor Wireless.
The system also includes a handheld RFID reader for capturing data from the smart bottle on the production line, and data compilation software. In addition, the Agent QC system is also used by beverage companies including Coors, E. & J. Gallo Winery, Coca-Cola and Kirin Beer to track the pressure of the machine on the bottle during capping.
Ardagh Glass is the world’s largest glass manufacturer, producing 12 billion glass bottles every year, with 20 manufacturing plants in Europe and 6,500 employees. Ardagh Glass has included lightweight glass products in the company’s products. The company’s senior customer service director for food, milk and beverages Paul O’Neill said that the company now uses the Agent QC system to track the manufacturing process of four new bottles. O’Neill Refused to disclose the name of the customer who ordered the new bottle.
When Ardagh received an order for the new bottle, the company sent the bottle specifications to Sensor Wireless, and engineers used acrylic plastic to replicate the same smart bottle. The bottle contains a 3-inch long RFID tag and sensor, which circulates in the Ardagh Glass factory together with other bottles. The sensor of the smart bottle measures pressure, impact sound and temperature. The sensor is connected to the battery charging RFID tag, and can use the 900 MHz of the proprietary air interface protocol, or the 2.4 GHz that meets the ZigBee standard to send data.
Using ZigBee technology can send a large amount of data, McNally said, but the 900 MHz signal will be more stable. When smart bottles flow through the assembly line, employees place or hold readers at important locations, such as a transfer point on a manufacturing line, or transport products to a warehouse. In these places, bottle shocks, pressure or temperature changes may damage glass bottles.
Employees can view the data of the smart bottle on the screen of the Sensor Wireless handheld device, store the data in the handheld device, and later connect to the computer via the USB interface to download the data to the Ardagh Glass ERP system. Ardagh uses Sensor Wireless other software to analyze the production line and test whether any modifications on the production line can improve process efficiency.
According to McNally, Ardagh Glass has adopted Agent QC in several factories and has produced new bottles for 4 customers in the past 2 years; the adoption of Agent QC has improved the manufacturing process, limited bottle damage, and identified the point of occurrence of the problem. .
By the end of 2009, McNally stated that Sensor Wireless will add GPS to its smart bottle system, and the label in the bottle can send sensing data through a satellite antenna mounted on a transport truck. This allows the user to understand the location of the accident (such as strong bumps and vibrations) during the transportation of the container.
In addition, Sensor Wireless is also developing an automatic system that enables data to be automatically transmitted to 900 MHz RFID readers or ZigBee nodes on the production line without any manual interference. This requires the installation of low-cost readers or nodes on the assembly line. McNally said that he is still looking for suitable products. Most of the readers are still too large and consume too much power.
[ad_2]