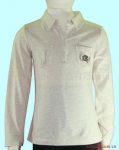
A garment factory in Zhongshan successfully launched the MTS-RFID real-time production management system
[ad_1]
Customer background:
Zhongshan Yifeng Garment Co., Ltd. is a mainstream manufacturer specializing in the production and sales of all kinds of children’s clothes, men’s and women’s casual clothes, etc. The company covers an area of 5,000 square meters, has more than 400 employees, and has more than 500 employees in the newly opened branch. Among them, technical personnel with professional titles of colleges and universities accounted for 20%.
The system data of the Zhongshan Yifeng Garment Factory and the main factory are undoubtedly docked. The main factory places orders uniformly, and the production data of the branch factories is synchronized to the main factory in real time. The management of the main factory grasps the production dynamics of the main factory and the branch in real time. After the branch plant starts to operate, the company’s total number of people will exceed 1,000 processing and production scales. INTI’s MTS-RFID real-time production management system helps Zhongshan Yifeng to efficiently manage the main plant and branch plants.
system introduction:
MTS-RFID is a relatively simple and practical electronic work ticket system, focusing on real-time automatic collection of production progress data of each process on the production site, and piece counting to individuals.takeRFIDRadio frequency identification technology sends the processing information (quantity, time-consuming, process) of each bundle of materials on the production line directly to the database through the read-write equipment to analyze the production flow in the workshop. Help companies obtain real-time production progress and quality information, find and balance on-site production bottlenecks in a timely manner, adjust production plans, grasp delivery dates, and improve production efficiency and productivity. The system adopts C/S+B/S architecture and can use a variety of wired, wireless and handheld terminal devices. RFID credit card machine with display screen, multi-function inquiry.
Advantages of electronic work ticket system:
Accurate and real-time statistics of production data
Real-time automatic statistics of worker production progress and automatic statistics of worker output and working hours of each process.
Eliminate the phenomenon of reselling work tickets and truly reflect the processing data of employees.
Automatically and accurately calculate the employee’s piece rate salary, and can be combined with QC pass rate data.
You can report the actual number of people being processed in each process of each order and each group.
Intuitively and accurately report production progress
Real-time automatic statistics of whether each production order is opened, whether it is in production, and whether it is completed.
Real-time monitoring of on-site production, including the proportion of each process of each order that has been produced.
Real-time statistics of the production speed of each process and section can be used to judge whether the division of labor and machine types is reasonable.
Discover production bottlenecks in real time, monitor the production capacity of each parking space in real time, and balance production line production capacity.
Increase production capacity
After switching to the plug-in card tracking method, each employee can save at least 30 minutes of cutting and sorting barcodes per day compared to barcodes, and this part of the time directly becomes effective production time.
It saves the time and personnel for receiving barcodes, scanning and entering barcodes, and reduces indirect working hours.
Promote process improvement, instantly find out which employee is doing faster in the same process, compare the reason for others to do faster, individual small improvement becomes the improvement of all employees, so that the company’s production efficiency is continuously improved and optimized.
Improve quality management
You can set mid-check, final check-point and quantity by yourself.
QC Zhayi accurately tracks the processing personnel who are assigned to each process to facilitate rework.
The monthly defect rate and ranking of employees can be counted, so that rewards and penalties can be distinguished.
Various bad proportions can be statistically analyzed to promote improvement.
Avoid waste and save costs
According to the actual production situation, the labor price of each process can be analyzed and calculated automatically and reasonably, so as to avoid the imbalance of the labor price setting.
The RFID card can be reused for more than 10 years, saving the cost of work ticket paper and printing work ticket.
Greatly reduce the backlog of materials and reduce the number of refills.
Prevent workers from maliciously damaging and discarding fabrics, reducing losses.
Timely release of information
The production progress of each production order can be released in real time.
Employees can self-check their own processing quantities in real time, increasing the transparency of labor and management.
Can report the production progress of the order to the customer in time.
Software features:
1. Accurate to the minute and second, each employee produces each package of products and each process takes time. Statistics each car platform is equivalent to installing a pair of eyes. Every employee does every move, what they do, how much they do, how fast they do it, who does it fast, who does it? The repaired defective product is high, you know it clearly
2. Real-time discovery of production bottlenecks, real-time monitoring of the production capacity of each parking space, and balance production line production capacity
3. Real-time automatic statistics of worker production progress and automatic statistics of worker output and working hours of each process
4. It can completely prevent workers from falsely reporting output, accurate piece counting, and reasonable and fair wages
5. Save the time for employees to cut work tickets, no need for specialized statistics personnel, reduce personnel, and save wage costs
6. RFID card can be reused for more than 10 years, saving the cost of work ticket paper and printing work ticket
7. Process improvement, instantly discover which employee is doing the same process faster. It takes a few minutes and a few seconds. Compared with others, individual small improvements become improvements for all employees, and the production efficiency of the company is continuously improved and optimized.
8. Product quality control is more complete, with immediate feedback of defective product information on the production line, and timely control and adjustment.
[ad_2]