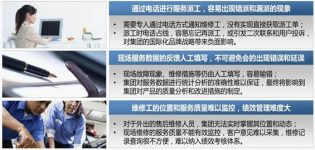
Uboxun helps Haier realize mobile after-sales work order management
[ad_1]
Project Background
Haier Group was founded in 1984. After 30 years of entrepreneurship and innovation, it has developed into one of the world’s largest home appliance manufacturers. It has more than 70,000 employees in 17 countries and users in more than 100 countries and regions around the world. Fierce market competition and rapidly changing market demands, and timely after-sales service are becoming the biggest magic weapon for enterprises to win.
Haier needs to make a comprehensive breakthrough in the original fixed information service system, and directly extend it to each customer, thoroughly opening up the last link of after-sales maintenance services, and allowing customers to experience brand-new mobile after-sales maintenance services. Because of this, the current situation and challenges that Haier faces are:

Customer goals
Haier urgently needs a high-quality maintenance system management tool to conduct standardized service management for maintenance personnel, and greatly improve the efficiency of daily maintenance operations and the competitiveness of the company’s comprehensive services.
*Scan entry of various maintenance product codes
*Real-time understanding of the location of on-site maintenance personnel
*Automatically import maintenance records and generate statistical reports
*Real-time information interaction, automatic dispatch and task scheduling
*Understand customer needs at any time, so as to improve service quality
Program implementation
1. Demand analysis

2. Maintenance flow chart

3. Function application
Haier maintenance personnel log in to the Haier after-sales service system, and after successfully verifying the user information, enter the main interface of work order management, download the work order tasks of the day, and perform operations such as user repair information registration, on-site repair information registration, and query and search operations.

(1) User report for repair
The maintenance staff receives the work order task information issued by the after-sales system through the PDA, and enters the work order management list to select a record for on-site repair processing, and registers the on-site time to check user, product and service information.

(2) Maintenance service management
The maintenance personnel will record the product information, faults, costs and service process after the on-site maintenance. After the maintenance information is saved, the repair information record will be automatically generated; if there is a fee that needs to be paid by card, the card payment interface will pop up and the card payment will be made on site.

(3) Search and apply for spare parts
Search for the inventory information of the designated spare parts of the maintenance machine: the maintenance personnel can enter the search criteria and the spare special number to query the spare parts name, quantity, applicable model, type and other inventory information of the repaired model, and submit the spare parts required for maintenance.
(4) Inquiry about related spare parts
Query related spare parts of the specified model of the work order: Enter the machine model and automatically display the name, quantity, applicable model, type, etc. of the search spare part.

4. System architecture diagram

Program effectiveness
(1) Enterprises can know the location of on-site maintenance personnel at any time, provide standardized services to maintenance personnel, and remotely perform real-time dispatch and task scheduling;
(2) Provide real-time information exchange for the frequently-occurring maintenance problems. The company can know the maintenance status of the maintenance personnel at any time, and provide technical support to the maintenance personnel through the remote knowledge base;
(3) Maintenance personnel can receive new and complete maintenance task information at any time, without wasting a lot of time, returning to the company to collect orders, and can log in to the company’s service system at any time when going out to work, query internal information and mobile office;
(4) Maintenance personnel can also inquire about spare parts inventory in real time on site, and provide customers with consultation on the price of spare parts to improve the quality of maintenance services and increase customer satisfaction;
(5) Maintenance personnel can easily scan and enter various product codes through portable reading devices during on-site maintenance, automatically write maintenance records into the system, and generate statistical reports every month, which greatly improves work efficiency.
Applicable Products
[ad_2]