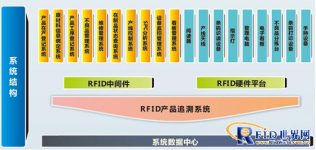
RFID production traceability project of an air-conditioning company
[ad_1]
1. Project background
A certain brand air-conditioning manufacturer currently has more than 48,000 employees. It is a business platform integrating the development, production and service of household and commercial air-conditioning products. Over the years, relying on comprehensive advantages such as brand, technology, quality, and efficient and flexible corporate mechanisms, it has provided high-quality products and services to overseas customers around the world, and has maintained a healthy, stable and rapid growth for a long time.
In recent years, in the face of fierce competition from domestic and foreign competitors, in order to ensure product quality, control product production quality, and enhance the overall competitiveness of enterprises, enterprises urgently need a complete information data management platform to manage and trace product quality. Maintain and deepen its dominant position in the industry. Since 2010, the company has vigorously promoted total quality management (TQM) and promoted the construction of a real-time production data collection system.
2. System description
The system usesRFIDThe tag is equipped with an electronic ID card for each air conditioner. During production, the RFID reader is pre-installed at the bottom of the production line to automatically read the product identity information when passing the work station and upload this information to the management system. Equipped with a computer in the key inspection process, when a defect is detected, click the touch screen defect code to input it, and the system synchronously sends the defect information to the PLC, and drives the defective product sorting line to sort the defective products to the maintenance station. The maintenance personnel use the handheld PDA to read the bad information and quickly carry out targeted maintenance. After the maintenance is completed, the maintenance information is written into the label for reference, and the decision-making analysis data and the kanban function are provided.
3. Construction goals
Solve some of the following problems found in the air-conditioning production process:
At present, on-site data collection adopts the method of “manual record, paper file circulation”. Using this method has problems such as time-consuming, easy data tampering, and untimely data collection;
At present, the manual recording method is adopted for the information collection of the key components used in the product (such as the air compressor) on the spot, and the data binding is inaccurate, which makes it difficult to trace the product quality;
On-site maintenance products are managed by manual records. In order to avoid problems, some personnel do not mark, register, and go online at will during the operation. As a result, the defective product data cannot be counted, and the on-site process improvement lacks accurate basic data.
4. System Architecture
This system is a distributed system, and its network deployment structure is as follows:
Deploy 1 computer in each production line, and deploy 1 RFID on demand at each data collection pointReaderWith 1 set of numerical control indicator lights and 1 set of operation buttons, the system drives the PLC to realize the comprehensive control of the production line, realize the real-time data collection of product data and the real-time elimination of defective products.
Project summary: Through the combined application of RFID technology and automatic control system, the system continuously solves the problem of product data collection and avoids the influx of defective products. At the same time, it also improves operation efficiency and reduces the workload of operators. Improve the level of enterprise informatization, thereby enhancing the competitiveness of enterprises.
[ad_2]