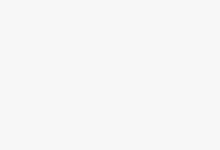
General engine assembly process uses RFID smart bolt tracking
[ad_1]
GM’s production plant in Tonawanda, New York, uses high-frequency passive RFID tags to track the processing process and realize the record of the entire process.inRFID tagsFrom Balluff.
Smart bolts with embedded passive RFID tags are used on some cylinder blocks and cylinder heads of the General Engine Processing Plant in Tonawanda, New York. These cylinder blocks and cylinder heads are mainly used to produce Gen 5 six-cylinder and eight-cylinder engines, and the embedded RFID tags are used to track the assembly process of the engine. At the beginning of 2012, the RFID tracking system was adopted. A total of 284 RFID read-write probes were installed on the Gen 5 production line. The RFID tags were 13.56MHz high-frequency RFID tags, which conform to the ISO 15693 standard.
The engine uses smart bolts with embedded 13.56MHz RFID tags
GM has used RFID technology to track the engine assembly process for ten years. Initially, a passive 13.56 MHz Siemens Simatic RF340T tag was installed on the pallet of the processing plant, and its memory was 8KB to track the assembly process of the engine. First, the engine components are placed on the tray with the RFID tag installed, and the unique ID code of the engine is written into the RFID tag of the tray. The label of the pallet is continuously read and written to record the information of the accessories loaded on it. The RFID tracking solution not only helps to ensure that the factory executes the correct assembly process, but also provides historical information for component recalls.
The factory also installs Balluff passive 13.56 MHz button tags on each processing machine tool. RFID installed on the machineReader, Through the reading of RFID tags, to ensure the rationality of the selection of processing machines.
In 2011, during the production process of the Gen 5 engine, it began to explore the tracking of cylinder block and cylinder head assembly. In order to ensure the normal operation of the assembly line, General Motors and other manufacturers usually have two processing methods: one is to view partial unique codes of text nature and two-dimensional codes through a camera. This technology is called a coding probe. Another method is based on RFID technology, using RFID bolts and fixed RFID readers to track moving parts on the production line.
The program includes 200 RFID read-write probes installed on the cylinder block production line and 84 installed on the cylinder head production line. These readers are distributed in different positions on the production line; the RFID tags are embedded in the bolts and are provided by Balluff.
The customized bolts in the scheme use Balluff BIS M-series 13.56 MHz RFID tags, and the tag memory is 2KB. The middleware used for data transmission in the scheme is also provided by Balluff.
On the right is the Balluff BIS-M read/write head, and on the left is the RFID bolt
When the parts pass the RFID read-write head, the tag data is read and forwarded to the back-end database. After the above process is executed, the read-write head writes the data into the smart RFID bolt, indicating the end of this process.
If an error occurs during the assembly of the cylinder block and cylinder head, employees need to use a handheld reader to read the tag data. The factory uses the Psion Workabout Pro handheld terminal with an embedded RFID reader module.
Smart bolts can be reused. After the cylinder block and cylinder head are processed, the bolts can be removed and the data in its memory can be cleared for recycling.
General Motors plans to continuously apply RFID to the production line of new products.
[ad_2]