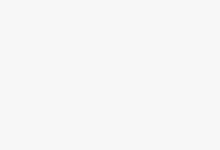
Application of RFID in the supply chain of automobile manufacturing industry
[ad_1]
With the rapid development of the economy and the gradual improvement of people’s living standards, the demand for automobiles continues to increase. All domestic automobile manufacturing industries are facing considerable operating pressure. When market demand is not easy to expand and competition is fierce, in order to survive, companies can only strictly control costs, use higher efficiency to reduce unnecessary waste, and improve quality to increase competitiveness.
1. The JIT management model promotes the refined development of the automobile manufacturing industry
JIT—Just? In? Time is a production method implemented by Toyota Motor Corporation of Japan in the 1960s. It refers to
The necessary parts are delivered to the production line in the necessary quantity at the necessary time, and only the required parts, only in the required quantity, and only in the exactly required time, are delivered to the production line. The core of this production method is to pursue a production system without inventory, or a production system that minimizes inventory.
At present, advanced enterprise management theories and practices are developing in the direction of refinement, and just-in-time (JIT) management has been widely used in modern automobile manufacturing. In the second half of the 20th century, the entire automobile market has entered a new stage of diversification of market demand, and the requirements for quality are getting higher and higher. How to effectively organize the production of multiple varieties in small batches, and eliminate the waste of excess manufacturing and waiting for work. The waste of materials, the waste of handling, the waste of processing itself, the waste of inventory and the waste of manufacturing substandard products will affect the competitiveness and survival of the enterprise.
1. JIT uses “pull” to control the production site
JIT emphasizes demand pull and on-site control. In terms of production site control technology, the basic principle of JIT is to adopt “pull-type” production, to deliver goods from the former process to the latter process in the traditional production process, and to change the latter process to pick up the goods according to the “kanban” to the previous process. This pull system reduces inventory to a minimum, thereby reducing manufacturing costs.
2. The prerequisite for realizing JIT — Logistic design and rationalization of flow design is the ultimate way to achieve cost reduction goals. Specifically, all equipment, personnel, and parts inside and outside the production line are allocated and distributed in the most reasonable manner. In the most timely manner.
To better implement JIT, it is necessary to optimize the layout of the production line, that is, streamlining. It provides an important foundation for meeting the production requirements of frequently receiving parts and products in the subsequent process and the balanced production of “multi-variety, small batch”. However, this rather complicated way of receiving products will inevitably increase the amount of transportation operations and transportation costs, especially if the transportation is inconvenient, it will affect the smooth progress of just-in-time production.
The design of the assembly line is considered to be S-shaped or U-shaped, increasing the flexibility of the layout, as short as possible, and reducing the transportation time. Reasonable arrangement of equipment, especially the “combined U-shaped production line” formed by connecting U-shaped units, can greatly simplify transportation operations and increase the number of parts and products transportation per unit time, but the transportation cost does not increase or increases very little, and it is a small batch Frequent transportation and single-piece production and single-piece delivery provide the basis. see picture 1.
3. Kanban controls the production process
The non-order production environment requires production requirements and simplified business processing procedures. JIT-based enterprise resource planning (ERP) automatically generates production plans to meet demand, and the final assembly plan usually uses electronic kanbans to pull materials. The main carrier of information in the kanban management mode is the kanban, which records the part number, time of order, part name, storage location of the part, number of parts, model of the station equipment used, etc., which are used as the purchase of each process, Evidence of delivery, transportation, production, and acceptance. In the Kanban management mode, every supply of materials is a reasonable supplement to actual consumption, which fully reflects the principle of just-in-time logistics.
ERP supports simple production business processes, and can simply record the materials received in inventory or the quantity completed between processes. This information can be used for barcode processing or other data collection systems. It can use assembly pull-type backflushing material resources, or process pull-type backflushing material (also called synchronous backflushing). Backflushing can specify locations, assembly lines, manufacturing units, workshop locations, and backflush replacement materials. ERP also provides automatic trigger backflushing for sales and shipments.
2. Application of RFID in the supply chain of automobile manufacturing industry
Supply chain operations include procurement, storage, manufacturing, packaging, loading and unloading, transportation, circulation processing, distribution, and sales to service. However, because all links in the movement of actual objects are in a moving and loose state, information and direction often change in space and time with actual activities, which affects the availability and sharing of information. RFID (Radio Frequency Identification) can effectively solve the input/output of various business operation data in the supply chain, control and tracking of business processes, and reduce the error rate.
At present, RFID technology is used to monitor the production process in the welding, painting and assembly production lines of many automobile production plants. In the welding production line, use high-temperature, dust/metal, anti-magnetic, reusable active encapsulated RFID tags to monitor welding production operations through automatic identification of work parts; use waterproof and paint-resistant RFID tags in the painting workshop, right Car parts and complete vehicles are monitored to complete the painting work according to the schedule, while reducing pollution; on the assembly line, according to the production plan, production schedule and sequence compiled by the supply chain planner, by identifying the information in the RFID tag , Complete mixed-flow production.
Especially on the assembly line that adopts the JIT just-in-time production method, the raw materials and parts must be delivered to the work station on time. After the use of RFID technology, it is possible to quickly and accurately find the raw materials and parts required by the workstation from a wide range of inventory by identifying electronic tags. RFID technology can also help managers send replenishment information in a timely manner based on the production schedule, achieve a balanced and stable production line, and also strengthen quality control and tracking.
3. RFID improves the efficiency of the automotive manufacturing supply chain
China is a manufacturing base with hundreds of thousands of manufacturing companies. Within the company, there will be islands of information in various links. Due to inaccurate and inaccurate data collection in the procurement, production, inventory, transportation, and sales processes There is even a certain delay. For the decision makers of the enterprise, the focus on RFID may be more on the application level.
Next, take the implementation process of JIT management in an automobile manufacturing group as an example to see the pulling process of production materials.
(1) Pull process
Start with sales orders to drive planning, logistics, supply, and production.
(2) Workshop production materials pull
Large-volume accessory parts: direct delivery station, advantages: minimize inventory, achieve zero inventory.
Standard parts: use kanban to pull, the production station uses the material box, and the material box is placed on the sliding material rack. Advantages: reduce labor intensity and improve work efficiency.
Optional parts and non-universal parts: use planned marshalling for distribution and supply.
[ad_2]